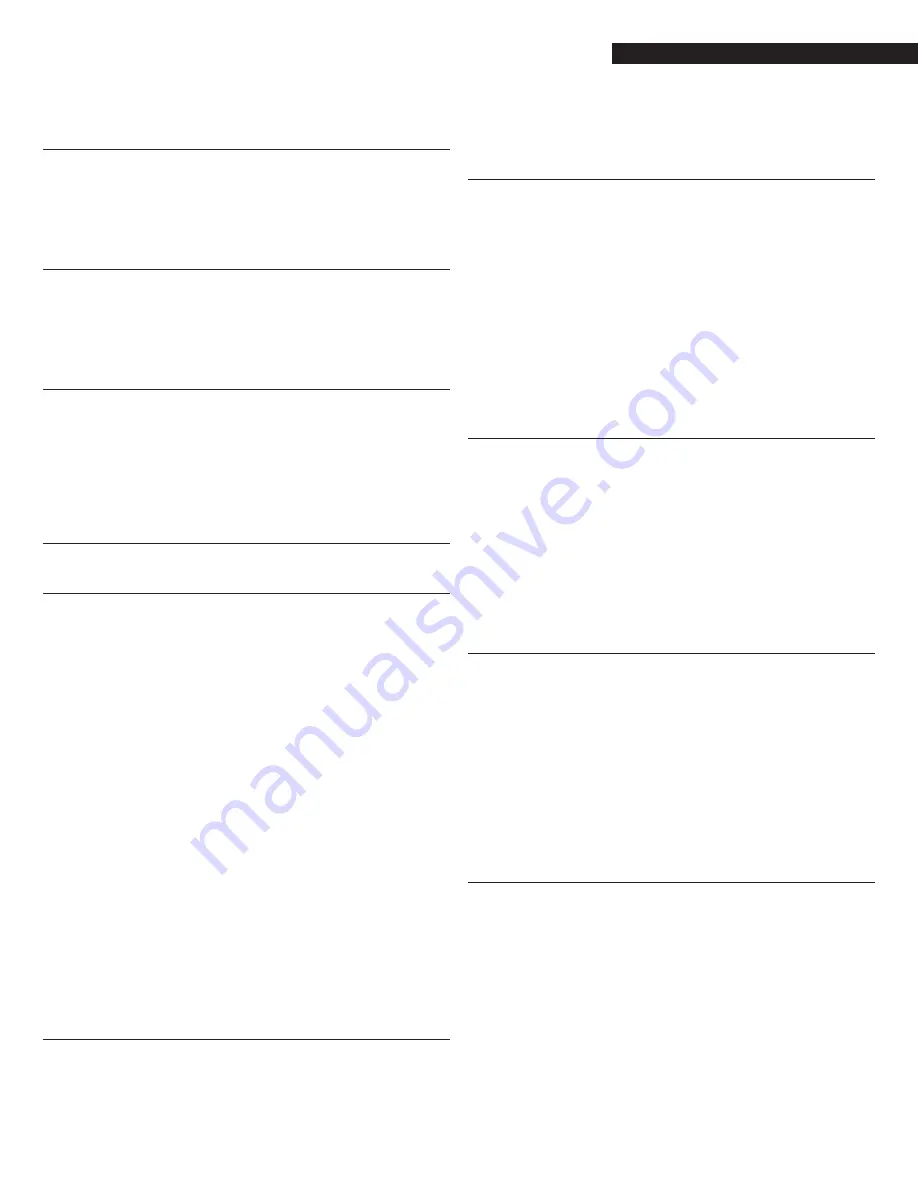
27
COMMISSIONING
in the following sections.
4.16.1
Combustion Air From Outside the Building
Air supplied from outside the building must be provided through two
permanent openings. For each unit these two openings must have a
free area of not less than one square inch for each 4000 BTUs input of
the equipment. The free area must take into account restrictions such
as louvers and bird screens.
4.16.2
Combustion Air From Inside the Building
When combustion air is provided from within the building, it must
be supplied through two permanent openings in an interior wall.
