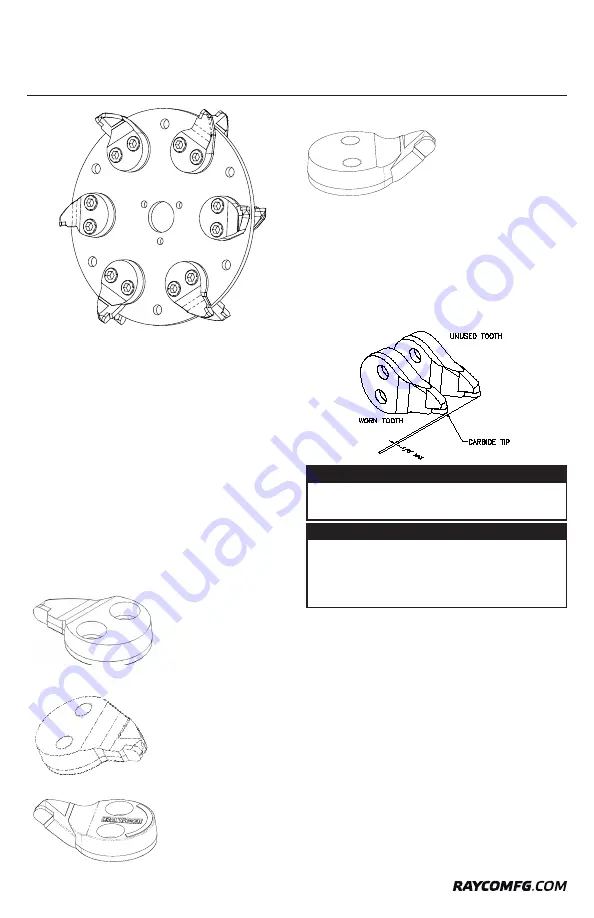
RG25DH Operation • Service • Maintenance • Parts Manual
34
• Position teeth as shown in the drawing above. Straight
teeth and bent teeth should be alternated as shown in
the drawing.
• When using Rayco brand square-shanked teeth, set
extreme edge of each tooth 1¼” away from edge of
pocket.
• When using Rayco SUPERTEETH®, because of one
piece construction, no pre-setting of the tooth is required.
• Make sure teeth are placed in coordinance with wheel
rotation.
• After setting each tooth pair, tighten the socket head
bolts to 135 to 145 foot-pounds.
There are four types of Superteeth, as shown in the diagram
on the previous page. The counterbored teeth are on one
side of the cutting wheel, the tapped teeth on the opposite
side. The tips of the bent teeth will always point away from
the cutting wheel.
1.) Straight Tooth - Part# 3144C (countersunk) Qty of 3.
2.) Straight Threaded Tooth - Part# 3144T Qty of 3
3.) Angled Countersunk Tooth - Part# 2933C Qty of 9.
4.) Angled ThreadedTooth - Part# 2933T Qty of 9
5.) Cutter Wheel - Part#28515 Qty of 1
Sharpening of Teeth
Do not allow any tooth to wear too much before sharpening.
Discard any tooth that has lost more than 1/8” of original bite.
The teeth must be removed from the cutting wheel for proper
sharpening.
Tooth Sharpening Guidelines
1. Obtain an unused tooth for comparison.
2. Discard any tooth that has lost more than 1/8” of original
bite, whether lost through usage or grinding.
3. Grind off a minimal amount from the end, just enough
to restore the original taper and radius on the end. The
end of the cemented carbide tip and the end of the steel
shank should be flush after grinding.
Maintenance
NOTICE
Do not hammer the tip of a tooth. Due to the super
hardness fo the tooth, it is brittle and may chip.
Sharpening cemented carbide cutting teeth
requires a special process. Have your teeth
sharpened only by a qualified machinist for
obtaining a proper edge and to avoid injury.
NOTICE
Summary of Contents for RG25HD
Page 48: ...RG25DH Operation Service Maintenance Parts Manual 48 Troubleshooting ...
Page 49: ...RG25DH Operation Service Maintenance Parts Manual 800 392 2686 49 Troubleshooting ...
Page 50: ...RG25DH Operation Service Maintenance Parts Manual 50 Troubleshooting ...
Page 51: ...RG25DH Operation Service Maintenance Parts Manual 800 392 2686 51 Troubleshooting ...
Page 52: ...RG25DH Operation Service Maintenance Parts Manual 52 Troubleshooting ...
Page 53: ...RG25DH Operation Service Maintenance Parts Manual 800 392 2686 53 Troubleshooting ...
Page 54: ...RG25DH Operation Service Maintenance Parts Manual 54 Troubleshooting ...
Page 55: ...RG25DH Operation Service Maintenance Parts Manual 800 392 2686 55 Troubleshooting ...
Page 56: ...RG25DH Operation Service Maintenance Parts Manual 56 Troubleshooting ...
Page 57: ...RG25DH Operation Service Maintenance Parts Manual 800 392 2686 57 Troubleshooting ...
Page 66: ...RG25DH Operation Service Maintenance Parts Manual 66 Hydraulic Drive Assembly ...