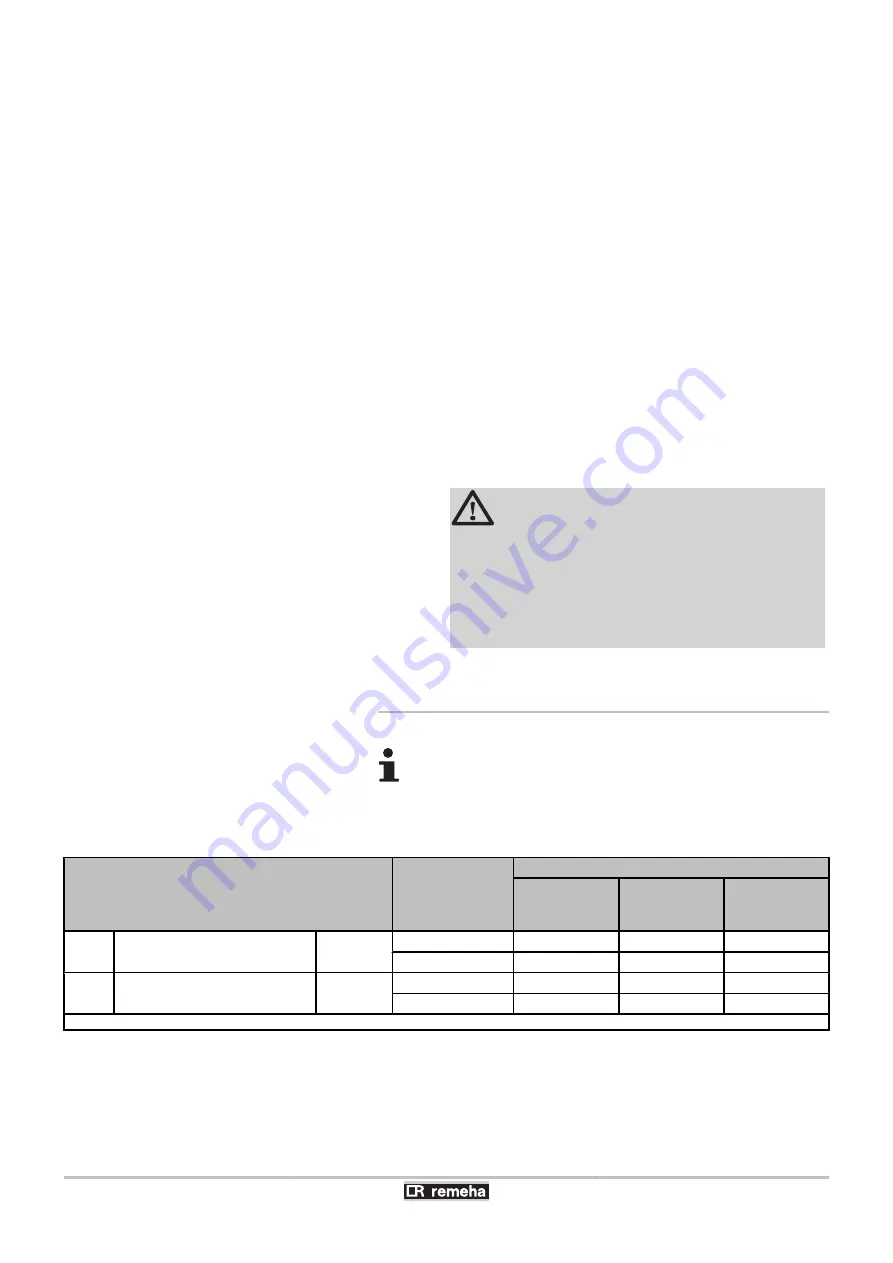
5
Configuration C
43(x)
Air/flue gas connection to a collective conduit for
watertight boilers (3CE P system)
6
Configuration C
53
Air and flue gas connection separated by means of a bi-
flow adapter and single pipes (combustive air taken from
outside)
7
Configuration C
83(x)
Flue gas connection to a collective conduit for sealed
boilers. The air supply is individual via a terminal coming
from outside the building.
8
Configuration C
93(x)
Air/flue gas connection by concentric pipes in the boiler
room and single pipes in the chimney (combustive air in
counter current in the chimney)
9
Configuration C
93(x)
Air/flue gas connection by concentric pipes in the boiler
room and single flex in the chimney (combustive air in
counter current in the chimney)
WARNING
4
Only factory components are authorised for
connecting the boiler and the terminal.
4
The clear section must comply with the
standard.
4
The chimney must be swept before the
installation of the evacuation conduit.
5.7.2.
Lengths of the air/flue gas pipes
For configurations B
23
and C
93
, the lengths given in the
table are valid for horizontal conduits with a maximum
length of 1 metre. For each additional metre of horizontal
conduit, subtract 1.2 m from the vertical length Lmax
Type of air/flue gas connection
Diameter
Maximum length in metres
CALORA
TOWER GAS
15S EX
CALORA
TOWER GAS
25S EX
CALORA
TOWER GAS
35S EX
C
13
Concentric pipes connected to a
horizontal terminal
Alu or PPS 60/100 mm
12,0
3,5
3,5
80/125 mm
12,3
20,0
17,6
C
33
Concentric pipes connected to a
vertical terminal
Alu or PPS 60/100 mm
13,0
4,9
5,5
80/125 mm
10,7
20,0
19,0
(1) See table for minimum sizes of duct or sleeving
CALORA TOWER GAS 15S EX CALORA TOWER GAS 25S EX
CALORA TOWER GAS 35S EX
5. Installation
22/04/2016 - 300026141-001-07
33