Each opening must have a free area of not less than one square inch
per 1000 BTUH of total input. The free area must take into account
any restrictions, such as louvers.
4.16.3
Ducted Combustion Air
For ducted combustion air installations, the air ductwork must then be
attached directly to the air inlet connection on the sheet metal enclosure.
In a ducted combustion air application, the combustion air ducting
pressure losses must be taken into account when calculating the
total maximum allowable venting length.
For additional details, see “Appendix I - Exhaust terminals and Air
inlet Clearances”.
5
COMMISSIONING
5.1
Introduction
Before starting the boiler, the user must be correctly instructed by
the installer, on how to operate the heater, in particular:
− Make sure that the user understands that combustion air
and ventilation openings must not be restricted, closed, or
modified in any way.
− Make sure that the user is informed of all the special measures
to be taken for combustion air inlet and discharging flue
gases, and that these must not be modified in any way.
− Make sure that the user keeps this manual and all other
documentation included with the boiler.
− Make sure that the user understands never to tamper with
gas control settings and the risk of fire, explosion, or CO
poisoning should an unauthorized individual do so.
− Make sure that the user knows how to adjust temperatures
and controls.
9
WARNING:
Do not attempt to dry fire the unit. Starting the unit
without a full water level can seriously damage the unit and
may result in injury to personnel or property damage. This
situation will void any warranty.
9
CAUTION:
All of the installation procedures in “Installation”
page 13 must be completed before attempting to start the unit.
5.2
Filling the Condensate System
The condensate system must be filled with water according to the
Section 2.9.
9
WARNING:
At the Start-up and after prolonged shutdown of
the boiler, the condensate traps and the syphon must be filled
with water prior to restarting it, otherwise combustion gases
will enter the room with a risk of an excessive level of carbon
monoxide.
5.3
Filling the Boiler Heating System
To fill the heating system, proceed as follows:
− Open any automatic air vents in the heating system.
− Open the fill valve and proceed to fill the heating system
and boiler until the pressure gauge (shown on Fig. 43),
reads the pressure for which the heating system is sized.
The heating system water pressure must be higher than 7.5
PSI.
− Check that there is no water leaking from the fittings. If
there is, the leaks must be repaired.
− Check the pressure gauge during the purging process. If the
pressure has dropped, re-open the fill valve to bring the
pressure back to the desired value.
5.4
Warnings Concerning the Gas Supply
When starting up the unit for the first time the following must be
checked:
− That the unit is supplied with the type of fuel that it is
configured to use.
− That the gas supply system is provided with all the safety
devices and controls required under current national and
local codes.
− That the vent and combustion air terminals are properly
connected and free from any blockages.
− That the condensate drain tube is properly connected.
5.4.1
Confirming the Unit’s Gas Type
The type of gas and the gas supply pressure that the unit is set up
for is listed on the rating label. The
Array
Series boilers can operate
using one of the following two gases:
NATURAL GAS
− Maximum supply pressure = 20” w.c. (50.0 mbar).
− Minimum supply pressure = 4.0” w.c. (10.0 mbar).
PROPANE (LP) GAS
− Maximum supply pressure = 20” w.c. (50.0 mbar).
− Minimum supply pressure = 8” w.c. (19.9 mbar).
5.4.2
Gas Type Conversion
If the gas available at the installation site is not the type the
boiler is configured to use, the boiler must be converted. Special
conversion kits are available for this purpose. The gas conversion
procedure may be found in Section “4.12.4 Gas Type Conversion”
page 19. Conversion must be carried out by a qualified technician.
Summary of Contents for Array AR 3000
Page 1: ...cod Doc 0079789 rev 5 09 2018 Array AR 3000 AR 4000 US INSTALLATION AND OPERATION MANUAL...
Page 39: ...39 SHUTDOWN 39 APPENDIX WIRING DIAGRAM DEPENDENT 5 6 7 8 RIGHT DOOR...
Page 69: ...69...
Page 70: ...70...
Page 71: ...71...