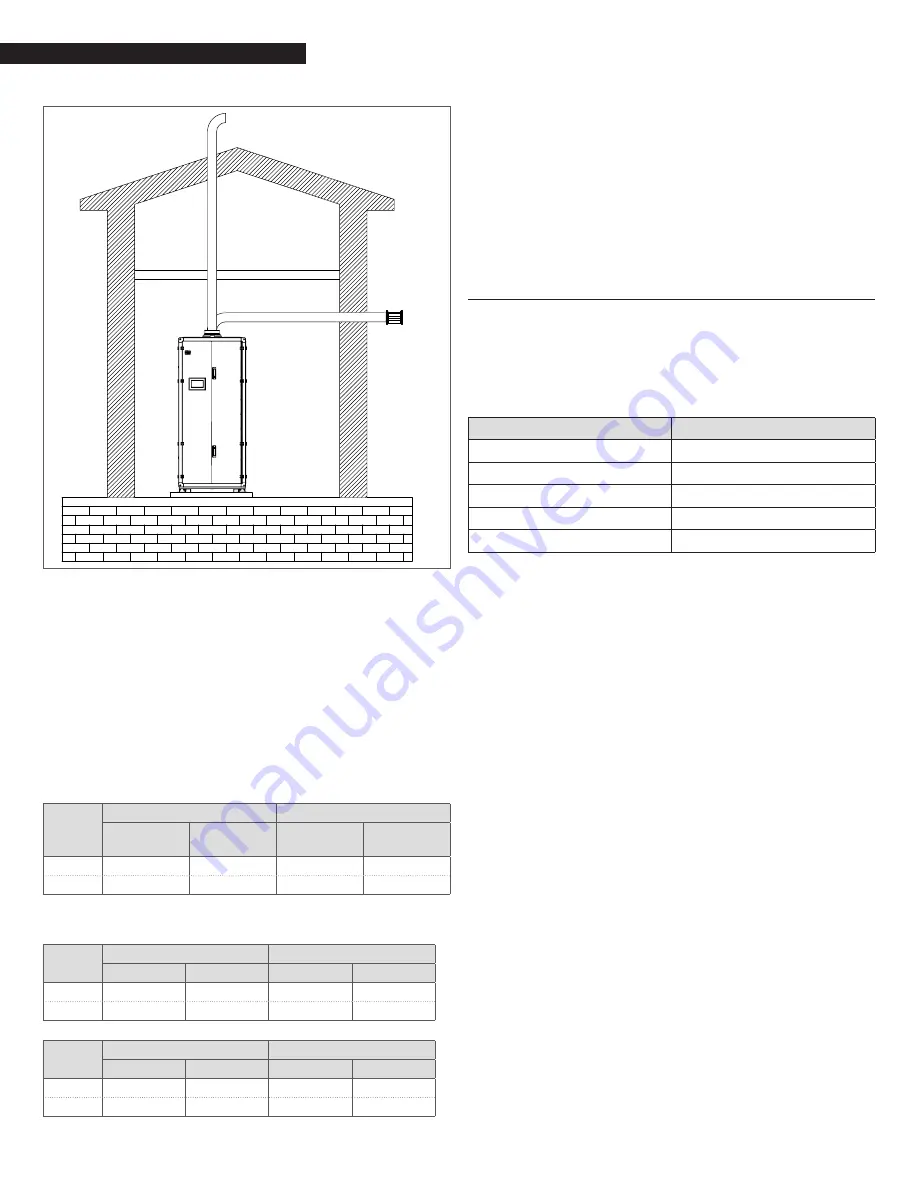
26
INSTALLATION
BOILER
EXHAUST
Fig. 35
Exhaust Located on Side Wall
− It is not recommended to terminate vent above any door
or window, condensate can freeze causing ice formations.
− Do not use chimney as a raceway if another boiler or
fireplace is vented into or through chimney.
