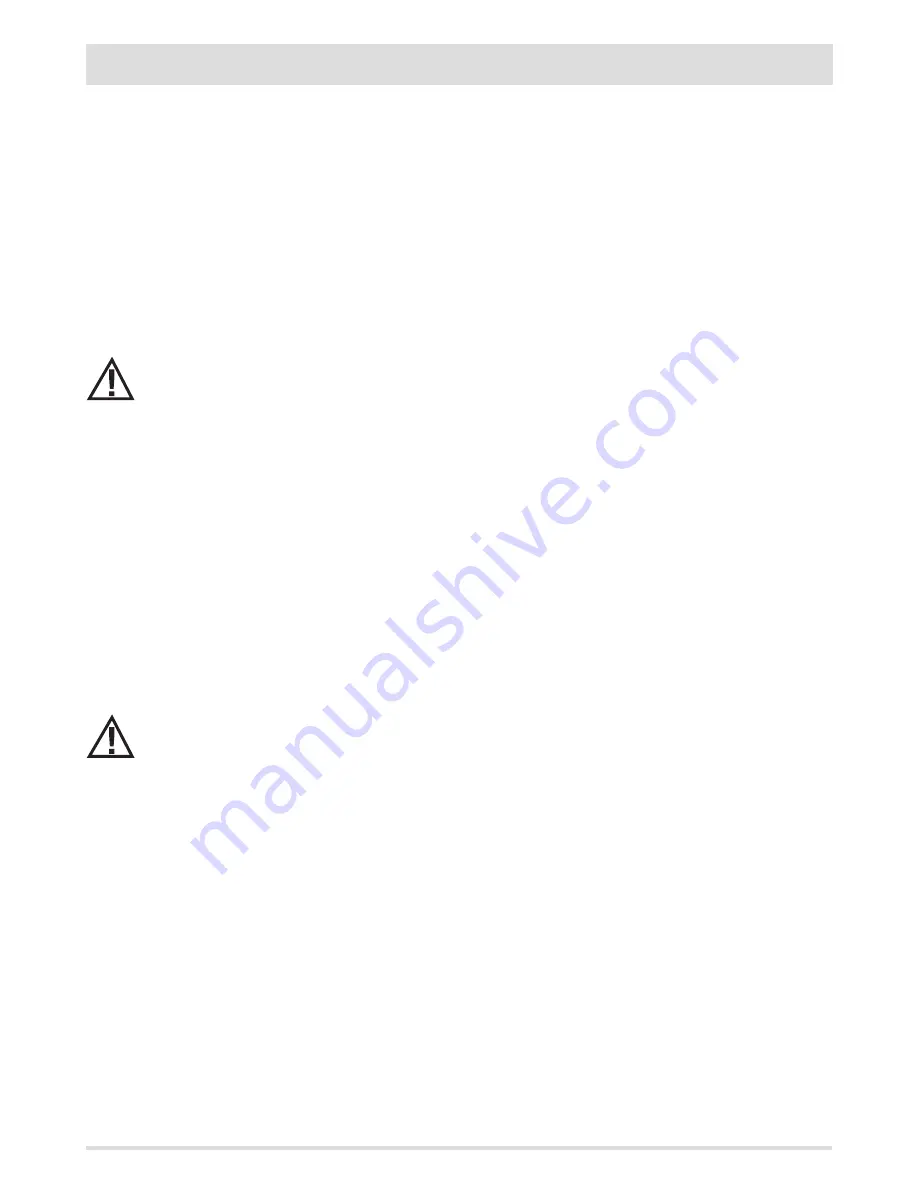
5-PLUMBING CONNECTION
29
Technical Dept. - All rights reserved - Reproduction is prohibited
SYSTEM WASHING
Fit suitable gate valves on the heating system pipes.
To protect the heating system from harmful corrosion, fouling or deposits, it is of the utmost importance, before installing the product, to
wash the system in compliance with UNI-CTI 8065, using appropriate products such as, for example, Sentinel X300 (new systems), X400
and X800 (old systems) or Fernox Cleaner F3.
Complete instructions are provided with the products but, for further clarifications, please directly contact the manufacturer SENTINEL
PERFORMANCE SOLUTIONS LTD or Fernox COOKSON ELECTRONICS. After flushing the system, to protect it against corrosion and deposits,
we recommend the use of inhibitors such as Sentinel X100 or Fernox Protector F1.
It is important to check the concentration of the inhibitor after each change to the system and during maintenance as prescribed by
manufacturers (specific tests are available at dealers).
The discharge of the safety valve must be connected to a collecting funnel for conveying the possible dredges in case of intervention.
Attention: Failure to clean the heating system and to add a suitable inhibitor will void the warranty of the equipment
and other accessories such as for example pumps and valves.
SYSTEM FILLING
Filling must be carried out slowly so that air bubbles can get out via the purposely placed outlets on the heating system. In closed circuit
heating systems the loading pressure of the system when cold and the expansion tank preloading pressure must be tha same.
• In
open
tank heating systems, there is direct contact between the circulating liquid and air. During the heating season the end user
must regularly check the level of water circulating in the expansion tank. The content of water in the recycling system must be kept
constant. Practical experience demonstrates that the water level must be inspected regularly every 14 days to maintain the water
content almost constant. In the event one needs to add water one must carry out the filling process when the boiler has cooled down
to room temperature. These precautions aim to prevent the onset of a thermal stress of the steel body of the boiler.
• In systems equipped with an open tank the water pressure in the boiler - when the system is cold - must not fall below 0.3 bar;
• The water used for filling the heating system must be decontaminated and without air.
Attention!
Do not mix the heating water with antifreeze or anticorrosion substances in the wrong concentrations! It can
damage the seals and cause the onset of noise during operation.
The manufacturer declines all responsibility if the damage caused to persons, animals or things is a result of failure
to comply with the above.
Once all plumbing connections have been carried out, proceed with the inspection of the seals under pressure, by filling
the boiler.
This operation must be done carefully observing the following steps:
• open the radiator, boiler and system air valves;
• gradually open the system filling tap making sure that any automatic air valves installed on the system work properly;
• close the radiator air valves as soon as water starts to come out;
• on the system pressure gauge check that the pressure reaches a value of approximately 1 bar (applicable only for systems equipped
with a closed tank - refer to any standards or local regulations that allow it); for open tank systems refilling takes place automatically
via the same tank;
• close the system loading tap and then bleed air again via the radiator air valves;
• check tightness of all connections;
• after having started the boiler for the first time and heated up the system, stop the pumps and repeat the air bleeding operations;