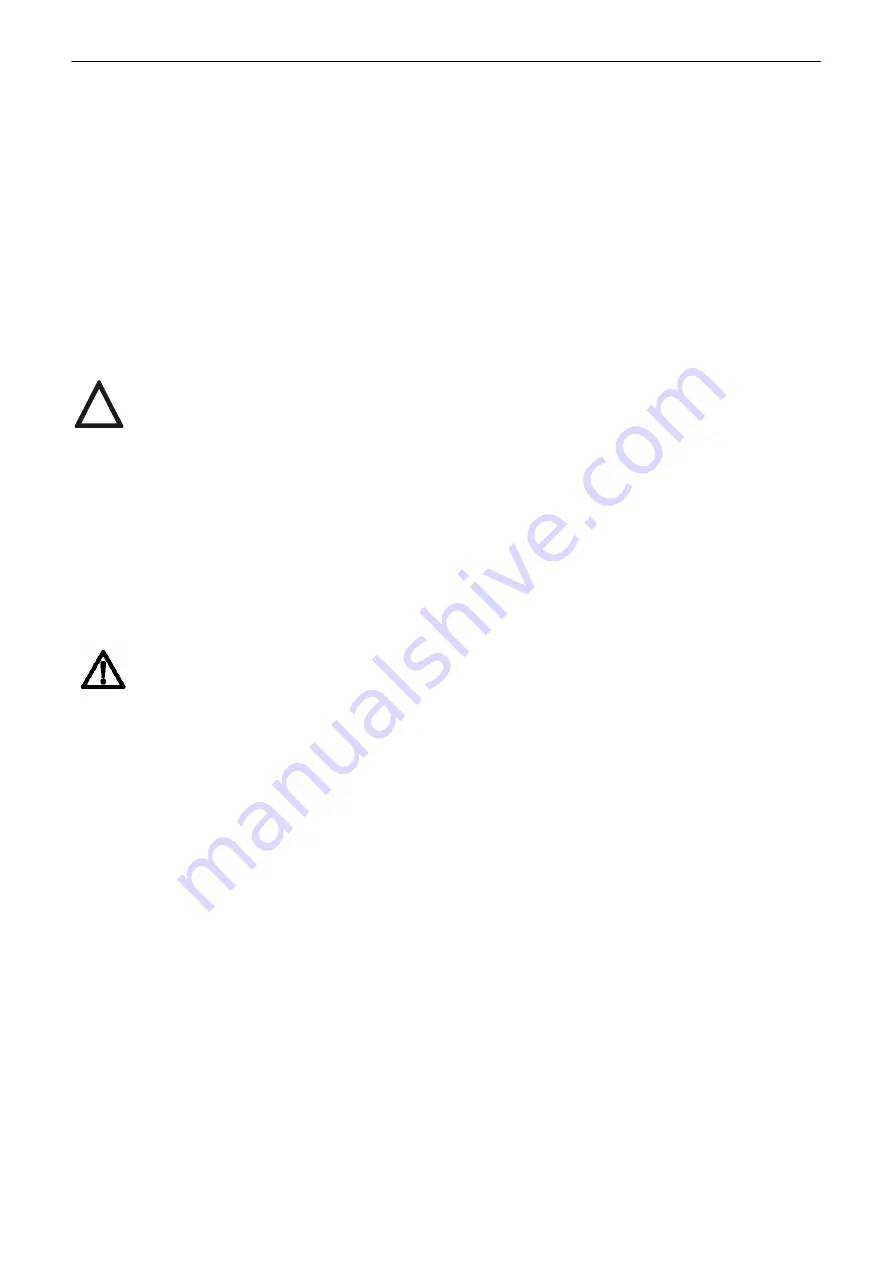
14
SP 0.1, SPR 0.1
The procedure is as follows
Press the button
SW1
for about 2 sec (i.e. till the
D3
diode is got on) to set the controller to the
autocalibration
mode. During this process the controller checks the feedback transmitter and the
sense of turning, puts the EA to the positions open and closed, measures inertia mass in the directions
"opening" and "closing", and loads the adjusted parameters into the EEPROM memory. In case that
during the initialisation process an error occurs (e.g. in connection or adjustment) the initialisation
process will be interrupted and the controller with the
D4
diode reports about the type of the error. Else
after finishing the initialisation process the controller is put into the
regulation mode
. If needed to
change adjusted parameters of the controller follow instructions given in the part Adjusting of actuator.
2.2 Dismantling
Before dismantling it is required to disconnect the EA from mains!
Do not connect and disconnect live connectors!
•
Disconnect the EA from mains.
•
Disconnect the leads from the EA terminal boards and loosen the cables from cable glands.
•
Loosen the fixing screws of the EA flange and disconnect the EA from the valve.
•
While sending the EA to be repaired put it into a package solid enough to avoid damages of the EA
during transportation.
3. Adjusting of actuator
Attention!
See chapter 1.2.2 Requirements for professional qualification …
Disconnect the electrical servo-drive from electrical power network!
Observe safety regulations!
The adjustment can be performed at a mechanically and electrically connected EA. This part
describes adjustment of EA to specified parameters in case that any unit of EA is reset. Laying of
adjusters of the control board is shown on Fig.1.
The control parts designed for adjustment are accessible after removing of the actuator upper
cover. Unscrew the four screws fixing the cover to the bottom case, and remove the cover.
After adjustment fix again the cover with the four screws. While placing the cover onto the
actuator have the position unit shaft fitting in the pointer shaft recess. Having the cover on and the
screws tightened adjust the pointer in accordance with the Chapter 4.6.
3.1 Output position changes
In the plant the end positions of the actuators are adjusted in accordance with the dimensional
drawings. If while the mechanical disengagement in accordance with the Chapter 2.1 the adjustment
does not meet the requirements, it is needed to turn the fixed operation angle 60°, 90°, 120° or 360°
by any value (in the limit position "closed"). While output position changing it is needed to adjust the
actuator in accordance with the Chapters 3.2 to 3.7.
If during the adjustment the actuator stops after switching-off the end switch S4 before the
required position, it is needed to turn the cam V4 counter-clockwisely until the required limit position
"closed" is set (Chapter 3.2).
!
Summary of Contents for SP 0.1
Page 26: ...24 SP 0 1 SPR 0 1 6 Enclosures 6 1 Wiring diagrams Wiring diagrams for EA SP 0 1...
Page 29: ...SP 0 1 SPR 0 1 27 6 2 Dimensional drawings...
Page 30: ...28 SP 0 1 SPR 0 1...
Page 31: ...SP 0 1 SPR 0 1 29...
Page 32: ...30 SP 0 1 SPR 0 1...
Page 33: ...SP 0 1 SPR 0 1 31...
Page 34: ...32 SP 0 1 SPR 0 1...
Page 35: ...SP 0 1 SPR 0 1 33...