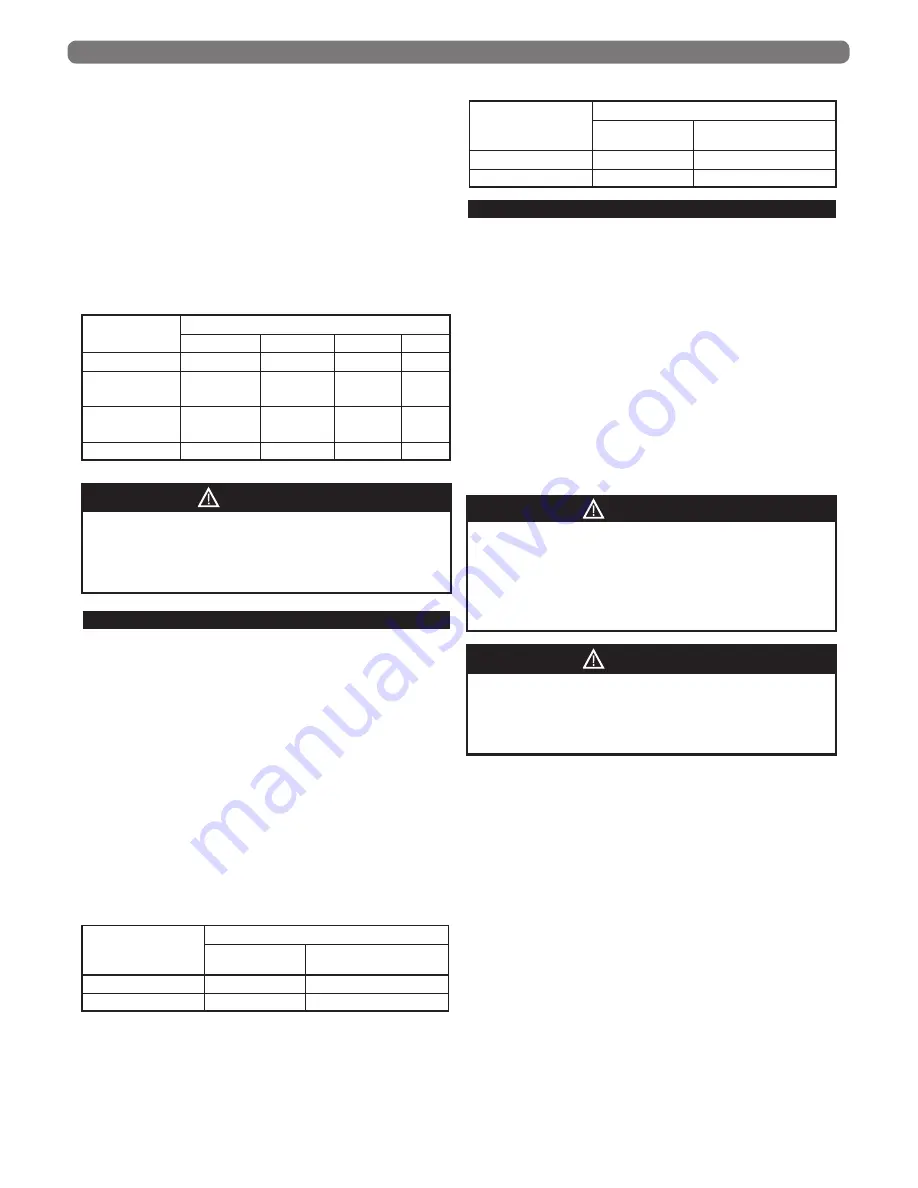
b. The Series PFC
TM
has a built-in De-Air feature that
activates on initial power up. Allow this cycle to
run fully to help drive any trapped air out of the
unit and to the air vent or vents. Refer to Section
8 for more details on the De-Air Cycle.
c. It is recommended that a water meter be installed
on the system fresh water intake to monitor the
system for any leaks by monitoring make-up water
usage. Untreated fresh water sources will introduce
oxygen, minerals and contaminants into system.
d. Correct any system leaks prior to placing the boiler
in operation.
