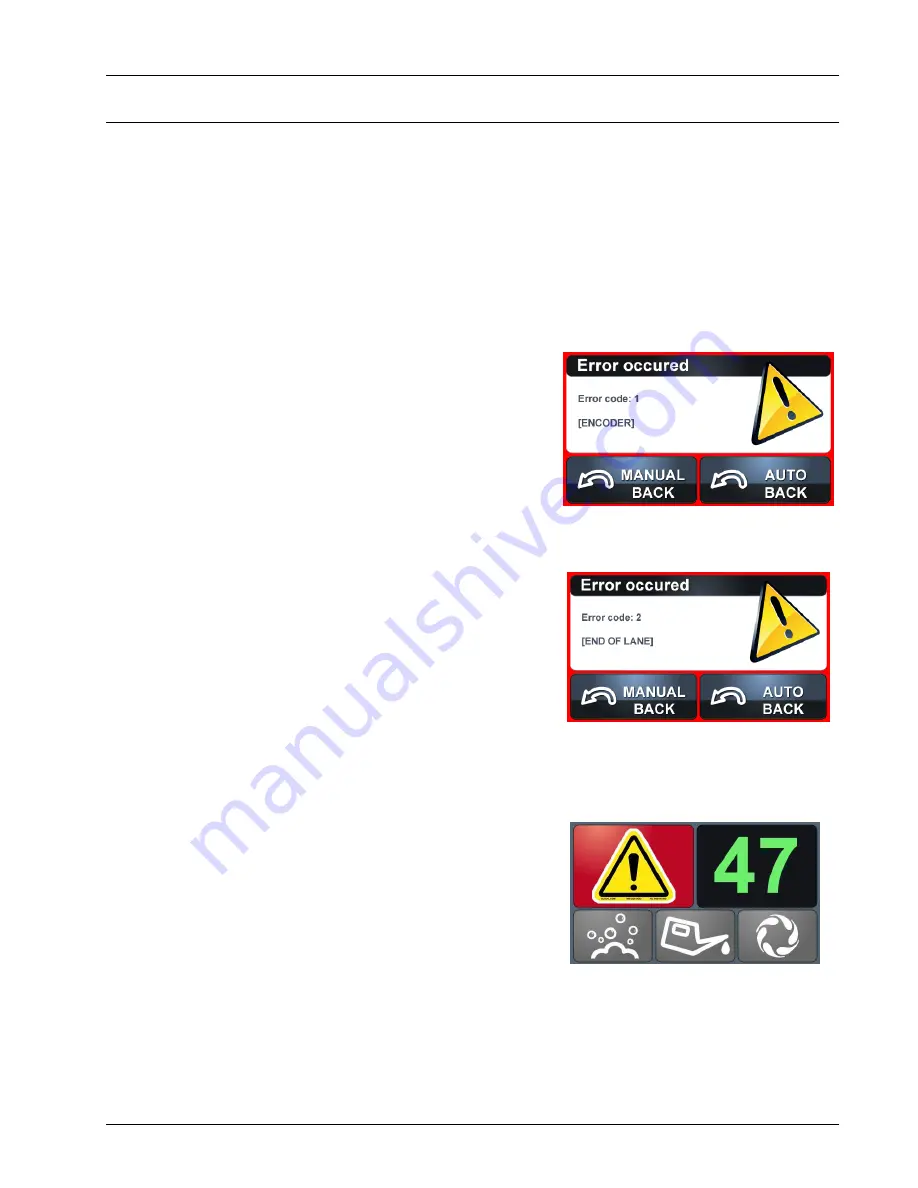
Troubleshooting
5-10
Rev. Date:
01/22
61-900040-000
5.2 RECOVERING IF THE PHOENIX LT4 STOPS ON THE LANE
There are five reasons the Phoenix LT4 might unexpectedly stop on the lane:
The machine became unplugged or lost power.
The encoder stopped counting or missed too many counts.
The oil compartment door became unlatched and tripped the interlock switch.
The guide rollers were too tight against the lane.
Gutter bumpers are too high and the machine cannot pass the elevated section.
Pressing the EMERGENCY STOP button or opening
the cover would also stop the machine.
If the machine stops on the lane, an error will be
displayed on the screen. Generally, this error will be
either an encoder or the end of lane error (Figure 5- 1
and Figure 5-
respectively). Regardless of the error,
the machine will need to be returned to the foul line
and lane to be reconditioned.
If the Auto Back option is selected, the machine will lift
the vacuum head off the lane and run the machine
back to the foul line using the drive motor. This option
is the preferred method for returning the machine to the
foul line.
If there is a drive motor or another failure that prevents
the machine from returning itself to the foul line, the
Manual Back option should be used. Select the
Manual Back button, wait for the vacuum head
solenoids to engage, and then pull machine by the
handle back to the foul line.
A screen similar to Figure 5- 3 will be displayed when
returning the machine to the foul line. The last reading
of the odometer is displayed in the upper right portion of
the screen; this value will decrease as the machine
approaches the foul line.
If it is not possible leave the machine energized while
manually returning it to the foul line, pull the machine
slowly to avoid damage to the vacuum head.
Once the Phoenix LT4 has returned to the foul line and the problem has been corrected,
restart the machine to have it perform the same operation(s) it was performing when it
stopped.
Figure 5- 1
Figure 5- 2
Figure 5- 3