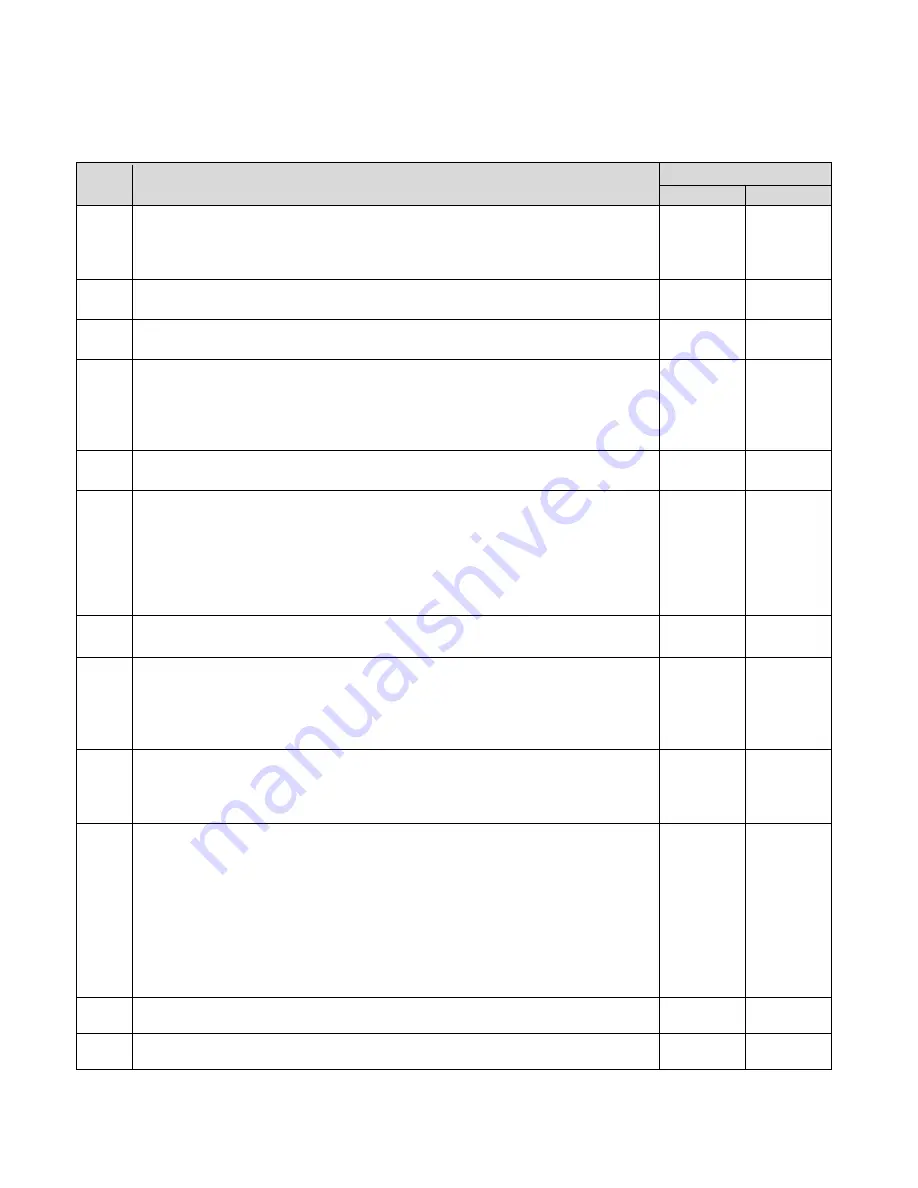
Copyright PSC
2000781K MkII MLB Operating Procedure
Page 58 of 68
12.
Horizontal Integration (Optional)
Horizontal integration may be necessary due to space vehicle (SV) and/or launch vehicle (LV) limitations. This
section describes the steps and precautions necessary to ensure proper Stowing of the Lightband.
Step
Procedure
Date & Initials
Tech.
QA
12.1.1
Is an isolation system attached to the Lower Ring? If so, it may be easier to
Stow the Lightband with Transition Rings, remove the Transition Rings, and
then bolt the already mated Lightband to the LV and SV. Contact PSC for
details.
-----N/A----- -----N/A-----
12.1.2
The Lower Ring, mounted to the LV, shall be perpendicular to level within
±0.2°. See Figure 12-1.
12.1.3
Micro-adjustment of the SV height, pitch and roll is essential. This can be
accomplished with a hydro-set, Vernier screws, turnbuckles, etc.
12.1.4
The structure supporting the SV (crane, tilt-cart, etc.) shall have sufficient
compliance to allow for SV movement when Stowing. The vertical stiffness
shall be less than 2,000 lb/in. Consider and verify compliance in all 6 degrees
of freedom (DOF). For instance, will the crane stretch, the tilt cart compress or
even be lifted up? Can the SV pitch, roll or yaw as necessary?
A load cell shall be installed in-line with the SV support structure. See Figure
12-1 and Figure 12-3.
12.1.6
Move the SV close to the LV until the tips of the Separation Springs are close
to the bottom edge of the Upper Ring (<0.5 inch) but not yet overlapping. Align
the Upper Ring to the Lower Ring in translation and rotation. See step 7.1.11
for alignment features. Ensure the Separation Springs will not be inhibited
from engaging their corresponding holes in the Upper Ring flange. It is
essential to align all 6 SV DOF prior to actually compressing the Lightband.
See Figure 12-2.
12.1.7
Verify no part of the Lower Ring is contacting the Upper Ring and then record
the SV load cell reading: _______________
12.1.8
Move the SV closer to the LV until the conical tips of the Separation Springs
are <0.10 in from the Upper Ring flange. All Separation Spring tips shall be
centered in their corresponding Upper Ring flange holes. The Lower and
Upper Rings shall be parallel within 0.02 inch. Adjust the SV alignment as
necessary. The load cell shall remain within 10 lb of the step 12.1.7 reading.
12.1.9
Move the SV closer to the LV until the conical tips of all Separation Springs
are engaged and centered in the Upper Ring flange holes. The Lower and
Upper Rings shall be parallel within 0.01 inch. Adjust the SV alignment as
necessary. The load cell shall remain within 10 lb of the step 12.1.7 reading.
12.1.10
Slowly compress the Lightband. See Section 17 if using LCTs. Continually
monitor the load cell. It shall remain within 10 lb of the step 12.1.7 reading.
When fully compressed, the distance between Lightband flanges shall
conform to Step 7.1.14. Also verify that the flange distance at the top, bottom,
left and right of the Lightband are within 0.005 inch of one another. See Figure
12-3.
An improperly aligned SV may translate (up, down, left or right) or rotate
(pitch, roll or yaw) during the Stow process, requiring additional power that the
Lightband motors cannot generate. Proper alignment is essential.
12.1.11
Record final load cell reading: ________________
12.1.12
Return to section 8 to Stow the Lightband.
-----N/A----- -----N/A-----