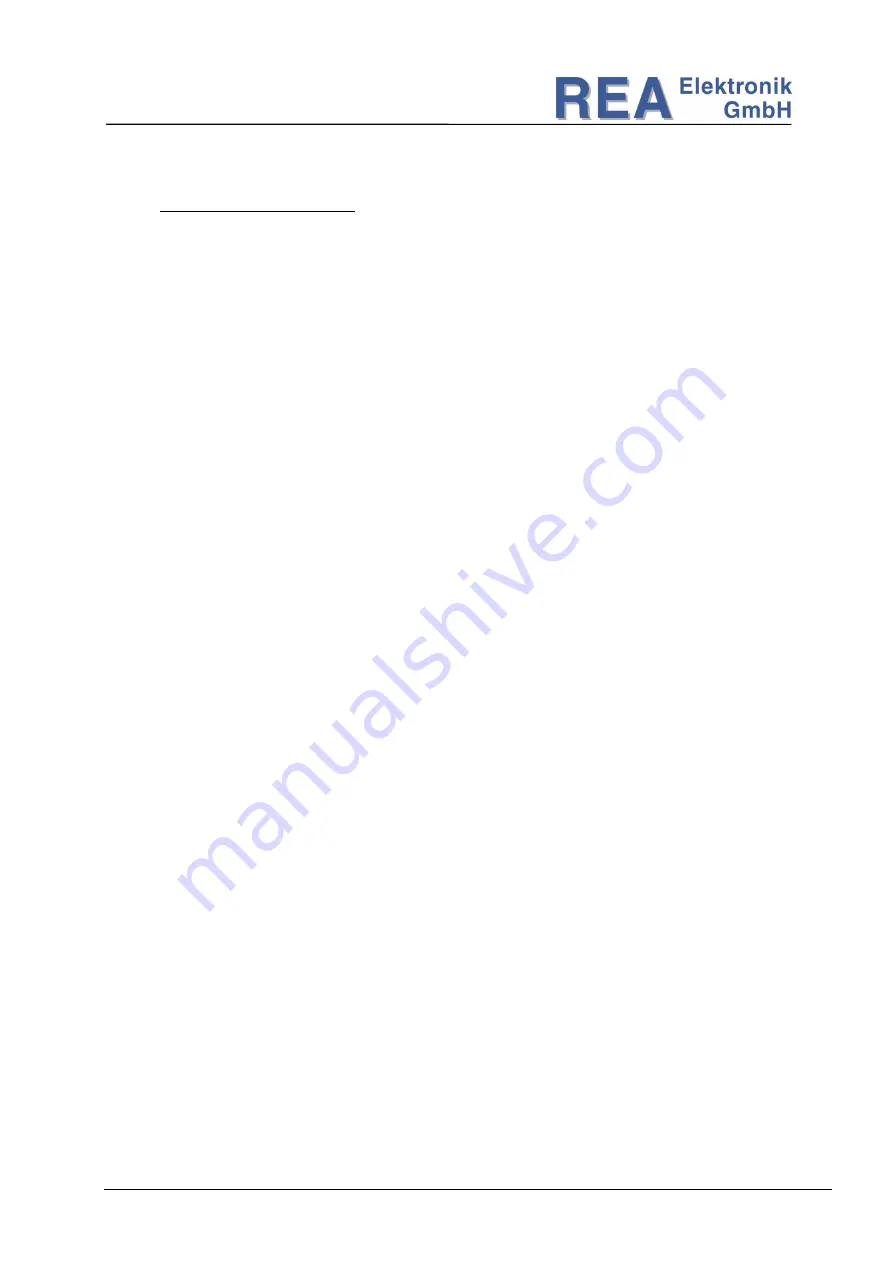
Copyright © 2006 REA Elektronik
Seite 6
Rationalisierung
Entwicklung
Automation
Elektronische Geräte und Systeme
6
Operator requirements
To install the REA-JET coding and marking system technical knowledge how to set up electrical
equipment is required.
For operation and maintenance of the coding and marking system a certified training is mandatory.
This training will allow the user to properly work with all system components and will also train for
proper handling of consumables such as inks and cleaner.