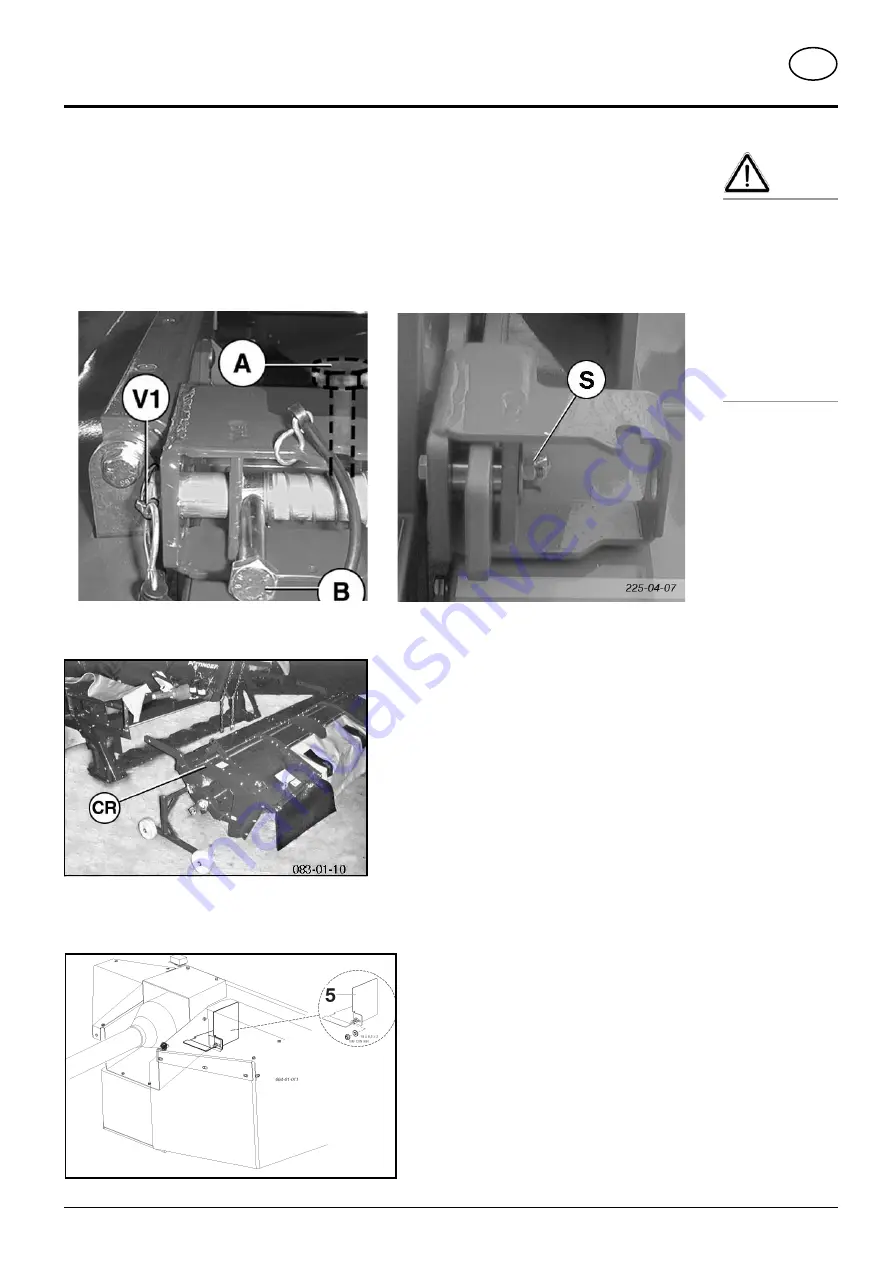
- 18 -
0500-GB AUFBEREITER_348
GB
CONDITIONER
5. Release left and right locks
• Spring loaded positioning bolt up to 2004
model
Remove linch pin (V1) and release bolts
• Pos. A = released
• Pos. B = Locked
• Screwed in from 2004 model
Remove screw (S)
(Spring loaded positioning bolt = optional)
6. Always park conditioner steadfast.
7. Mount the guard (5)
This guard (5) prevents the penetration of dirt into the
gear area.
Mounting the conditioner
- is effected in the reverse sequence to
dismounting.
Important!
When
mowing
without
conditioner,
protective
elements and
the both swath
formers (SB)
must be mounted
additionally on the
cutter bar. Parts
see spare parts
list.