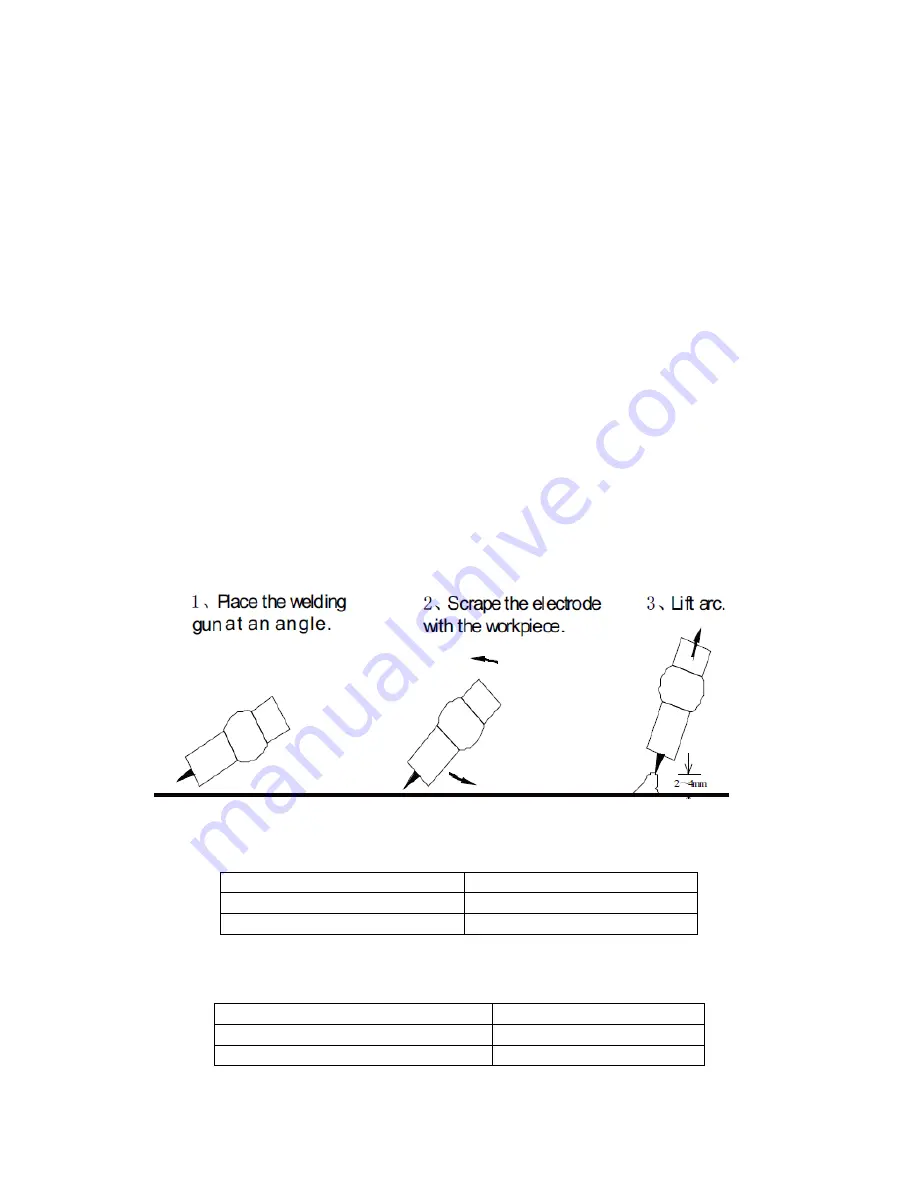
25
(4)
The tungsten must be ground to a blunt point in order to achieve optimum welding
results. It is critical to grind the tungsten electrode in the direction the grinding wheel is
turning.
(5)
Install the tungsten with approximately 3mm to 7mm sticking out from the gas cup,
ensuring you have correct sized collet.
(6)
Tighten the back cap
(7)
Commence welding. If necessary, readjust the Weld Current control to obtain the welding
condition re-quired.
(8)
After completion of welding the Power Source should be left turned ON for 2 to 3 minutes.
This allows the fan to run and cool the internal components.
(9)
Switch the ON/OFF Switch (located on the rear panel) to the OFF.
•
3.3.3. TIG Welding Fundamentals
Stricking the arc for TIG Operation: when tungsten electrode touches the workpiece, the
short-circuit current is only 28A. After generating arc, current can rise to the setting welding
current. If the tungesten electrode touches the workpiece when welding, the current will drop to
5A within 2s, which can reduce tungsten waste, prolong the using life of the tungsten electrode,
and prevent tungsten clipping.
Scraping Arc
Tungsten Electrode Current Ranges
Electrode Diameter
DC Current
1.0mm
25 - 85
1.6mm
50 - 160
Shielding Gas Selection
Alloy
Shielding Gas
Carbon Steel
Welding Argon
Stainless Steel
Welding Argon