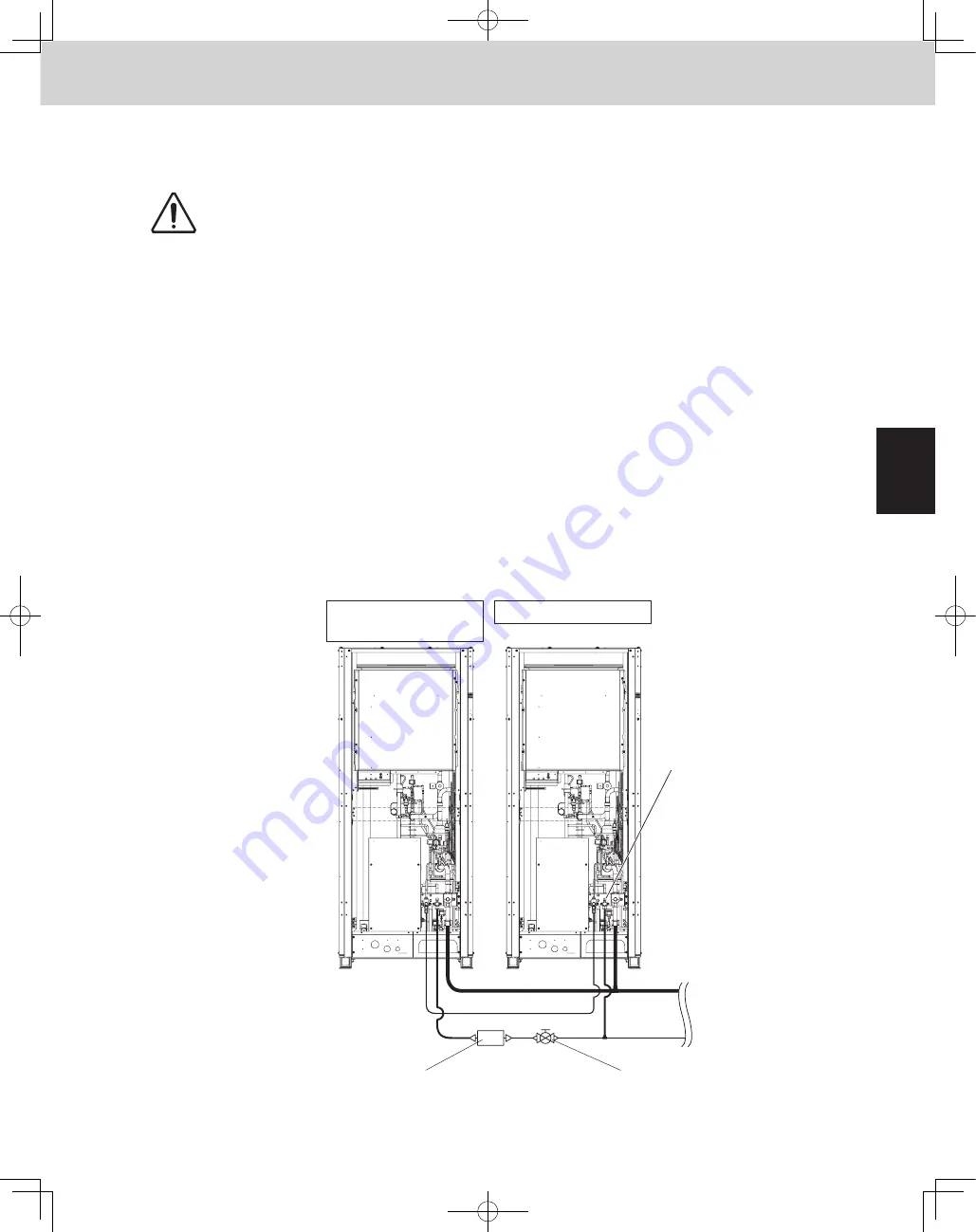
2
- 31
1
2
3
4
5
6
7
8
9
2WAY VRF SYSTEM
Outdoor Unit Repair Procedures
2WAY VRF SYSTEM
Outdoor Unit Repair Procedures
9. Compressor
9-2-4. Dry core cleaning
(A) If a ball valve is installed on the outdoor unit
If burning or other failures occur repeatedly at compressors within the same system, in many cases the cause is
acid, sludge, carbon, or other substances that remain in the refrigeration cycle as the result of insufficient cleaning.
If, when the oil is inspected, there is an outdoor unit where the oil color phase is 4.0 or higher, or where a sharp
odor is present, carry out all steps below to perform dry core cleaning.
And use the bidirectional dry core for refrigerant R410A.
