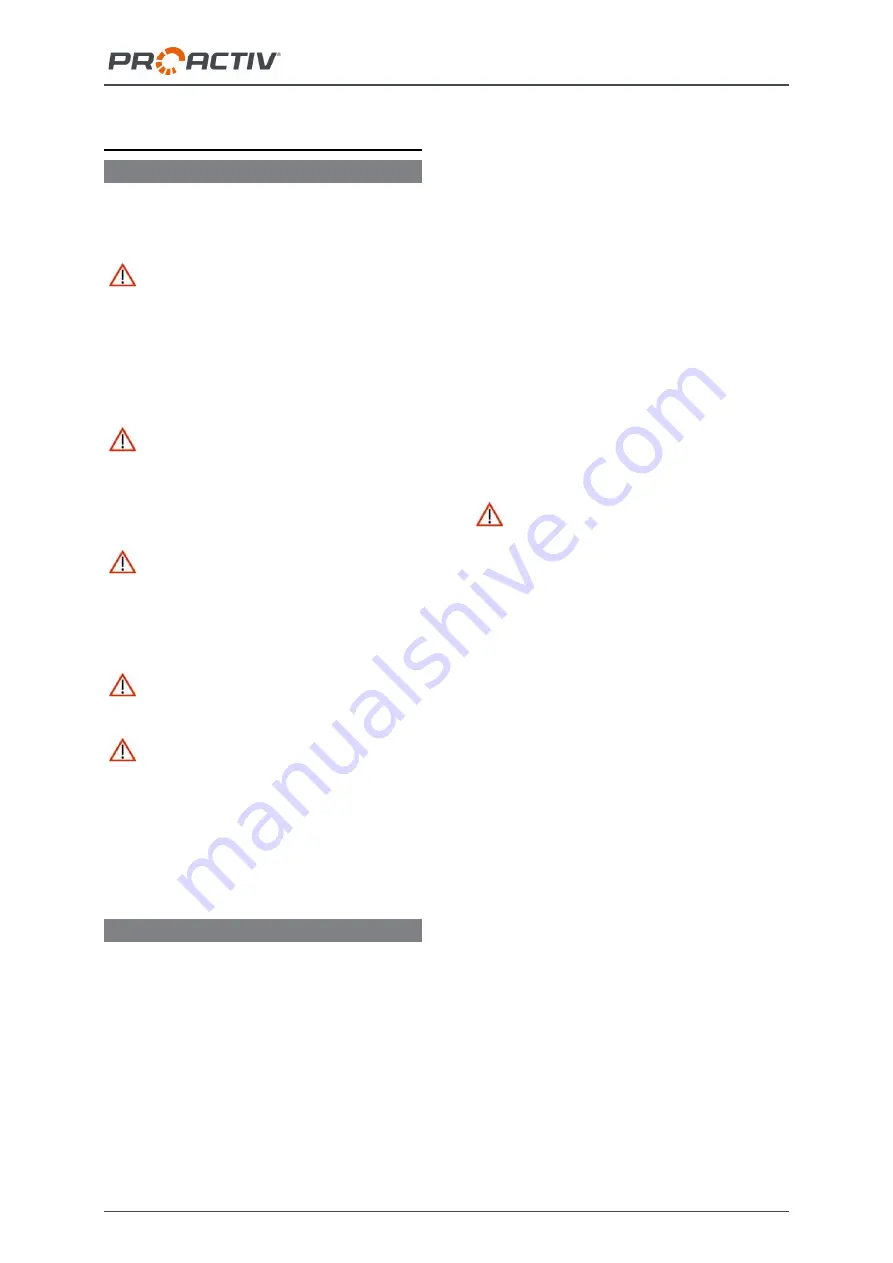
Usage instructions BUDDY 4all & classic
59
32 Maintenance
32.1 General instructions
The product is not a maintenance-free device.
Therefore, please observe the following in-
structions about maintenance.
If repairs are required or there are any
defects in your product, in the interests of your
own safety, you should contact your rehabilita-
tion specialist dealer or PRO ACTIV before
using it again and have the defect remedied.
Screws and other elements need to be se-
cured properly again after repairs.
For tyres with tread: As soon as there is
one or more points with less than 1
mm of
tread on the tyres, the tyres must be changed
as otherwise there is an increased risk of an
accident.
For tyres without thread: As soon as there
is one or more points where the tyre carcass or
the puncture-proofing is visible, the tyres must
be changed as otherwise there is an increased
risk of an accident.
Only manufacturer's original parts may be
used when ordering spare parts.
Repairs and conversions to the product
may only be carried out by your rehabilitation
specialist dealer or PRO ACTIV.
Tightening torques and securing details for
fastening elements as shown in the table in
Chapter 37 must be observed.
32.2 Service schedules
There is some
maintenance work or checks
which should be carried out by the user
themselves
at regular intervals (approximately
every 4 weeks depending on the frequency of
use):
Check the tyres for damage, foreign bodies
and any cracks that form.
Check the tyre pressure and correct if
needed (the tyre pressure should always
be as printed on the tyre covers).
Check the brakes (function, wear on brake
pins).
Clean and oil the pivot points of the brakes
and check the ease of movement or actua-
tion force of the brake levers.
Check the function of the anti-tipping de-
vice.
Check the stable stand of the seat and
backrest upholstery.
Check the tight fit of the fixing screws on
the seat and back system.
Check the function and ease of running of
the quick release axles of the drive wheels
and caster forks.
If you should discover any problems dur-
ing these checks, please immediately contact
your rehabilitation specialist dealer or
PRO ACTIV. Service and repair work on the
product may only be carried out by your reha-
bilitation specialist dealer or PRO ACTIV.
In addition to these maintenance tasks/checks
by the user, PRO ACTIV has prescribed
maintenance tasks to be carried out by the
rehabilitation specialist dealer or
PRO ACTIV
for safe operation of the product
and to minimise the risk to the user or third-
parties.
The initial inspection is performed six weeks
after delivery. The maintenance schedule can
be found in the inspection lists in chapter 40.
Subsequent inspections are then always per-
formed a year after the last inspection. The
maintenance schedule can be found in the
inspection lists in chapter 40.
After extreme stresses, such as during holi-
days where the product was exposed to sand,
sea water or snow, an additional deep clean
and inspection by your rehabilitation specialist
dealer is recommended.
To maintain the warranty validity, the perfor-
mance of the maintenance tasks must be doc-
umented. Any faults identified during mainte-
nance work must be rectified and documented
as such before further use of the product.