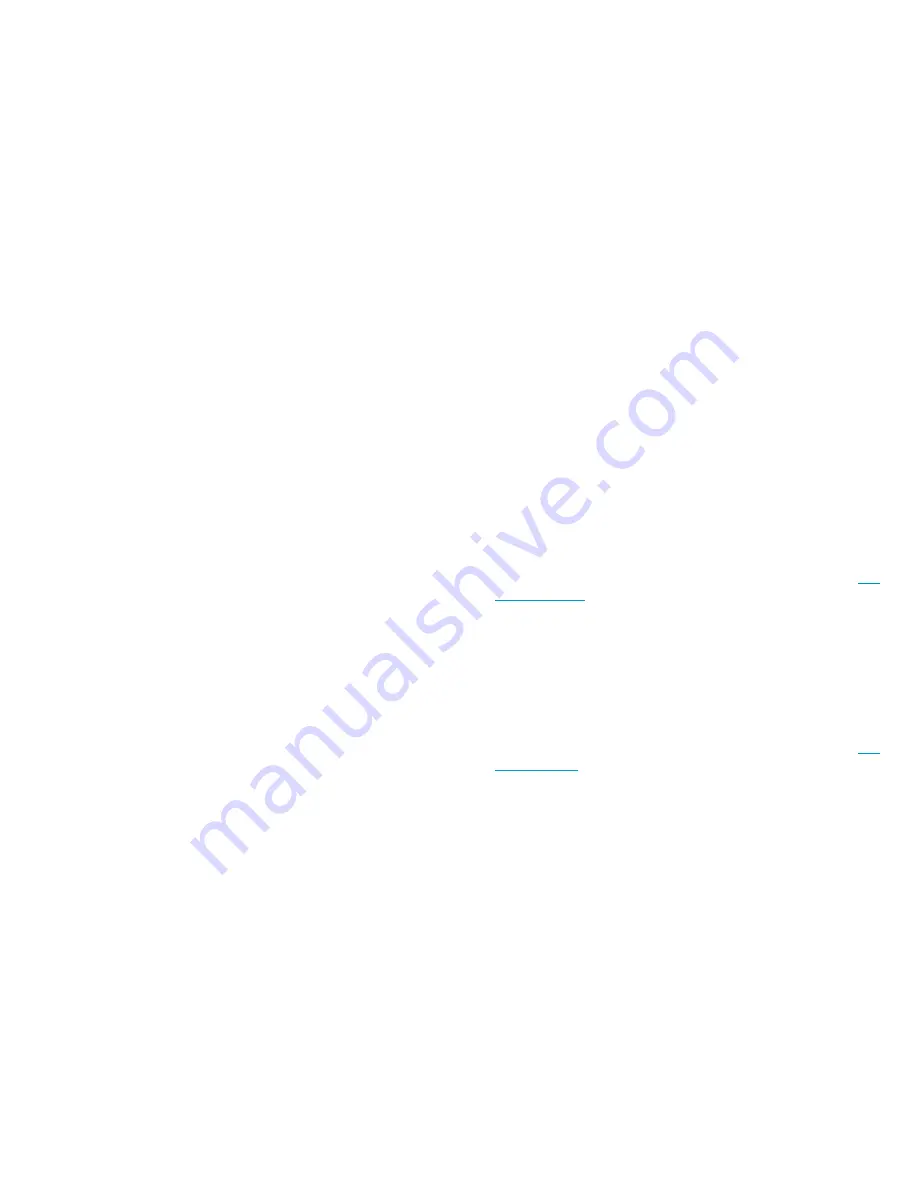
22
| Terms
23. TERMS
23.1 Throttle
Throttle can be compared to a vehicle’s gas pedal. More throttle increases propeller speed
and altitude and less throttle reduces propeller speed and altitude.
23.2 Elevator
Elevator denotes the movement around the lateral axis which can be compared to the
nodding of a head. Through this, the »NovaX 350 gains flight speed forwards or backwards
or decelerates.
23.3 Rudder
Rudder denotes the rotation of the »NovaX 350 around the rudder axis (vertical axis).
This movement either occurs unintentionally due to the speed torque of the propellers or
intentionally as a flight direction change. For the »NovaX 350, this movement is controlled
through speed variation of the individual propellers.
23.4 Aileron
Aileron denotes the movement around the longitudinal axis which can be compared to the
sideways rolling of a ball (or the sideways crawl of a crab). In this way, through lifting one
side the »NovaX 350 moves to the side independently of its forward direction.
23.5 Hover
Hover denotes a flight status in which the »NovaX 350 neither rises nor falls so that the
upwards directed uplift force is equal to the downwards directed weight.
23.6 Mode 1, Mode 2
Mode 1 and Mode 2 refer to the stick arrangement of the transmitter.
23.7 GNSS
>
GNSS
stands for Global Navigation Satellite System and enables you to precisely fix
a position.
>
R.T.H. (Return To Home), the GPS mode and T.P.C.S. (Task Point Command System)
make use of GNSS.
23.8 I.R.P.C
>
I.R.P.C stands for Intelligent Relative Positioning Control. It utilizes compass and
positioning data to control the »NovaX 350 relatively to the take-off position.
>
Activate and configure I.R.P.C. in the
EYE CONTROL
app. Also see chapter
‘30.6
I.R.P.C.’ on page
38
.
23.9 S.M.A.R.T
>
S.M.A.R.T or Software Managed Auto Return Technology enables the pilot to quickly
and safely recover the »NovaX 350 in the event of loss of control over the »NovaX 350.
>
Configure S.M.A.R.T. in the
EYE CONTROL
app. The
AUTO
function marks the motor
start location as home and the pilot can deactivate the function again to take back
control as soon as they see the situation under control.
>
To learn more about S.M.A.R.T., refer to the product website and also see chapter
‘30.5
R.T.H.’ on page
37
.
Summary of Contents for NovaX 350
Page 1: ...88012RC ArF 88014RC RtF NovaX 350 Operating instructions M1...
Page 2: ...2 EVER WONDERED WHAT INNOVATION LOOKS LIKE NovaX 350...
Page 21: ...Dimensions 21 22 2 Long legs 283 mm 283 mm 250 mm 241 mm 130 mm 2 0 3 m m 3 4 7 m m...
Page 27: ...Calibration 27 2 1 90 90 90 1 2 3 4 5 6 Fig 6...
Page 49: ...49...
Page 50: ...50...
Page 51: ...51...
Page 52: ...52 www rclogger com...