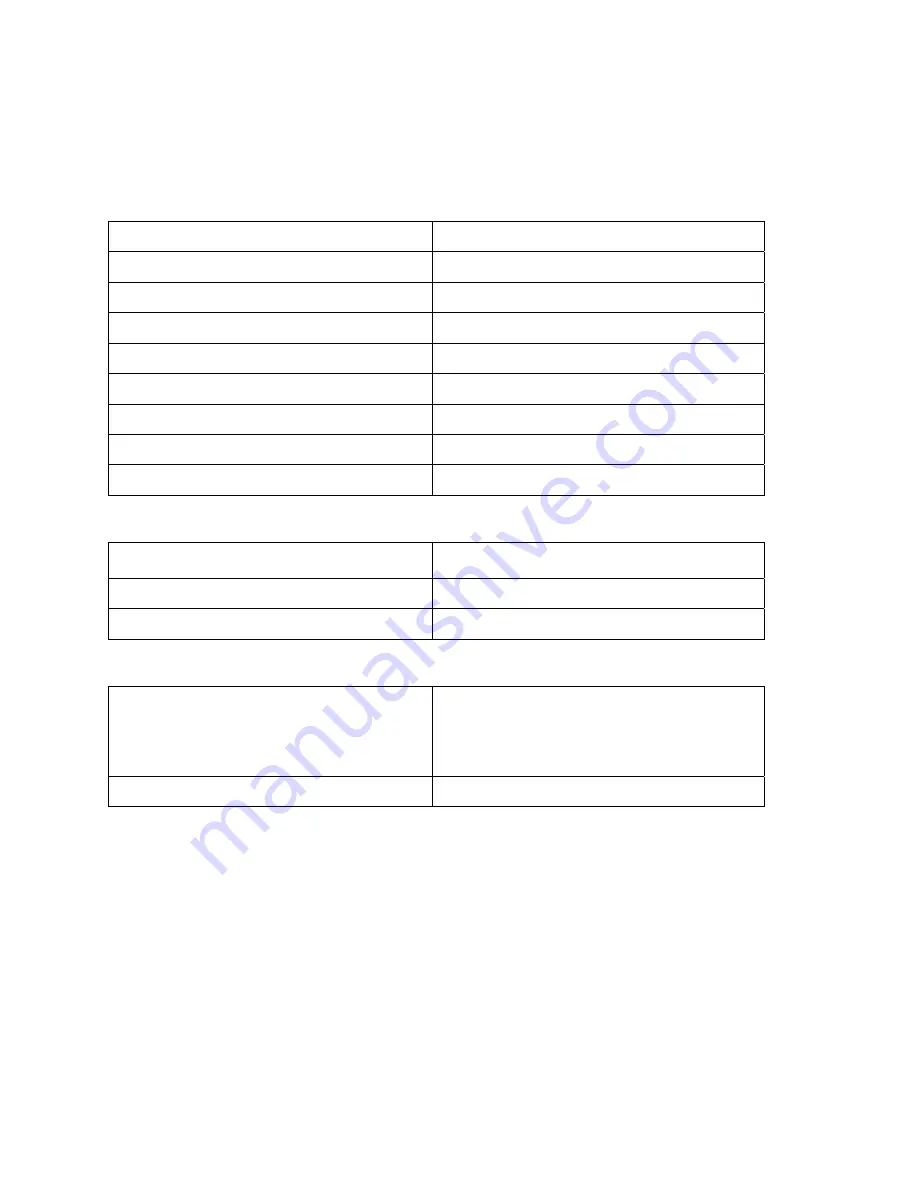
1. Specifications and features
1.1. Output
Maximum Power
12.5kW
Maximum Apparent Power
25kVA @ 240V input
Minimum Power Factor
0.5 @ 480V input
Duty Cycle
100%
Maximum Voltage
500V
Power Transformers (6)
2 :1
Frequency Range
135kHz to 400kHz
Maximum response time
0.1s
Minimum Allowed OFF-Time
0.5s
1.2. Input
AC line-to-line voltage
240V
10%, 3
, 50 to 60Hz
AC line current
35A @ 240V
AC power
14.5kVA
1.3. Physical
Dimensions: Depth
Width
Height
16in (41cm)
20in (51cm)
43.75in (111cm)
Weight
275lb (125kg) approximately
1
Inverter output power i.e. includes power losses in heat station.
2
Mainly limited by the rating of resonant capacitors. Consult manufacturer for operating
at output voltages above 500V rms.
3
When using the adjustable start-frequency feature.
3