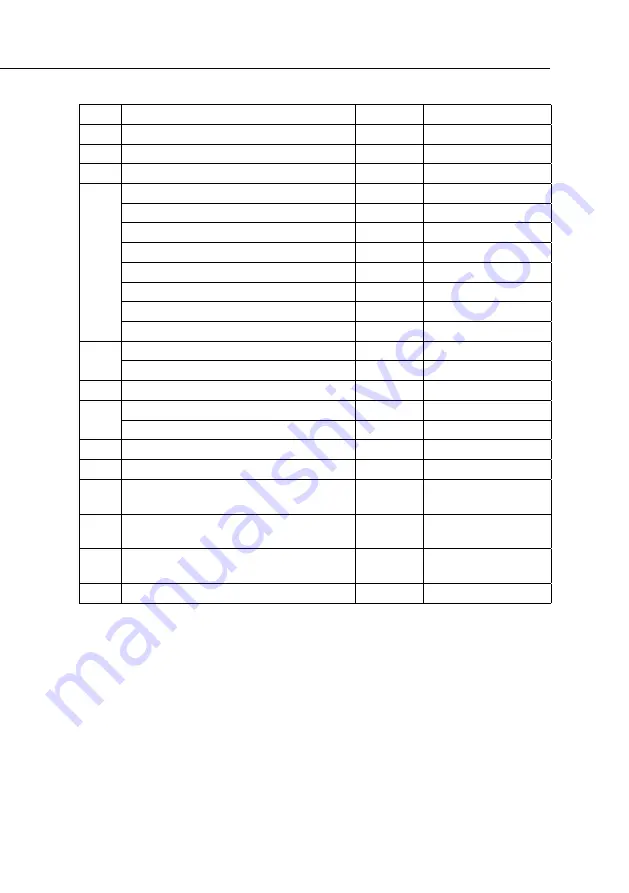
41
Operating instructions
Peristaltic Pump ISI Series
POS.
DESCRIPTION
QUANTITy
REFERENCE
1
Pump Housing
1
AX102.01.01
2
Roller Kit ISI 10 / 13
2
AX102.99.01
3
Press flange standard
2
AX102.00.11
4
Connection S.S. BSP 3/8” ISI 13
2
AX103.00.10
Connection P.P. BSP 3/8” ISI 13
2
AX103.00.15
Connection PVDF BSP 3/8” ISI 13
2
AX103.00.16
Connection S.S. NPT 3/8” ISI 13
2
AX103.00.17
Connection PVC NPT 3/8” ISI 13
2
AX103.00.37
Connection PVDF NPT 3/8” ISI 13
2
AX103.00.19
Connection S.S. TRI-CLAMP 3/4" ISI 13
2
AX103.00.22
Connection S.S. DIN 11851 NW-15 ISI 13
2
AX103.00.20
5
Peristaltic Hose NORPRENE ISI 13
1
AX103.00.31
Peristaltic Hose SILICONE ISI 13
1
AX103.00.38
6
Plastic cover
1
AX102.02.08
7
Base plate
1
AX102.00.12
Base plate S.S.
1
AX102.00.24
8
Drive
1
9
Cover Gasket
1
AX102.01.05
10
DIN 931 Hexagonal Head Partially-threaded
Cap Screw M6x30
4
AXTORDIN931M6X30
11
DIN 931 Hexagonal Head Partially-threaded
Cap Screw M6x40
4
AXTORDIN931M6X40
12
DIN 933 Hexagonal Head Cap Screw M5x10
Grade 8.8
4
AXTORDIN933M5X10
13
DIN 125A Flat Washer M6 Grade 8.8
8
AXARANDIN125AM6
Summary of Contents for ISI 10
Page 1: ...Operating instructions ISI Series Peristaltic pump ALL THE HOSE PUMP YOU LL EVER NEED ...
Page 38: ...38 Operating instructions Peristaltic Pump ISI Series 11 3 Spare parts exploded ISI 13 Model ...
Page 42: ...42 Operating instructions Peristaltic Pump ISI Series 11 5 Spare parts exploded ISI 16 Model ...
Page 48: ...48 Operating instructions Peristaltic Pump ISI Series 11 8 Spare parts exploded ISI 22 Model ...
Page 53: ...53 13 Declaration of Conformity ...
Page 59: ......
Page 60: ...AHQ IOM EN 0849 1120 www realaxpumps com ALL THE HOSE PUMP YOU LL EVER NEED ...