− Because the unit is capable of discharging low temperature
exhaust gases, the flue must be pitched back towards the
unit a minimum of 1/4” per foot to avoid any condensate
pooling and to allow for proper drainage.
− While there is a positive flue pressure during operation,
the combined pressure drop of vent and combustion air
systems must not exceed the following equivalent length:
Model
PIPE SIZE - 8”
PIPE SIZE - 10”
MAX. equiv.
(m)
MAX. equiv.
(ft)
MAX. equiv.
(m)
MAX. equiv.
(ft)
AR 3000
21
70
30
100
AR 4000
12
40
30
100
Fittings as well as pipe lengths must be calculated as part of the
equivalent length, according to the following table:
Model
45° ELBOW - 8”
45° ELBOW - 10”
equiv. (m)
equiv. (ft)
equiv. (m)
equiv. (ft)
AR 3000
2.1
7
1.5
5
AR 4000
2.1
7
1.5
5
Model
90° ELBOW - 8”
90° ELBOW - 10”
equiv. (m)
equiv. (ft)
equiv. (m)
equiv. (ft)
AR 3000
2.7
9
1.8
6
AR 4000
2.7
9
1.8
6
− For a natural draft installation the draft must not exceed -
0.25” w.c.
− These factors must be planned into the vent installation. If
the maximum allowable equivalent lengths of piping are
exceeded, the unit will not operate properly or reliably.
− For Massachusetts installations, contact companies able
to provide vent systems which conform to all applicable
requirements for installations within the Commonwealth of
Massachusetts.
− For installation of multiple boilers, common venting shall be
sized based on the data of “Appendix H - Venting Size Data”.
4.16
Combustion Air
Air supply is a direct requirement of ANSI 223.1, NFPA-54, CSA
B149.1 and local codes. These codes should be consulted before a
permanent design is determined.
Array boilers can utilize combustion air from the space in which
they are installed, or utilize combustion air ducted directly to the
unit. Ventilation air must be provided in either case.
Material
Standard
ABS
ANSI/ASTM D1527
PVC Schedule 40
ANSI/ASTM D1785 or D2665
CPVC Schedule 40
ANSI/ASTM F441
Polypropylene
ULC S636
Single wall galvanised steel
26 gauge
In cold climates it is essential to provide a motorized air inlet
damper to control the supply of combustion air and prevent
nuisance condensation.
The combustion air must be free of:
− Permanent wave solutions;
− Chlorinated waxes/cleaners;
− Chlorine-based swimming pool chemicals;
− Calcium chloride
− Sodium chloride used for water softening;
− Refrigerant leaks;
− Paint or varnish removers;
− Hydrochloric acid/muriatic acid;
− Cements and glues;
− Antistatic fabric softeners used in clothes dryers;
− Chlorine-type bleaches, detergents, and cleaning solvents
found in household laundry rooms;
− Adhesives used to fasten building products and other
similar products.
To prevent contamination do not connect the combustion air inlet
and exhaust near:
− Dry cleaning/laundry areas and establishments;
− Swimming pools;
− Metal fabrication plants;
− Beauty shops;
− Refrigeration repair shops;
− Photo processing plants;
− Auto body shops;
− Plastic manufacturing plants;
− Furniture refinishing areas and establishments;
− Remodeling areas;
− Garages with workshops
Whenever the environment contains these types of chemicals,
combustion air MUST be supplied from a clean area outdoors for the
protection and longevity of the equipment and warranty validation.
The more common methods of combustion air supply are outlined
Summary of Contents for Array AR 3000
Page 1: ...cod Doc 0079789 rev 5 09 2018 Array AR 3000 AR 4000 US INSTALLATION AND OPERATION MANUAL...
Page 39: ...39 SHUTDOWN 39 APPENDIX WIRING DIAGRAM DEPENDENT 5 6 7 8 RIGHT DOOR...
Page 69: ...69...
Page 70: ...70...
Page 71: ...71...