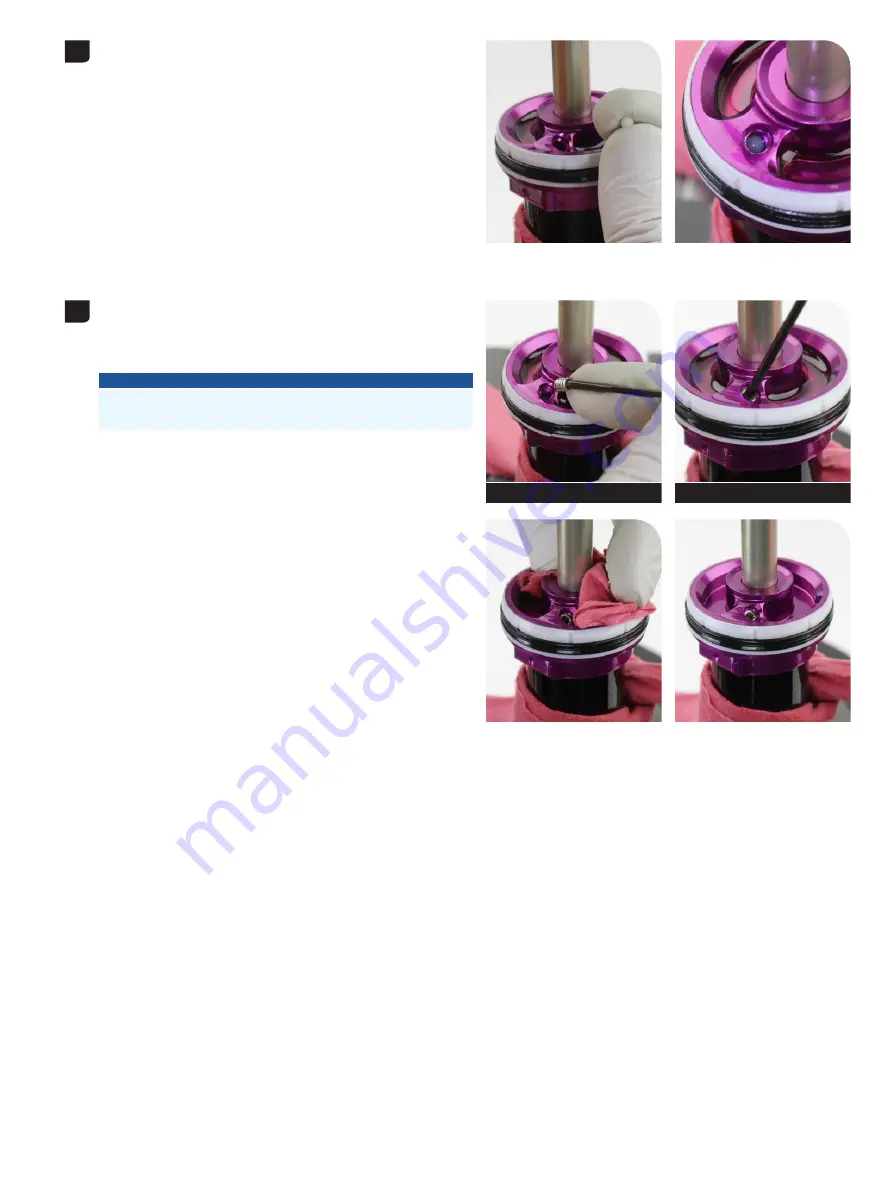
61
Shock Assembly and Bleed
Allow oil and air bubbles to escape from the bleed port in the seal
Allow oil and air bubbles to escape from the bleed port in the seal
head / air piston.
head / air piston.
Insert a NEW nylon compression ball into the bleed port. Allow it to
Insert a NEW nylon compression ball into the bleed port. Allow it to
settle into place below the threads.
settle into place below the threads.
Install the bleed screw into the bleed port and thread it in until you feel
Install the bleed screw into the bleed port and thread it in until you feel
it contact the nylon compression ball, then tighten the bleed screw an
it contact the nylon compression ball, then tighten the bleed screw an
additional ½ turn.
additional ½ turn.
Clean the oil from the seal head.
Clean the oil from the seal head.
NOTICE
Overtightening the bleed screw can damage the nylon compression
ball. If the nylon compression ball is damaged, it must be replaced.
6
7
2 mm
2 mm