(2) If all units are operated in Cooling mode, close first the liquid tube service valve then the ball valve on all outdoor
units where dry cores will be attached.
If all units are operated in Heating mode, close first the ball valve then the liquid tube service valve on all outdoor
units where dry cores will be attached.
(1) See “4-2-1. Cooling operation (for all units)” and operate all outdoor units in either Heating or Cooling mode.
(4) Connect a refrigerant recovery device to the liquid tube service port (Schrader-type valve) of all outdoor units
where dry cores will be attached, then recover the refrigerant from the tubing. Be sure that no air enters the
tubing at this time.
(5) As shown in Fig. 16, disconnect the tube that runs from the liquid tube valve to the ball valve on all outdoor units
where dry cores will be attached. Then attach the dry cores.
(6) At all outdoor units where dry cores are attached, pressurize with 484 psi (3.8MPa) of nitrogen from the liquid tube
service port and check for leaks.
(7) After evacuating all nitrogen gas from the tubing, apply vacuum from the liquid tube service port to all outdoor
units where dry cores are attached until the pressure is –14.7 psig {-101kPa, 5 Torr} or less.
(8) Fully open the liquid tube valve and ball valve on all outdoor units where dry cores are attached.
(9)
(10) Follow the above procedure, and replace all dry cores with new dry cores.
Operate all outdoor units for approximately 3 hours (in either Heating or Cooling mode).
(11) Operate all outdoor units for approximately 20 minutes (in either Heating or Cooling mode).
(12) Follow the instructions in “2. Discharging Compressor Oil” and drain a small amount of the oil from the oil
separators of all outdoor units where dry cores are attached. Check the color phase, odor, and other
characteristics.
(3) Press the
all units.
Pull out the SCT connector (2P) (YEL) (CN65) from the outdoor unit control PCB of the unit where pump-down
is being performed. When the SCT connector is pulled out, alarm F12 (sensor trouble) immediately occurs and
all outdoor units stop operating. Be sure that you do NOT grasp the lead wire when pulling out the connector.
Removing any other connector may not cause the units to stop. Therefore be sure to pull out only the SCT
connector.
(ON/OFF) button on the outdoor unit maintenance remote controller to stop the operation of
* This step is performed in order to expel refrigerant from the tubing between the liquid tube service valve and
the ball valve. Approximately 4 – 5 seconds is a sufficient interval between closing each of the 2 valves.
* If the outdoor unit maintenance remote controller is not available, use the following method to stop the operation
of all units:
When the hose is connected, internal pressure is applied by the remaining refrigerant in the
inter-unit tubing. The connection port employs a Schrader-type valve.
To determine when refrigerant recovery is complete, follow the instructions in the instruction
manual of the refrigerant recovery device.
CAUTION
9. Compressor
2WAY VRF SYSTEM
Outdoor Unit Repair Procedures
(13) If the results show that dry core cleaning is still necessary (for example, a color phase of 4.0 or higher)*,
return to Step (11) and repeat until the results are normal (including a color phase of 3.5 or less)*.
(14) Perform steps (1) – (4), and remove all dry cores. Then connect the tubing between the liquid tube valves
and the ball valves.
(15) At all outdoor units where dry cores were removed, pressurize with 484 psi (3.34MPa) of nitrogen from the
liquid tube service port and check for leaks.
(16) After evacuating all nitrogen gas from the tubing, apply vacuum to all outdoor units where dry cores were
removed until the pressure is –14.7 psig {-101kPa, 5 Torr} or less.
(B) If a ball valve is not installed on the outdoor unit
(17)
INSTALLATION:
Refer to the Installation Instructions for further information.
Charge with an amount of refrigerant equal to the amount that was recovered.
* Color sample sheet for degree of stain
(1) See “4-2-3. Refrigerant recovery procedures (2) : Indoor unit with no ball valve equipped.” Perform
pump down of the refrigerant from all indoor units and inter-unit tubing to the outdoor unit side.
(2) Cut the liquid tube at all outdoor units where dry cores will be attached, then attach the dry cores
and ball valves as shown in Fig. 16.
(3) For the next steps, see the steps (6) – (17) in “(A) If a ball valve is installed on the outdoor unit” on the previous
page.
Perform another dry core replacement after approximately 30 hours of system operation.
CAUTION
9. Compressor
Fig. 16
To indoor unit
Liquid tube
Ball valve
Dry core (bidirectional: for R410A refrigerant)
Balance tube
Gas tube
Outdoor unit for
cleaning by dry core
Normal outdoor unit
Liquid tube service port
(for ø5/16” (ø7.94mm)-
dia connector)
SM830237-07_北米向け2WAY_VRF.indb 31
18/06/18 18:48:19