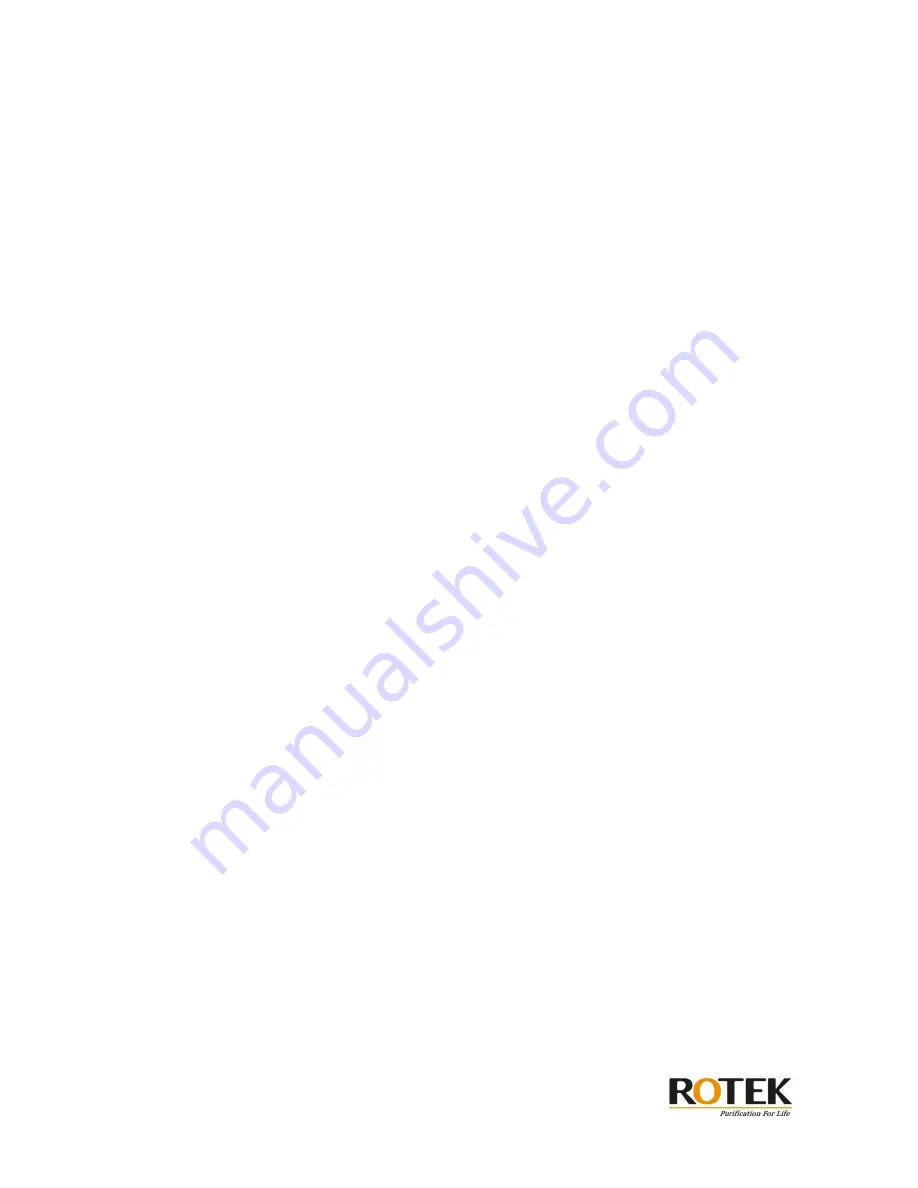
17
2.
Low-flow rate pumping. Pump mixed, preheated cleaning solution into the housing at a low flow
rate of 5-10 litres per minute at low pressure (<120kPa) to displace the process water. Use only
enough pressure to compensate for the pressure drop from feed to concentrate. The pressure should
be low enough so that little to no permeate is produced. A low pressure minimizes re-deposition of
dirt on the membrane. Dump the concentrate, as necessary, to prevent dilution of the cleaning
solution.
3.
Re-circulate. After the process water is displaced, cleaning solution will be present in the
concentrate stream and this can be recycled to the cleaning solution tank. Recycle the cleaning
solution for 15 minutes or until there is no visible colour change. If a colour change occurs, dispose of
the cleaning solution and prepare a new solution as described in step 2.
4.
Soak. Turn the recirculation pump off and allow the elements to soak for 1-15 hours (soaking
overnight will give best results). To maintain temperature during an extended soak period, use a slow
recirculation rate (2-5 litres per minute). Soak time will vary depending on the severity of the fouling.
For lightly fouled systems, a soak time of 1-2 hours is sufficient.
5.
High-flow pumping. Recirculate the cleaning solution through the membranes at 15-20 litres per
minute for 45 minutes. This high flow rate flushes out the foulants removed from the membrane
surface by the cleaning. If the elements are heavily fouled, using a higher flow rate is possible up to
the maximum pressure drop across the membrane permissible (check with membrane manufacturer’s
data sheets). With higher flow rates, excessive pressure drop may be a problem. The maximum
recommended pressure drops for most common membranes are 100kPa per element or 340 kPa per
multi-element housing, whichever value is more limiting.
6.
Flush out. Clean RO permeate water is preferred for this stage. If clean RO permeate water is not
available, pre-filtered raw water can be used for flushing out the cleaning solution unless there will be
corrosion problems (e.g., stagnant seawater will corrode stainless steel piping). To prevent
precipitation of any remaining contaminants, the minimum flush out temperature is 20°C. The system
should be flushed for 1 hour.
7.
Re-start the system. The RO elements and the system need to stabilize before taking any
performance data. The stabilization or normalisation period will vary depending on the severity of the
fouling. To regain optimum performance, it may take several cleaning and soak cycles.RO Membrane
Cleaning Procedures for inorganic material fouling
1.
Prepare the cleaning solution as listed below
* Preferred 2.0% (wt) Citric Acid PH 2, 45°C maximum
* Alternate Muriatic Acid
* Alternative 1.0% Na2S2O4
NOTE!
●
(wt) Denotes weight percent of active ingredient.
●
Cleaning chemical symbols in order used: HCI is hydrochloric acid (Muriatic Acid).
2.
Low-flow rate pumping. Pump mixed, preheated cleaning solution into the vessel at a low flow
rate of 5-10 litres per minute at low pressure (<120kPa) to displace the process water. Use only