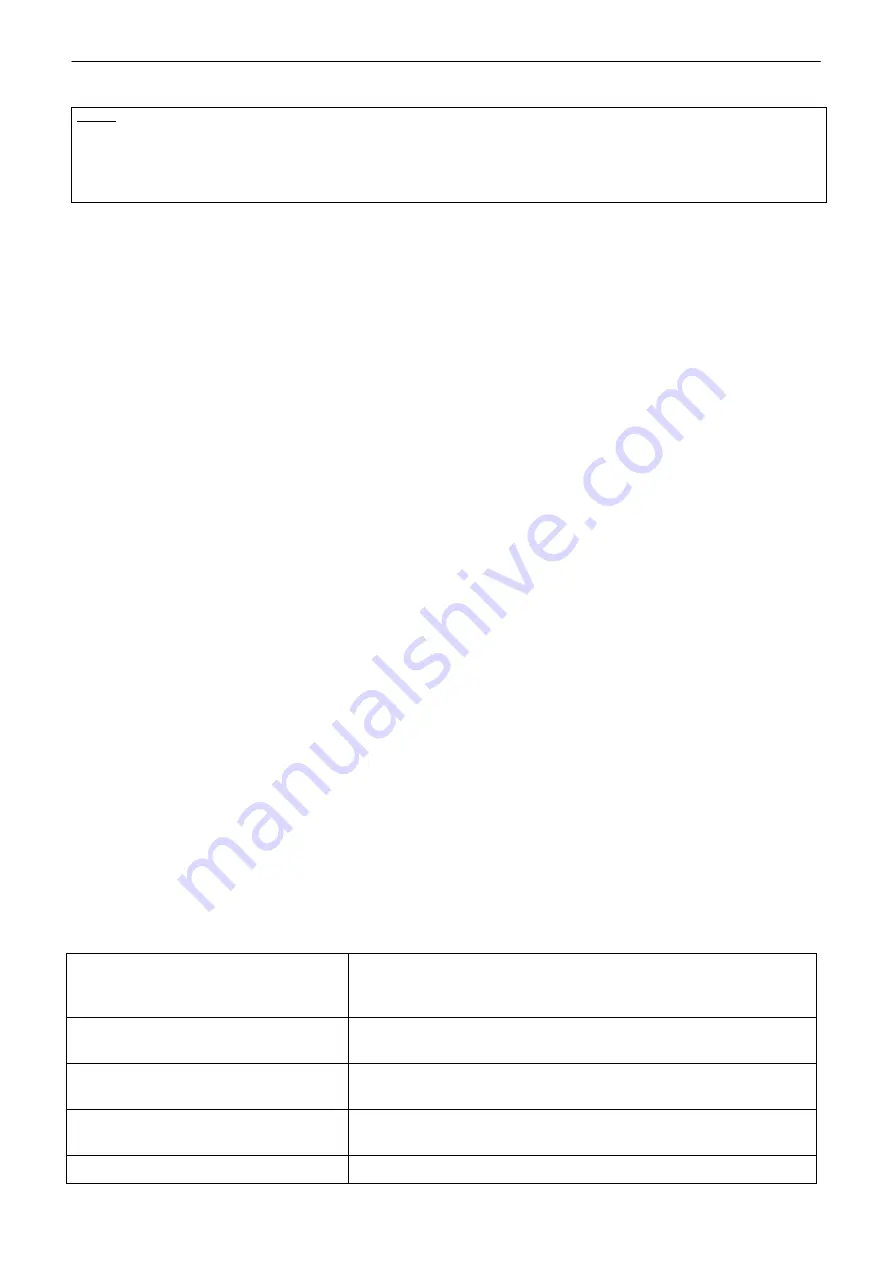
20
SP 0.1, SPR 0.1
Notes:
1. The controller at autocalibration automatically sets the feedback type - resistant/current
2. (*) Parameters set in the production plant, if customer has not stated else.
3. (**) Input signal
4 mA - position "closed"
20 mA - position "open"
Standard setting of controller (programmed RESET of controller) -
in case of any problems with
setting of the parameters it is possible with pressing both
SW1 and SW2
at the same time and then
switching power on to set the standard parameters.
Controller setting procedure:
The initialisation routine starts at the switched-on controller, zero system deviation and short pressing
of the SW1 button for ca 2 sec (i.e. until the diode D3 got on). Loosing the button some of the default
menus starts (usually control signal) what is shown with 1 blink on the D3 diode as well as one of the
default parameters (usually control signal of 4-20mA) what is shown with 1 blink on the D4 diode.
Then the required parameters of the controller can be changed according to Table 2:
•
press shortly the SW1 button to list the menu shown with the blinking number on the D4 diode.
•
press shortly the SW2 button to set parameters shown with the blinking number on the D4 diode.
After changing of the parameters according to user's wishes, put the controller to autocalibration
with pressing the SW1 button for ca 2 sec (i.e. until the diode D3 got on). During this process the
controller performs the feedback transmitter and turning sense checking, sets actuator to the positions
"open" and "closed", measures inertia mass in the directions "opening" and "closing", and loads the
adjusted parameters into the EEPROM memory. In case that during the initialisation process an error
occurs (e.g. in connection or adjustment) the initialisation process will be interrupted and the controller
with the D4 diode reports about the type of the error. Else after finishing the initialisation process the
controller is put into the regulation mode.
Error messages of the controller with D4 diode at initialisation
4 blinks .......... improper connection of the torque switches
5 blinks .......... improper connection of the feedback transmitter
8 blinks
bad sense of actuator's turning direction or adverse connection of the feedback
transmitter
3.7.2
Watching operation and error states
Watching operation and error states is possible with the EA open.
a) Operation status with the D3 LED diode indicating:
•
it is continuously lighting - the controller regulates
•
it is continuously not lighting - system deviation in the insensitiveness range - the EA has stopped
b) Error state with the D4 and D3 LED diodes indicating - D4 continuously lighting,
D3 indicates error state with blinking
1 blink
(repeated)
indication of the "TEST" mode - the EA is put to the position
according to the signal in the "TEST" menu (at connecting the 66
and 86/87 terminals)
2 blinks
(repeating after short pause)
missing of control signal - the EA is put to the position according
to the signal in the "TEST" menu
4 blinks
(repeating after short pause)
torque switches activity indication (the EA switched-off with the
torque switches in a mid-position)
5 blinks
(repeating after short pause)
failure of the feedback transmitter - the EA is put to the position
according to the signal in the "TEST" menu
7 blinks
(repeating after short pause)
control signal (current at range 4-20mA less than 4mA (3.5mA)).
Summary of Contents for SP 0.1
Page 26: ...24 SP 0 1 SPR 0 1 6 Enclosures 6 1 Wiring diagrams Wiring diagrams for EA SP 0 1...
Page 29: ...SP 0 1 SPR 0 1 27 6 2 Dimensional drawings...
Page 30: ...28 SP 0 1 SPR 0 1...
Page 31: ...SP 0 1 SPR 0 1 29...
Page 32: ...30 SP 0 1 SPR 0 1...
Page 33: ...SP 0 1 SPR 0 1 31...
Page 34: ...32 SP 0 1 SPR 0 1...
Page 35: ...SP 0 1 SPR 0 1 33...