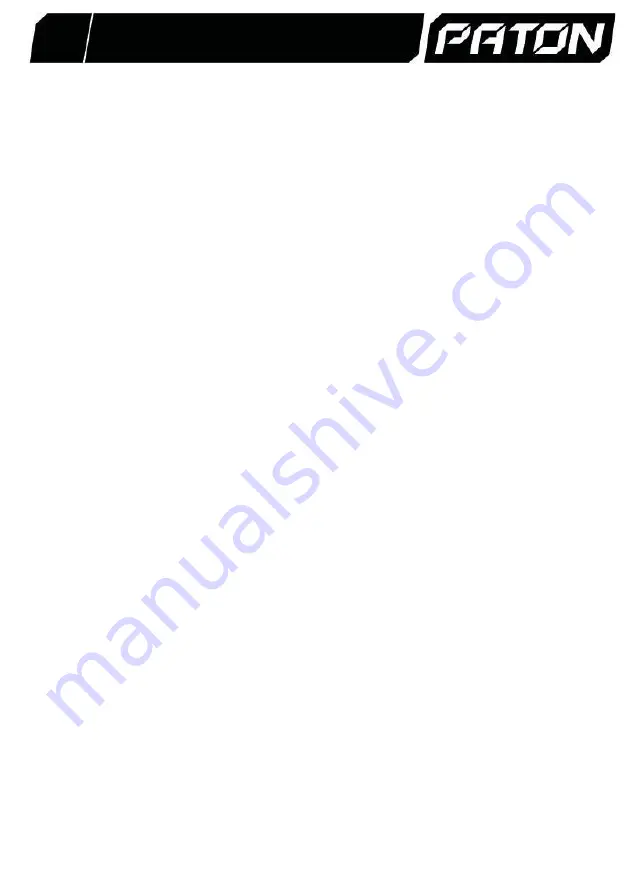
- 19 -
PATON
ProMIG
DC MMA/TIG/MIG/MAG
3.5 CURRENT-VOLTAGE CHARACTERISTIC SLOPE CONTROL FUNCTION
The slope of the current-voltage characteristic, often denoted as [CVS], varies depending on
the type of electrode coating. For rutile-coated electrodes, like E6013, a standard [CVS] slope
setting of 1.4 V/A is generally advised. However, for electrodes with a basic or main coating,
specifically the E7015 type, a more suitable [CVS] slope is around 1.0 V/A. Electrodes coated
with cellulose, such as E6011, have unique requirements. Their [CVS] slope is recommended
to be within the range of 0.2 to 0.6 V/A. Additionally, for optimal performance with E6011
electrodes, one might need to increase the "Arc-Force" level, labeled [u.AF], to as high as
18V in certain situations. However, always refer to the electrode manufacturer's guidelines
for the most accurate settings.
To change the value of any function in the current welding mode, see section 6.1.
3.6 SHORT-ARC WELDING FUNCTION
This function is particularly useful when welding ceiling welds, when it is necessary to ensure
that the welding arc does not extend too far. For this purpose, the "Short arc" function [Sh.A]
can be set to the ON position. By default, it is set in the OFF position.
To change the value of any function in the current welding mode, see section 6.1.
3.7 NO-LOAD VOLTAGE REDUCTION FUNCTION
When carrying out welding work in containers, tanks and where increased electrical safety is
required, the no-load voltage reduction function can be activated.When the electrode is
disconnected from the workpiece, the voltage at the source terminals drops to a safe level
below 12 V after 0.1 seconds.
This requires a no-load voltage regulator [BSn], which is available on this model, but by
default it is in the OFF position, i.e. off, as it is known that enabling such a function slightly
degrades arc ignition.
To change the value of any function in the current welding mode, see paragraph 6.1
3.8 PULSED CURRENT WELDING FUNCTION
The pulse current function in SMAW (Shielded Metal Arc Welding) introduces a controlled
modulation between a higher peak current and a lower base current during the welding
process. This pulsation aims to optimize the balance between metal deposition rate, heat
input, and penetration.
During the peak current phase, sufficient energy is delivered to ensure proper fusion and
penetration, while the base current phase maintains the arc stability and reduces the overall
heat input. This controlled pulsing can aid in achieving a more consistent and refined weld
bead, mitigating excessive heat build-up and potential warping or distortion of the
workpiece.
Summary of Contents for PROMIG-160
Page 1: ...j...