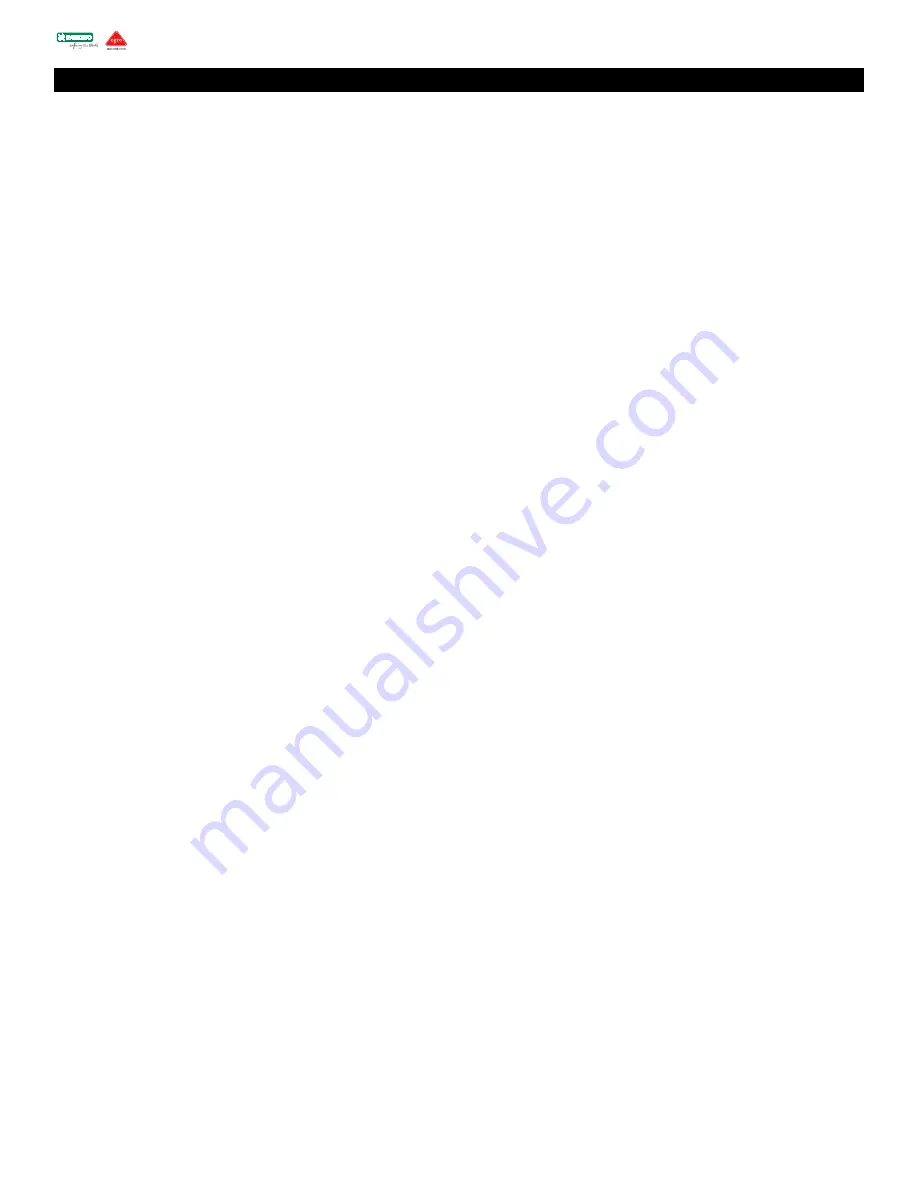
EGRO 5511
Manual
BREW GROUP REPLACEMENT
Complete Brew Group Assembly Replacement
1. Unplug
machine
2.
Remove the Left side panel to gain access to the mother board.
3.
Disconnect the Motors from the motherboard
a.
Connections “J2” & “J3” located in the up right hand side of the motherboard.
4.
Disconnect the John Guest fittings on the upper and lower piston
5.
Loosen the 2 nuts located behind the B.G.A.
6.
Pull the B.G.A. upwards to remove from the door.
7.
Clean any coffee build up on the B.G.A.
8.
Install the new B.G.A.
a.
Reverse Directions stated above.
*CAUTION*
Ensure that both John Guest fittings are fully seated and sealed. Failure to do so may result in water
damaging electrical components!
Page 61
Summary of Contents for EGRO 5511
Page 1: ...EGRO 5511 Technical Manual Technical Manual ...
Page 2: ......
Page 4: ...Page 4 ...
Page 5: ...EGRO 5511 Manual SECTION 1 INTRODUCTION OVERVIEW Page 5 ...
Page 8: ...Page 8 ...
Page 9: ...EGRO 5511 Manual SECTION 2 INSTALLATION Page 9 ...
Page 15: ...Page 15 ...
Page 16: ...EGRO 5511 Manual SECTION 3 PROGRAMMING Page 16 ...
Page 40: ...Page 39 ...
Page 41: ...EGRO 5511 Manual SECTION 4 ELECTRICAL Page 40 ...
Page 50: ...Page 49 ...
Page 51: ...Page 50 ...
Page 52: ...Page 51 ...
Page 53: ...EGRO 5511 Manual SECTION 5 HYDRAULIC STEAM Page 52 ...
Page 58: ...EGRO 5511 Manual HYDRAULIC STEAM Brew Group Assembly D D F G C C C C E E H B A Page 57 ...
Page 60: ...Page 59 ...
Page 61: ...EGRO 5511 Manual SECTION 6 ADJUSTMENT MAINTENANCE Page 60 ...
Page 69: ...5 Page 68 ...