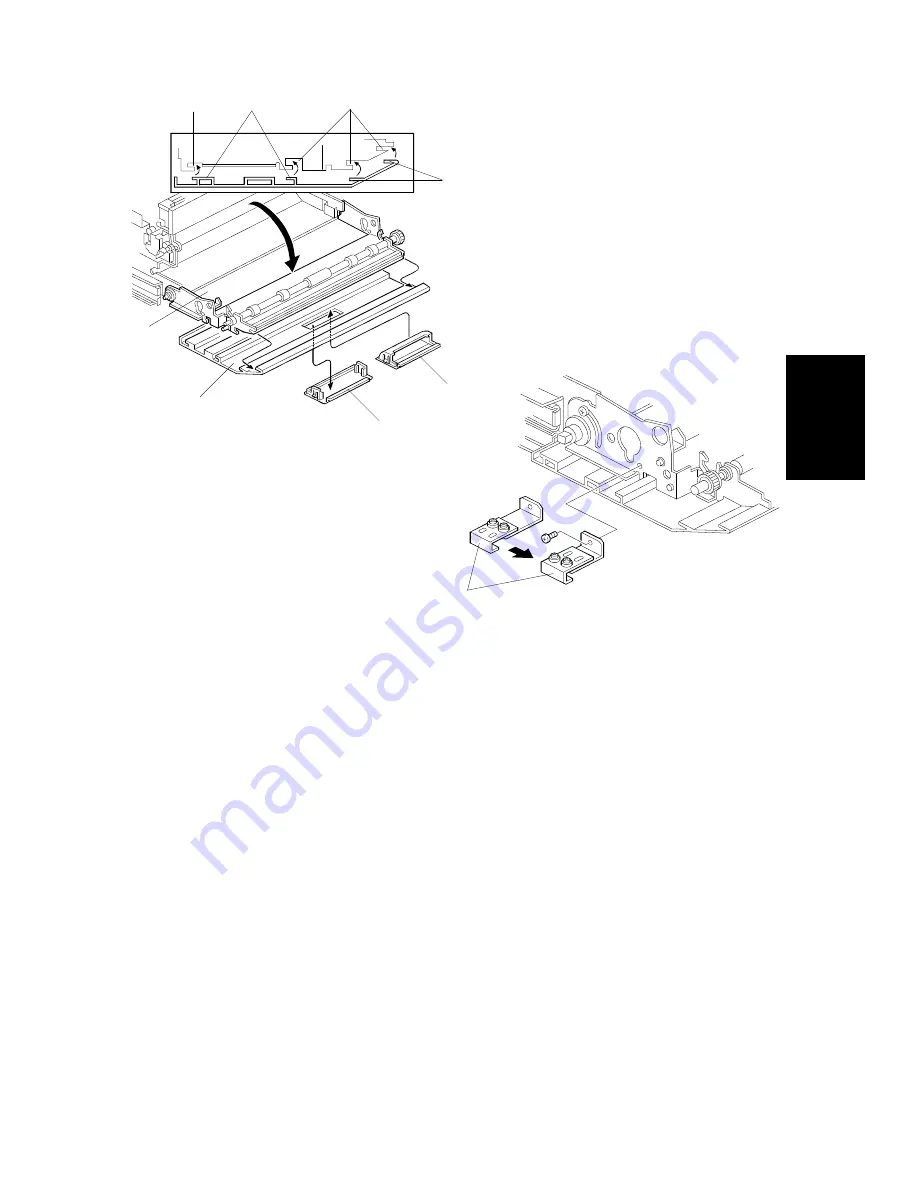
16. Replace the 3rd cover cap [A] of the 3rd cover with the 3rd roll grip [B].
NOTE: The 3rd cover open lever should come out of the 3rd roll grip [B]
for the next step.
17. Open the 3rd roll feed unit [C] and install the 3rd cover [D] (Hook the
projections [E] onto the cutouts [F] in the roll feeder side plates.).
18. Change the screw positions of the 3rd cover securing plates [G] as
shown and install the 3rd cover securing plates (1 screw each).
[D]
[A]
[B]
[C]
[E]
[F]
[E]
[F]
A613I508.wmf
[G]
A613I509.wmf
Inst
allat
ion
25 July 1996
ROLL FEEDER INSTALLATION PROCEDURE (A613)
3-19
Summary of Contents for FW870
Page 3: ...SECTION 1 OVERALL MACHINE INFORMATION...
Page 15: ...SECTION 2 DETAILED SECTION DESCRIPTIONS...
Page 61: ...SECTION 3 INSTALLATION...
Page 86: ...SECTION 4 SERVICE TABLES...
Page 139: ...SECTION 5 REPLACEMENT AND ADJUSTMENT...
Page 188: ...SECTION 6 TROUBLESHOOTING...
Page 205: ...34 33 32 31 30 29 45 38 37 35 40 44 43 42 41 36 39 26 47 28 27 46 64 66 65...