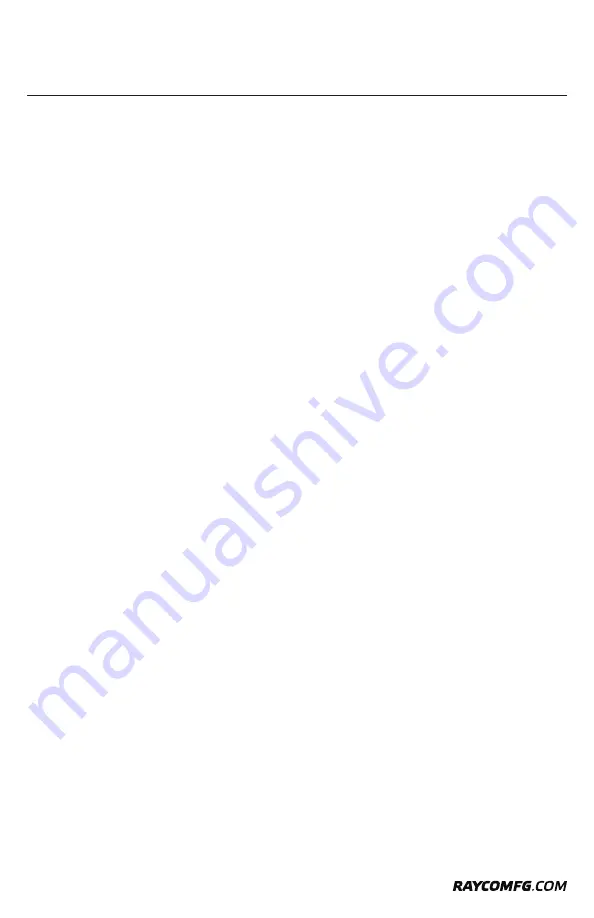
RG25DH Operation • Service • Maintenance • Parts Manual
16
Safety
6. Disconnect the operator restraint devices (if equipped)
and exit the machine.
7. Block the wheels (if equipped), and set manual brake
(if equipped) to prevent movement.
Slope Operation
Machines that are operating safely in various applications
depend on these criteria: the machine model, configuration,
machine maintenance, operating speed of the machine,
conditions of the terrain, fluid levels, and tire inflation
pressures. The most important criteria are the skill and
judgment of the operation.
A well trained operator that follows the instructions in the
Operation and Maintenance Manual has the greatest impact
on stability. Operator training provides a person with the
following abilities: observation of working and environmental
conditions, feel for the machine, identification
of potential hazards, and operating the machine safely by
making appropriate decisions.
When you work on side hills and when you work on slopes,
consider the following important points:
• Speed of travel – At higher speeds, forces of inertia
tend to make the machine less stable.
• Roughness of terrain or surface – The machine may be
less stable with uneven terrain.
• Direction of travel – Avoid operation the machine across
the slope. When possible, operate the machine up
the slopes and operate the machine down the slopes.
• Place the heaviest end of the machine uphill when you
are working on an incline.
• Mounted equipment – Balance of the machine may be
impeded by the following components: equipment that
is mounted on the machine, machine configuration,
weights, and counterweights.
• Nature of surface – Ground that has been newly filled
with earth may collapse from the weight of the machine.
• Surface material – Rocks and moisture of the surface
material may drastically affect the machine’s traction and
machine’s stability. Rocky surfaces may promote side
slipping of the machine.
• Slippage due to excessive loads – This may cause
downhill tracks or downhill tires to dig into the ground,
which will increase the angle of the machine.
• Width of tracks or tires – Narrower tracks or narrower
tires further increase the digging into the ground which
causes the machine to be less stable.
• Implements attached to the machine hitch if equipped
or drawbar – This may decrease the weight on the uphill
tracks. This may also decrease the weight on the uphill
tires. The decreased weight will cause the machine to
be less stable.
• Height of machine working load. When the working loads
are in higher positions, machine stability is reduced.
• Operated equipment – Be aware of performance
features of the equipment in operation and the effects
on machine stability.
Sound Level Information
The operator Equivalent Sound Pressure Level is used to
measure a work cycle sound exposure level
Hearing protection may be needed when the machine is
operated with an open operator station for extended periods
in a noisy environment. Hearing protection may be needed
when the machine is in operation.
Vibration Data Information concerning
hand/arm vibration level
When the machine is operated according to the intended
use, the hand/arm vibration of this machine is rated by meter
per second squared.
Note: Vibration levels are influenced by many different
parameters listed below.
• Operator training, behavior, mode, and stress
• Job site organization, preparation, environment, weather
and material
• Machine type, attachments, and condition of the
equipment.
Guidelines for Reducing Vibration Levels
on Equipment
Properly adjust machines. Properly maintain machines.
Operate machines smoothly. Maintain the conditions of the
terrain. The following guidelines can help reduce the whole
body vibration level:
1. Use the right type and size of machine, equipment, and
attachments for the job.
2. Maintain machines according to the manufacturer’s
recommendations.
a. Tire pressures
b. Brake and steering systems
c. Controls, hydraulic system and linkages
3. Keep the terrain in good condition.
a. Remove any large rocks or obstacles.
b. Fill any ditches and holes.
c. Provide machines and schedule time in order to
maintain the conditions of the terrain.
4. Use a seat that meets “ISO 7096”. Keep the seat
maintained and adjusted if equipped.
a. Adjust the seat and suspension for the weight and
the size of the operator.
b. Inspect and maintain the seat suspension and
adjustment mechanisms.
Summary of Contents for RG25HD
Page 48: ...RG25DH Operation Service Maintenance Parts Manual 48 Troubleshooting ...
Page 49: ...RG25DH Operation Service Maintenance Parts Manual 800 392 2686 49 Troubleshooting ...
Page 50: ...RG25DH Operation Service Maintenance Parts Manual 50 Troubleshooting ...
Page 51: ...RG25DH Operation Service Maintenance Parts Manual 800 392 2686 51 Troubleshooting ...
Page 52: ...RG25DH Operation Service Maintenance Parts Manual 52 Troubleshooting ...
Page 53: ...RG25DH Operation Service Maintenance Parts Manual 800 392 2686 53 Troubleshooting ...
Page 54: ...RG25DH Operation Service Maintenance Parts Manual 54 Troubleshooting ...
Page 55: ...RG25DH Operation Service Maintenance Parts Manual 800 392 2686 55 Troubleshooting ...
Page 56: ...RG25DH Operation Service Maintenance Parts Manual 56 Troubleshooting ...
Page 57: ...RG25DH Operation Service Maintenance Parts Manual 800 392 2686 57 Troubleshooting ...
Page 66: ...RG25DH Operation Service Maintenance Parts Manual 66 Hydraulic Drive Assembly ...