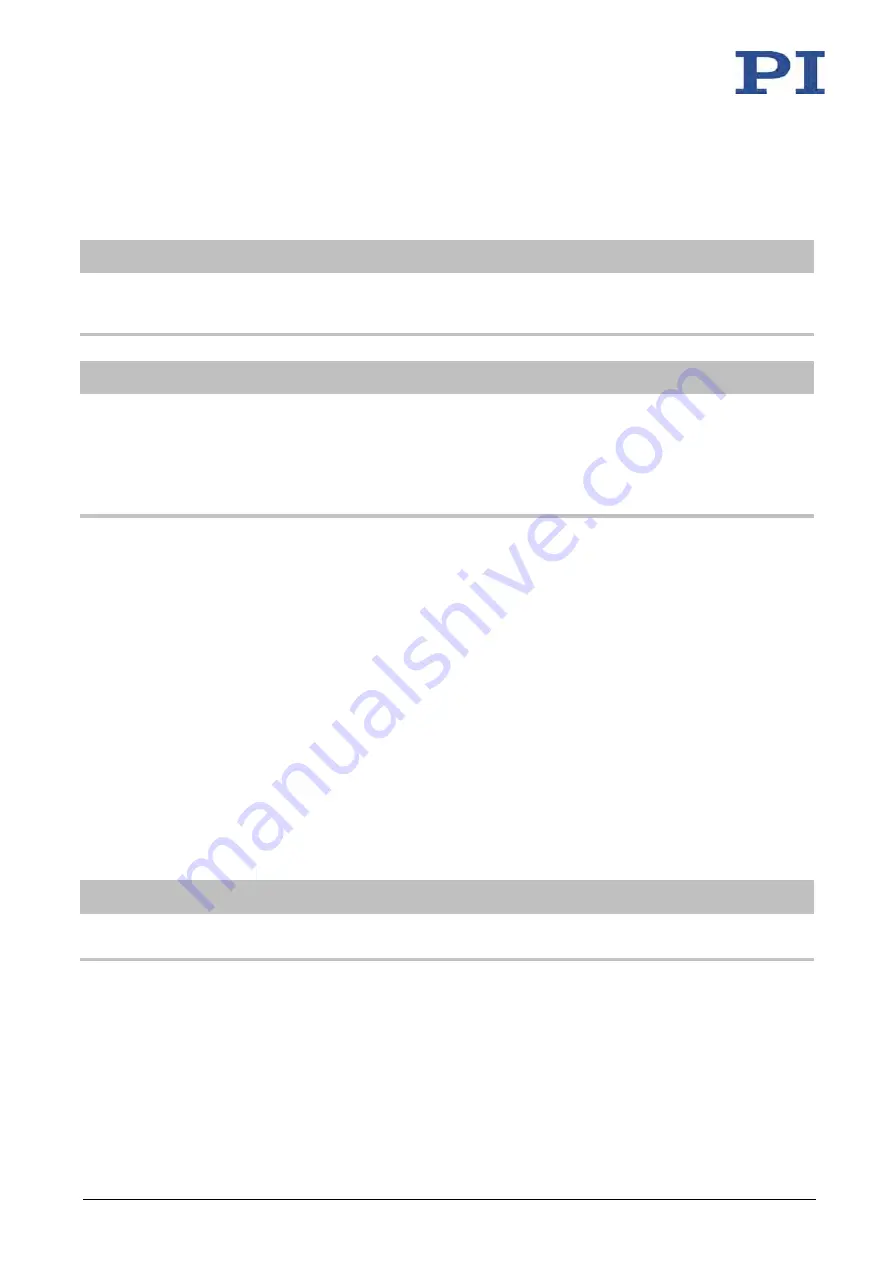
6 Startup
E-625 Piezo Servo Controller
PZ166E
Version: 2.0.0
27
The E-625 or the positioner was replaced. In this case, the displacement of the axis
must first be recalibrated (p. 51).
INFORMATION
In regular intervals, check the position of the positioner at 0 V input voltage and adjust the
sensor zero point if necessary. This can extend the lifetime of the piezo actuator in the
positioner.
INFORMATION
When the yellow overflow LED comes on, the amplifier is near to its range limit (piezo voltage
outside the range of –30 V to +130 V).
In open-loop analog mode, do
not
exceed the recommended input voltage range of –2 to
+12 V.
Adjust the zero point of the sensor when the overflow LED comes on in closed-loop
operation (servo mode ON) (p. 27).
6.3
Adjust the Sensor Zero-Point
Changes in temperature or changes in the mechanical load can cause small deviations of the
sensor zero point.
Objectives of the zero-point adjustment:
Make the entire travel range available:
When the sensor zero point is set correctly, the complete output voltage range of the
amplifier can be used in closed-loop operation.
Prevent the piezo actuators from damage:
In open-loop operation, the displacement of the positioner with 0 V piezo voltage
should already be about 10 % of the travel range (sensor monitor signal is +1 V). Then
the average applied voltage is reduced and this lengthens the lifetime of the piezo
actuator in the positioner without reducing the nominal travel range.
INFORMATION
Zero-point adjustment of the sensor changes the physical zero position of the positioner in
closed-loop operation.
Requirements
You have read and understood the general notes on startup (p. 23).
For computer-controlled mode only: