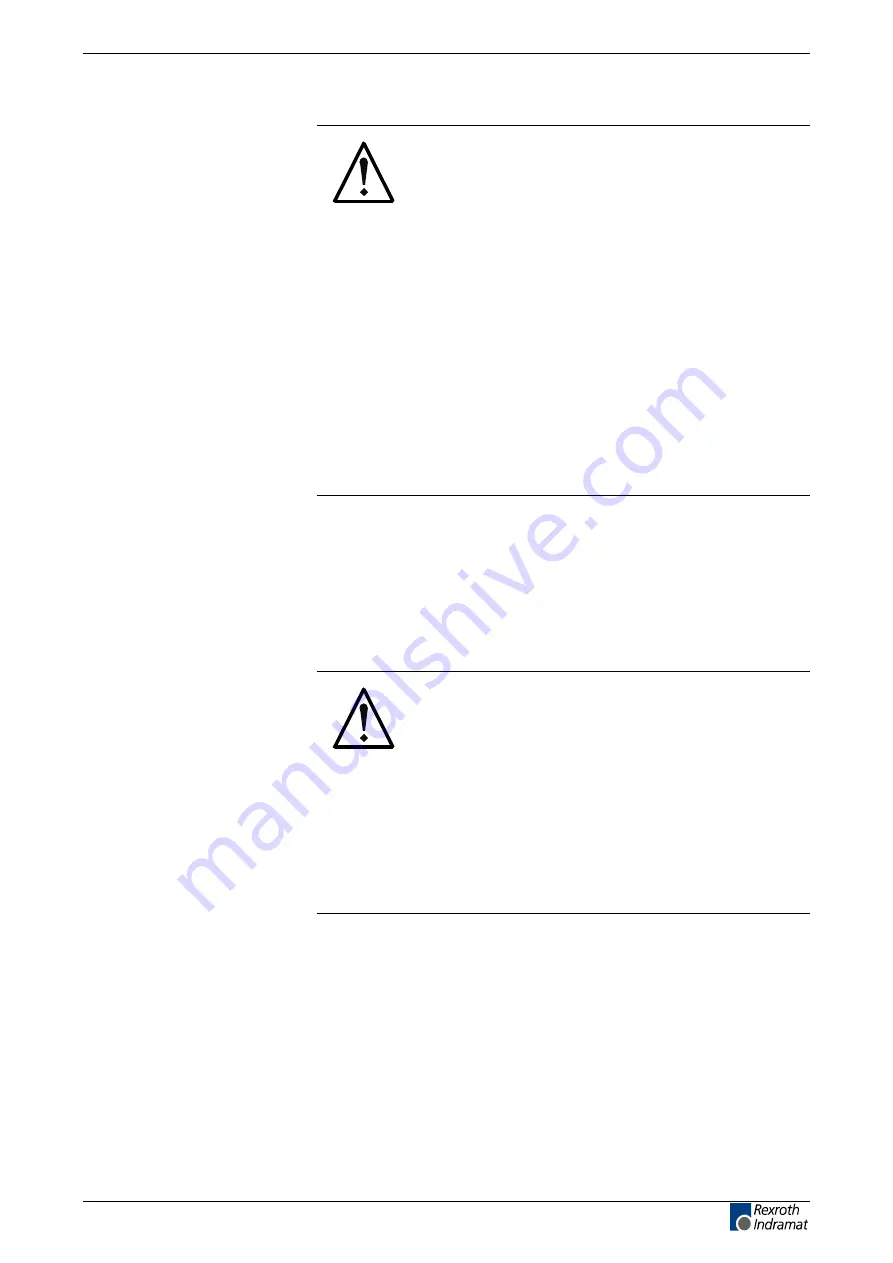
RECO PLC ISP200-R/G2
Safety Instructions for Electric Drives and Controls
3-5
DOK-CONTRL-MTS-R0*.2G2-PR01-EN-P
To be observed with electrical drive and filter components:
DANGER
High electrical voltage on the housing!
High leakage current! Danger to life, danger of
injury by electric shock!
⇒
Connect the electrical equipment, the housings of all
electrical units and motors permanently with the safety
conductor at the ground points before power is
switched on. Look at the connection diagram. This is
even necessary for brief tests.
⇒
Connect the safety conductor of the electrical
equipment always permanently and firmly to the
supply mains. Leakage current exceeds 3.5 mA in
normal operation.
⇒
Use a copper conductor with at least 10 mm² cross
section over its entire course for this safety conductor
connection!
⇒
Prior to startups, even for brief tests, always connect
the protective conductor or connect with ground wire.
Otherwise, high voltages can occur on the housing
that lead to electric shock.
3.6
Protection Against Electric Shock by Protective Low
Voltage (PELV)
All connections and terminals with voltages between 0 and 50 Volts on
Rexroth products are protective low voltages designed in accordance with
international standards on electrical safety.
WARNING
High electrical voltage due to wrong
connections! Danger to life, bodily harm by
electric shock!
⇒
Only connect equipment, electrical components and
cables of the protective low voltage type (PELV =
Protective Extra Low Voltage) to all terminals and
clamps with voltages of 0 to 50 Volts.
⇒
Only electrical circuits may be connected which are
safely isolated against high voltage circuits. Safe
isolation is achieved, for example, with an isolating
transformer, an opto-electronic coupler or when
battery-operated.
3.7
Protection Against Dangerous Movements
Dangerous movements can be caused by faulty control of the connected
motors. Some common examples are:
•
improper or wrong wiring of cable connections
•
incorrect operation of the equipment components
•
wrong input of parameters before operation
•
malfunction of sensors, encoders and monitoring devices
•
defective
components
•
software or firmware errors
Summary of Contents for DURADRIVE SYSTEM200
Page 1: ...Project Planning Manual DOK CONTRL MTS R0 2G2 PR01 EN P SYSTEM200 RECO PLC ISP200 R G2 ...
Page 6: ...IV Contents RECO PLC ISP200 R G2 DOK CONTRL MTS R0 2G2 PR01 EN P ...
Page 26: ...4 6 Technical Data RECO PLC ISP200 R G2 DOK CONTRL MTS R0 2G2 PR01 EN P ...
Page 30: ...5 4 Communication RECO PLC ISP200 R G2 DOK CONTRL MTS R0 2G2 PR01 EN P ...
Page 42: ...6 12 Startup RECO PLC ISP200 R G2 DOK CONTRL MTS R0 2G2 PR01 EN P ...
Page 46: ...7 4 RECO PLC MTS R01 2 RECO PLC ISP200 R G2 DOK CONTRL MTS R0 2G2 PR01 EN P ...
Page 50: ...8 4 RECO PLC MTS R02 2 RECO PLC ISP200 R G2 DOK CONTRL MTS R0 2G2 PR01 EN P ...
Page 54: ...9 4 INTERBUS Master Connection RECO PLC ISP200 R G2 DOK CONTRL MTS R0 2G2 PR01 EN P ...
Page 66: ...12 4 Serial Interfaces RECO PLC ISP200 R G2 DOK CONTRL MTS R0 2G2 PR01 EN P ...
Page 85: ......