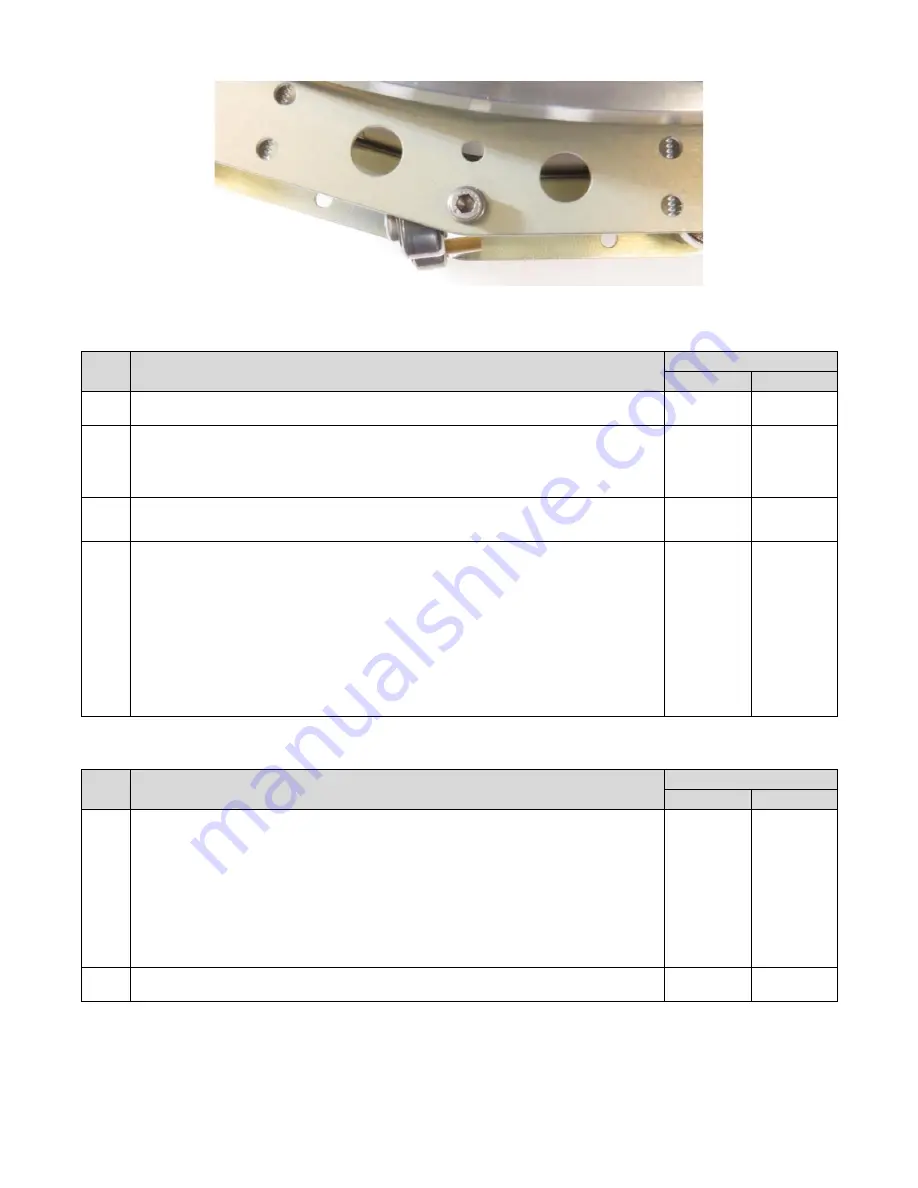
Copyright PSC
2000781K MkII MLB Operating Procedure
Page 66 of 68
Figure 17-3: Visually aligned LCT pair
17.3 Mating the Lightband
Step
Procedure
Date & Initials
Tech.
QA
17.3.1
Upper and Lower Rings shall be aligned per Step 7.1.11.
17.3.2
Prepare cable tie tool
1. Disable cut-off feature (if present).
2. Ensure force setting does not exceed cable tie break strength. If using
referenced tool,
set to ‘8’.
17.3.3
Place one cable tie around each LCT pair and pull until just taut. Do not
compress the Separation Springs.
Measure the distance between Upper and Lower Ring flanges (A and B in
Figure 17-1) next to each LCT and record in Table 17-1. For reference the
nominal uncompressed distance is 2.13 inch for the dimension shown in Figure
7-7.
Lightly tighten each cable tie until the flange distance measures 2.00 to 2.05
inch at every LCT (1).
Note: Failure to evenly compress the Lightband increases probability of
breaking cable ties.
1) If using a combination of weight and LCTs to compress the Lightband, the initial flange distance will be less
than stated above. Record the minimum initial reading and adjust all LCTs until they are within 0.05 inch.
Step
Procedure
Date & Initials
Tech.
QA
17.3.5
To compress the Lightband tighten the cable ties in maximum increments of
0.05 inch. Work around the Lightband and record all measurements in Table
17-1 after each round of adjustments. The flange distance at all LCTs shall
agree within 0.05 inch prior to compressing further.
If a cable tie is over-tightened or breaks, remove and replace the cable tie.
Repeat this iterative process until the flange distance at every LCT complies
with the pre-Stow distance in Figure 7-7.
17.3.6
Proceed to section 8 to Stow the Lightband.
-----N/A----- -----N/A-----