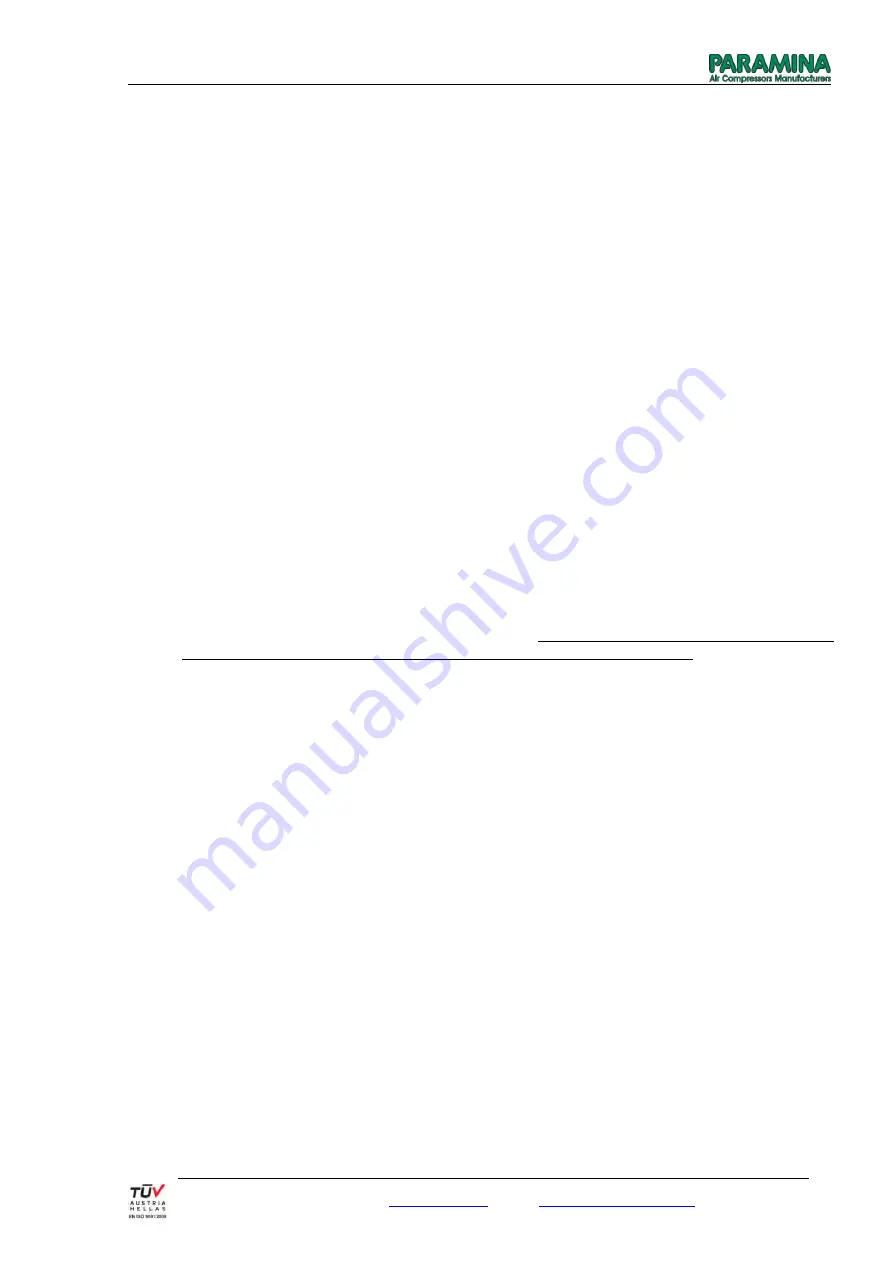
User Manual -
Cyclone Silent -
1-2018 edition
PARAMINA SA – Byway Evaggelistrias str. 19300 Aspropirgos, Greece, Tel: 0030 210 5575860-1
Fax: 0030 210 5575868, email:
- website:
www.paramina-compressors.com
9
4.
Installation - Operation
4.1.
General Specifications
High pressure compressors are complete units for filling cylinders with compressed air at 225 bar (3200 psi) and
330 bar (4700 psi). They are mostly used for compressing breathing air for divers, fire brigades, military, paint ball
applications, etc.
Cyclone
is a 4 staged, air cooled, piston compressor with 4 cylinders, 3 intercoolers and 1 final aftercooler. The
machine is also equipped with condensate separators after the 1
st
and 2
nd
stage, coalescing filters (for retaining
particles and oil droplets down to 0.01 ppm) after the 3
rd
and 4
th
stage, all accompanied with automatic and manual
drains. The compressor has pressure control in all stages of compression, with pressure switches and mechanical
safety valves, as well as BA final filter at the final pressure (after fourth stage) which incorporate molecular sieve for
dehumidification and activated carbon for air purification.
All functions of
Cyclone
are completely automated through
Paramina Controller
(digital control panel). You simply
adjust the desirable maximum operating pressure and press the start button.
The compressor starts its operation and will stop when the pressure reaches the preset maximum value.
4.2.
Installation - First start of the compressor
All compressors are tested and pre-adjusted by the manufacturer before they are shipped to the buyer.
They can start their operation immediately on the following conditions that are considered necessary, for safety
and ease.
Anyone who will be handling the unit must read carefully all contents of this manual so as to have full knowledge of
the product.
1.
Choose carefully the installation place of the compressor. The place must not be burdened by unfavorable
environmental conditions (toxic substances – explosives – fumes – dirt – debris etc).
2.
Place the compressor in a well-ventilated area. Make sure that the intake air for the compressor is clean
and cool.
Prevent the hot cooling air from recirculation to the cooling air intake.
Make sure that foreign
objects cannot get into the compressor with the intake air. Make sure that the intake air does not contain
any smells, fuel or fumes, explosive or inflammable gases or harmful substances.
3.
Turn the compressor by using the flywheel and make sure it turns freely. Do the same after overhaul of the
unit or a long-term out of service period.
4.
Check the rotation direction (follow the arrow) by pressing instantly the start-stop button. The same check
should be carried out after any service or reconnection of electrical supply.
5.
Before any start of the compressor, check oil level. It should always be at the top of the oil sight glass.
6.
The compressor should be placed in a completely horizontal position. If during operation there are
vibrations, adjust the anti-vibration pads of the stand until vibrations are minimized.
Installation room
>30m
3
.
ATTENTION:
Larger oil quantity may increase pressures inside the block and also cause leak of larger oil quantity in the
pneumatic air resulting in the creation of chars in the valves, burden the filters and affect their life duration, as well
as the quality of breathing air.
Smaller amount of oil means inadequate lubrication affecting the life duration of the compressor.