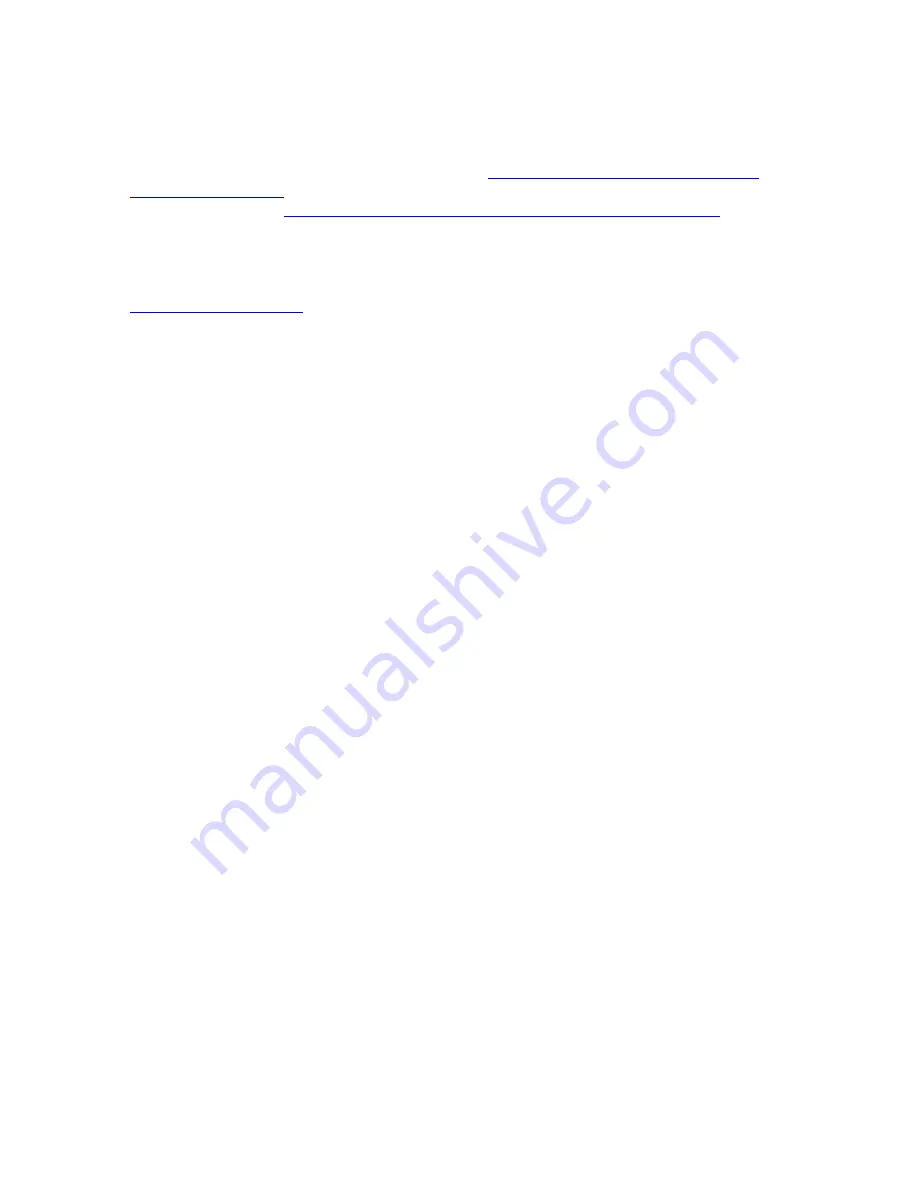
Contacting Powermetrix
General
For general information regarding Powermetrix products and services, contact one of the
following representatives listed on the website at
http://www.powermetrix.com/contact-
us/representatives-2/
. For customers outside the US, please visit the following representatives
list on the website at
http://www.powermetrix.com/contact-us/intl-representatives/
.
Technical Support
For technical support, please contact the factory at (865) 218-5800 (877-966-5851 toll free) and
ask for “Powermetrix Technical Support.” You may alternatively email Powermetrix at
. The support staff will answer questions about the operation and care of
your equipment, assist you in troubleshooting a problem, and help you overcome common
application difficulties whenever possible. If it becomes necessary for your equipment to be
returned to us for any reason, you will be issued an RMA number during the technical support
contact.
Feedback
Powermetrix depends on information from our customers to continue the attributes of quality,
dependability, and simplicity associated with our products. We invite you to contact our Technical
Support office.
Calibration and Certification
Your Powermetrix equipment is calibrated and certified effective the date of shipment.
Powermetrix requires the unit to be calibrated by Powermetrix or a Powermetrix authorized
service facility on an annual basis to insure accuracy and currency of installed electronic
components. In addition, current and voltage probes are also required calibration on an annual
basis or when dropped, damaged, or suspect of improper operation. The unit is identified as
calibrated by a sticker stating the date of calibration and next due date of calibration. A certificate
of calibration is provided to you to verify compliance to inspectors. A permanent record of your
calibration is maintained by Powermetrix. For information on calibration services, contact
Powermetrix Technical Support.
Additional services to be included at no additional charge during annual calibration:
1. Inspection of probes, cables, and internal circuit boards
2. Proper maintenance and/or prevention to any suspect components
3. ECN’s (Engineering Change Notices)
4. Update firmware
5. Reproducibility report for clamp-on probes
6. Service Report for all work completed
Rev 1.5
7