C. OPERATING PARAMETERS
1. The Series PFC
TM
boiler is designed to operate in a
closed loop hydronic heating system under forced
circulation. This requires the system to be completely
filled with water and requires a minimum water
flow rate through the boiler to assure proper flow
distribution.
2. The minimum system operating pressure is 14.5 PSI
(100 kPa). Be sure to set the air-side pressure on the
expansion tank to match the system water pressure
before installing it.
3. Table 4.2 lists the minimum flow rates for each Series
PFC
TM
model covered in this manual. Also shown is
the minimum flow rate for 50% glycol solution. For
other glycol concentrations, contact your PB Heat,
LLC representative for the minimum flow rates.
4. Section 4.F provides detailed information about using
glycol for freeze protection. Table 4.3 provides the
water volume of the heat exchangers for calculating
the system volume.
D. SYSTEM COMPONENTS
Figure 4.1 shows the symbol key for piping diagrams in
this section. The following are brief descriptions of system
components.
1.
Pressure/Temperature Gauge
: A combination
pressure/temperature gauge is provided with each
P
ure
F
ire
®
boiler to be mounted in the piping from the
boiler supply to the system as shown in Figure 4.2.
Most local codes require this gauge.
2.
Air Elimination
: Closed loop hydronic systems require
air elimination devices. As the system water is heated,
dissolved oxygen and other gases will separate from
the liquid. An air elimination device (such as a TACO
Vortech
®
Air Separator) is required to remove the
dissolved gases preventing corrosion in the piping
system and eliminating noise.
3.
Expansion Tank
: An expansion tank (such as a Bell
& Gossett Series HFT) is required to provide room
for expansion of the heating medium (water or glycol
solution). Consult the expansion tank manufacturer’s
instructions for specific information regarding
installation. The expansion tank is to be sized for the
required system volume and capacity. In addition,
be sure that the expansion tank is sized based on the
proper heating medium. Glycol solutions may expand
more than water for a similar temperature rise.
4.
Y-Type Strainer or Filter Ball
®
Valve
: PB Heat, LLC
recommends the use of a strainer device in the system
to prevent dirt or sediment from clogging the heat
exchanger. A 20 mesh stainless steel screen is adequate
to protect the heat exchanger. The strainer should be
cleaned often in the first several months of operation. The
Filter Ball
®
Valve from Jomar International incorporates
a strainer into a ball valve which allows the technician to
isolate the water circuit while cleaning the strainer.
17
Table 4.2:
Recommended Water Treatment Products for
use in Stainless Steel Condensing Boiler Applications
Supplier
Fernox
Sentinel
Sotin
ADEY
Universal Cleaner
Restorer
X300
-
-
Sludge Remover
Cleaner F1,
Protector F3
X400
Sotin 212
-
Inhibitors
Protector F1/
Alphi 11
X100, X500 Sotin 212
MC1+
Antifreeze
Alphi 11
X500
-
-
Do not use petroleum based cleaners when cleaning
the boiler system. Damage to the gaskets found in
typical system components can occur resulting in
significant property damage.
WARNING
Use only inhibited propylene glycol solutions which
are specifically formulated for hydronic systems.
Unlike automotive antifreeze, solutions for hydronic
applications contain corrosion inhibitors that will
protect system components from premature failure
due to corrosion.
CAUTION
Use only inhibited propylene glycol solutions
which are specifically formulated for hydronic
systems. Ethylene glycol is toxic and may cause an
environmental hazard if a leak or spill occurs.
WARNING
P
ure
F
ire
®
Model
Total Water Capacity
Gallons
Liters
PFC-625
5.6
21.3
PFC-750
6.36
24.8
Table 4.4: Heat Exchanger Water Capacity
P
ure
F
ire
®
Model
Minimum Flow Rate
Water
GPM (LPM)
50% Glycol Solution
GPM (LPM)
PFC-625
14.3 (54.2)
17.9 (67.8)
PFC-750
16.3 (61.7)
20.4 (77.2)
Table 4.3: Minimum Boiler Flow Rates
WATER PIPING & CONTROLS