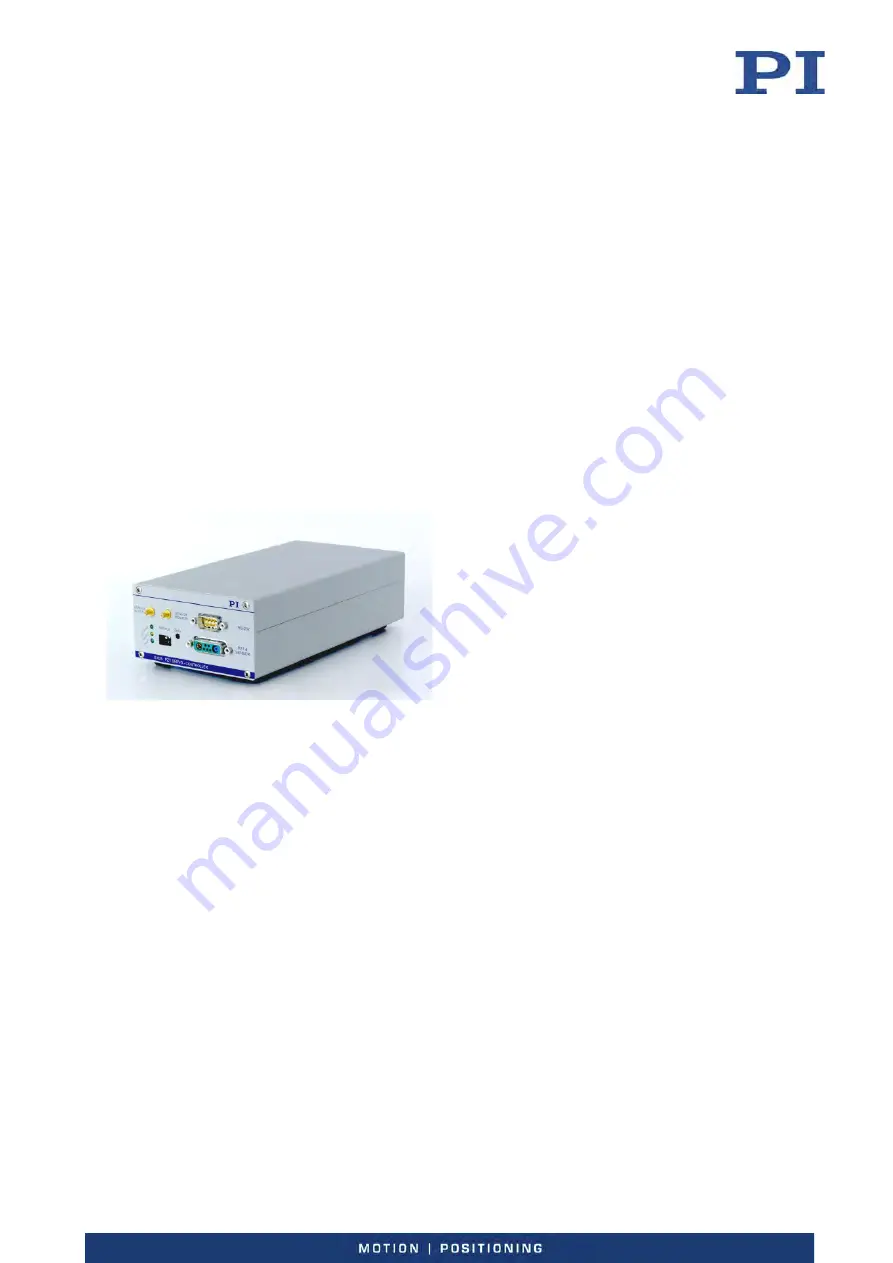
Physik Instrumente (PI) GmbH & Co. KG, Auf der Roemerstrasse 1, 76228 Karlsruhe, Germany
Phone +49 721 4846-0, Fax +49 721 4846-1019, Email [email protected], www.pi.ws
PZ166E
E-625 Piezo Servo Controller
User Manual
Version: 2.0.0
Date: 15.09.2021
This document describes the following products:
E-625.CR
Piezo servo controller, single channel, for
capacitive sensors
E-625.C0
Piezo servo controller, single channel, for
capacitive sensors, only analog control