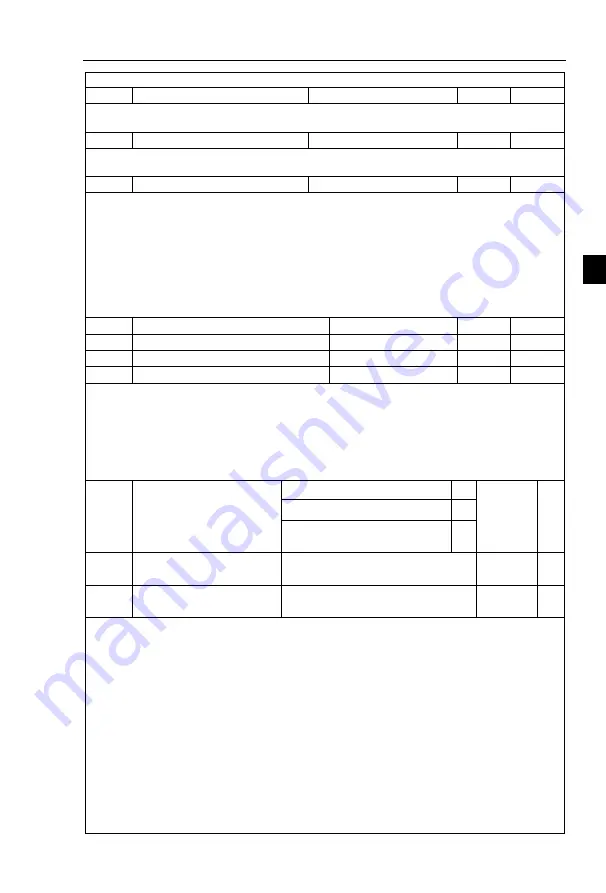
Chapter 5 Function parameter
79
Ch
ap
ter 5
inverter's rated torque.
F5.09
Vector control differential gain
50% to 200%
150%
☆
For the sensorless vector control, the parameter can be used to adjust the motor speed and
stability: if the speed of motor with load is low, increases the parameter and vice versa decreases.
F5.10
Speed loop filter time constant
0.000s~0.100s
0.000s
☆
Under vector control mode, properly increases the filter time when speed fluctuate wildly; but
do not excessively increases, or the lag effect will cause shock.
F5.11
Vector control over excitation gain 0~200
64
☆
In the process of the inverter's deceleration, the over-excitation control can suppress the rise
of bus voltage to avoid over-voltage fault. The greater over excitation gain, the stronger the
inhibitory effect.
For the occasions that the inverter's deceleration easily cause over pressure alarm , the over
excitation gain needs to be improved. But if over excitation gain is too large, which easily lead to
the increase of output current, you need to weigh in practical applications.
For the small inertia occasions that the inverter's deceleration will not cause voltage rise, it is
recommended to set over excitation gain as 0; the set value is also suitable for the occasions with
braking resistor.
F5.12 Excitation regulator proportional gain
0~60000
2000
☆
F5.13 Excitation regulator integral gain
0~60000
1300
☆
F5.14 Torque regulator proportional gain
0~60000
2000
☆
F5.15 Torque regulator integral gain
0~60000
1300
☆
The regulator parameters of vector control current loop PI, the parameter will be obtained
automatically after performing asynchronous motor parameters comprehensive auto tuning or
synchronous motor parameters comprehensive auto tuning and generally do not need to modify it.
It is reminded that the dimension that this current loop integral gain adopted is not the
integration time, but the direct set integral gain. Therefore, if the setting of current loop PI gain is
too large, which may cause the oscillation of entire control loop, in the event of oscillation, you
can manually reduce PI proportional gain and integral gain.
F5.16
Synchronous machine
weak magnetic mode
No weakening magnetic mode
0
1
Automatic adjustment mode
1
Compu auto-adjustment
synthesis mode
2
F5.17
Synchronous machine weak
magnetic gain
0
~
50
5
F5.18
Synchronous machine output
voltage limit Margin
0
~
50%
5%
The parameters are used for synchronous machine weakening magnetic control.
F5.16=0 No weakening magnetic mode
Synchronous machine does not perform weakening magnetic control. At this time, the
maximum value of the motor speed can be related to the inverter‟s bus voltage. The advantage is
that there is no weakening magnetic current and the output current is small. The disadvantage is
that the operating frequency cannot reach the set frequency, if customer wishes to achieve higher
speeds require the weakening magnetic function to be turned on.
(
2
)
F5.16=1 Automatic adjustment mode
This kind of weakening magnetic method is simple and reliable. The higher the speed is, the
weaker the magnetic current is. When the rated current of the motor is reached, it is not allowed to
increase the speed anymore. Otherwise, it will be overloaded if it is running for a long time. If it is
required to be quickly and weakly magnetized, the synchronous machine may be appropriately
increased by Weak magnetic coefficient F5.17, but excessive F5.17 will caused current instability.
(
3
)
F5.16=2 Compu auto-adjustment synthesis mode
In this mode, the flux-weakening current is adjusted faster, this mode can be set when the