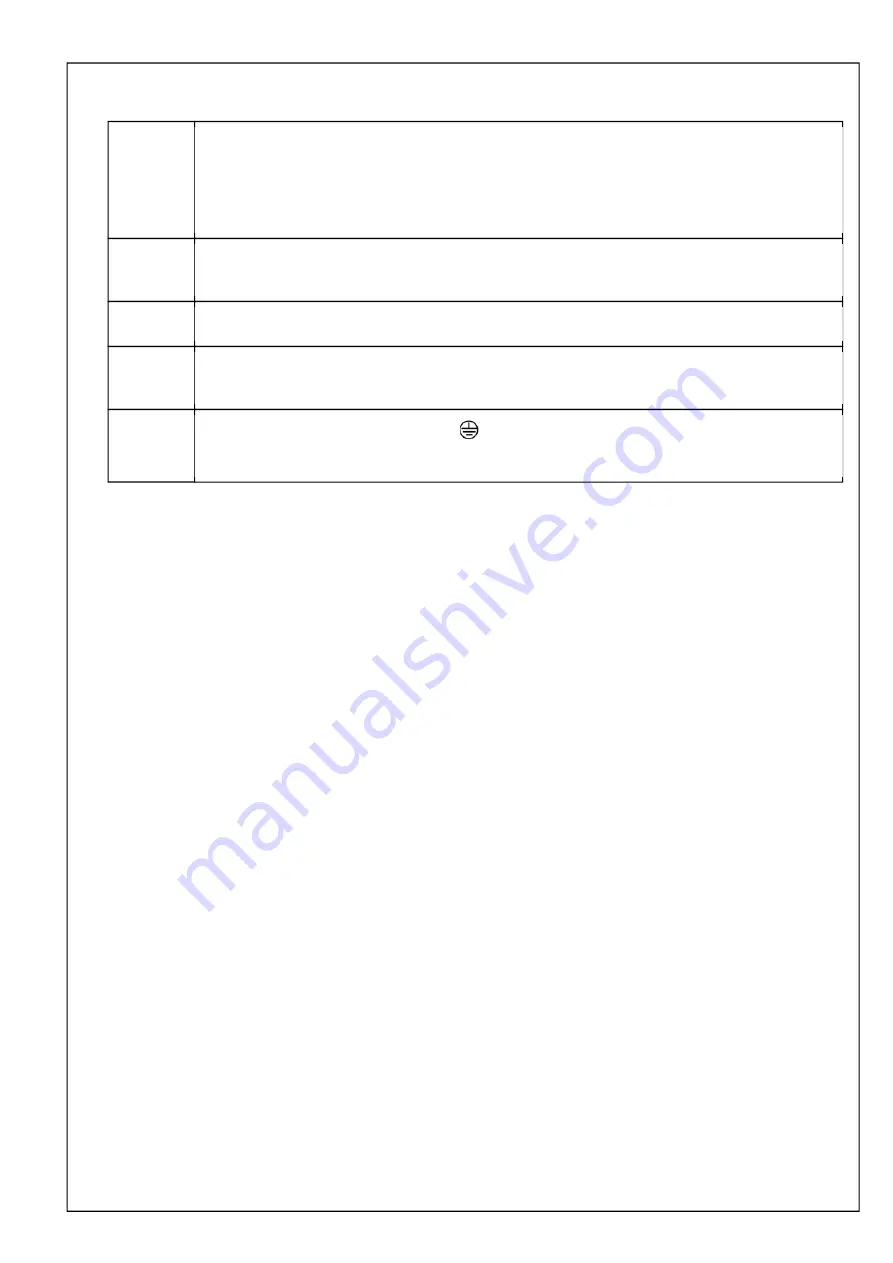
№
SX-DCT00221 -
39-
Panasonic Corporation
12.1 Configuration of peripheral equipment
Power
supply
100 V system: Single phase 100 V – 120 V
10%, 50/60 Hz
200 V system: Single / 3 phase 200 V – 240 V
10%, 50/60 Hz
Use the equipment under the environment of overvoltage category II specified by IEC60664-1.
In order to obtain overvoltage category
Ⅲ
, insert a transformer conforming to EN standard or IEC
standard to the input of brushless amplifier.
Use an electric wire size suitable to EN60204-1.
Fuse
breaker
Be sure to connect a specified no-fuse breaker certified by IEC standard and UL, or a fuse certified by UL
between power supply and noise filter. Observance of this condition allows conformance with UL508C (file
No.E164620) and UL1004 (file No.E166557).
Noise
filter
When installing one noise filter at the power supply for more than one brushless amplifier used, contact
the manufacturer of noise filter.
Surge
absorber
Install a surge absorber on the primary side of noise filter. However, in performing the voltage
resistance test of machine and equipment, be sure to remove the surge absorber; otherwise,
the surge absorber may be ruptured.
Grounding
Be sure to ground the grounding terminal (
) of brushless amplifier for preventing electric shock.
Brushless amplifier is provided with two grounding terminals. Connect the grounding wire of brushless
motor to the other one.