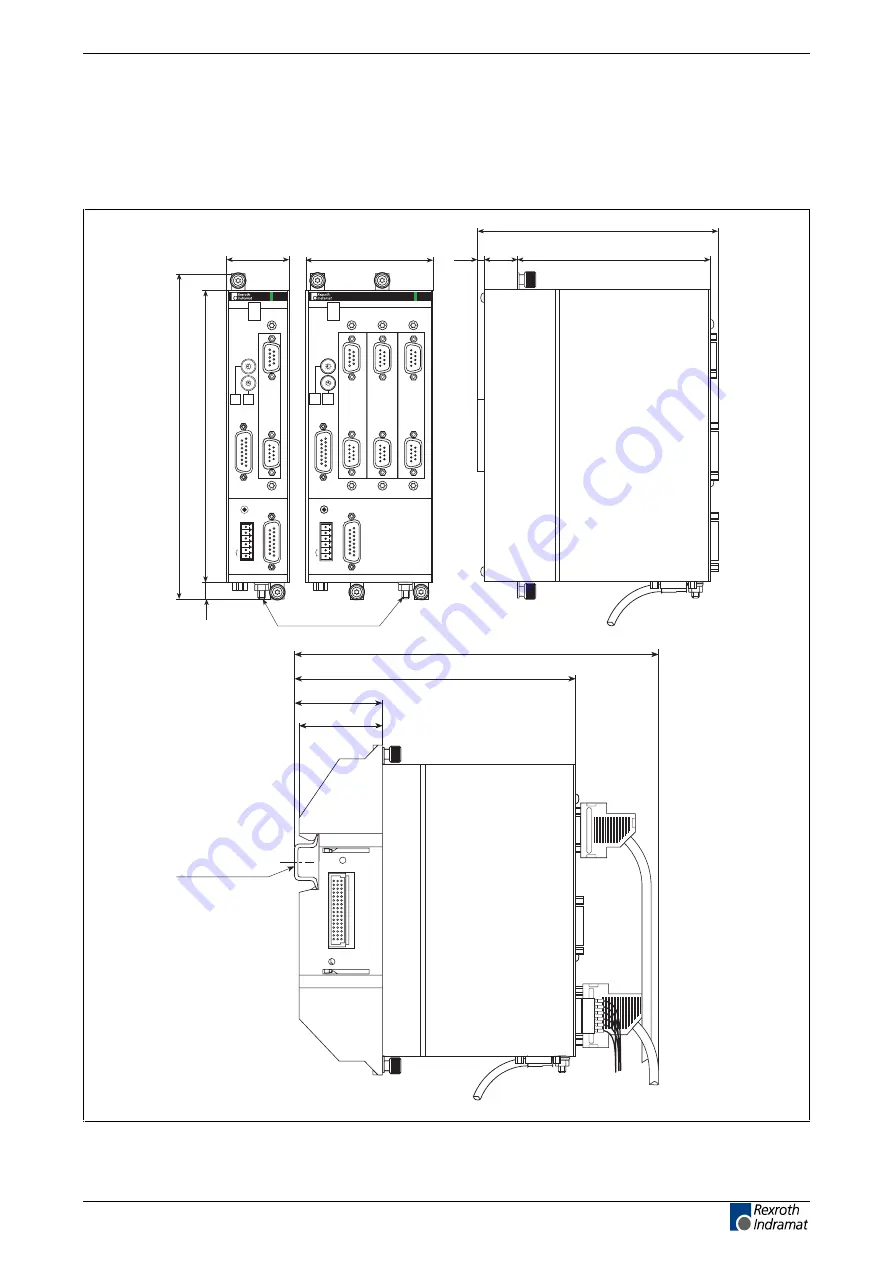
RECO PLC ISP200-R/G2
Technical Data
4-3
DOK-CONTRL-MTS-R0*.2G2-PR01-EN-P
4.7 Dimensions
MTS-R01.2 and MTS-R02.2
IBS-
MASTER
X64
X60
MTS-R_Maß.FH7
0
5
1
6
2
7
3
8
4
9
0
5
1
6
2
7
3
8
4
9
RS 422
X41
X40
RS 232C
X36
X35
IBS-
MASTER
X64
X60
0
5
1
6
2
7
3
8
4
9
0
5
1
6
2
7
3
8
4
9
DEVICE-NO
X16
X10
RESET
H1
PROG
COM
X1
+24V
0V
NC
WD
1
2
3
4
5
6
U1
U2
U3
MTS-R02.2
8
NC
11
192
214
41,5
83,7
4,5
22
128
159
Top hat rail
TS 35 x 17 x 15
56
54,5
182,5
ca. 230
MTS-R01.2
RESET
H1
PROG
U1
X16
COM
1
2
3
4
5
6
X1
+24V
0V
NC
WD
DEVICE-NO
X10
8
RECO
NC
M5 grounding bolt
RECO
MTS-R_Maß.FH7
Fig. 4-1:
Dimensional drawing of MTS-R01.2 and MTS-R02.2
Summary of Contents for DURADRIVE SYSTEM200
Page 1: ...Project Planning Manual DOK CONTRL MTS R0 2G2 PR01 EN P SYSTEM200 RECO PLC ISP200 R G2 ...
Page 6: ...IV Contents RECO PLC ISP200 R G2 DOK CONTRL MTS R0 2G2 PR01 EN P ...
Page 26: ...4 6 Technical Data RECO PLC ISP200 R G2 DOK CONTRL MTS R0 2G2 PR01 EN P ...
Page 30: ...5 4 Communication RECO PLC ISP200 R G2 DOK CONTRL MTS R0 2G2 PR01 EN P ...
Page 42: ...6 12 Startup RECO PLC ISP200 R G2 DOK CONTRL MTS R0 2G2 PR01 EN P ...
Page 46: ...7 4 RECO PLC MTS R01 2 RECO PLC ISP200 R G2 DOK CONTRL MTS R0 2G2 PR01 EN P ...
Page 50: ...8 4 RECO PLC MTS R02 2 RECO PLC ISP200 R G2 DOK CONTRL MTS R0 2G2 PR01 EN P ...
Page 54: ...9 4 INTERBUS Master Connection RECO PLC ISP200 R G2 DOK CONTRL MTS R0 2G2 PR01 EN P ...
Page 66: ...12 4 Serial Interfaces RECO PLC ISP200 R G2 DOK CONTRL MTS R0 2G2 PR01 EN P ...
Page 85: ......