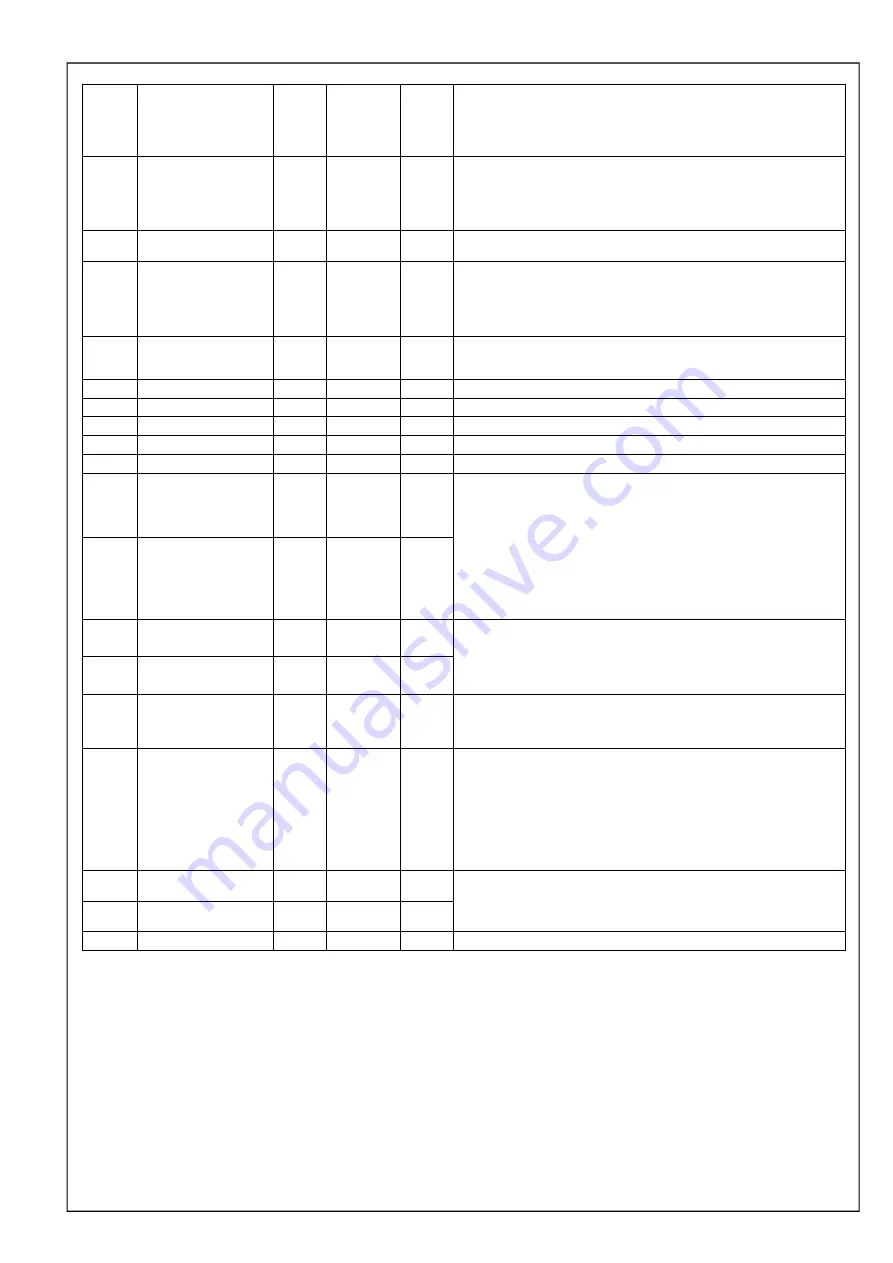
№
SX-DCT00221 -
15-
Panasonic Corporation
Parameter
No.
(Pr
□□
)
Name of parameter
Effective
after
power re-
setting
Setting
range
Default
Description
63
RS485 communication
response time
○
10~100
10
Communication response time is the shortest time for setting transmission mode in
RS485
bus for response after the motor has received communication data. Actual data re-
sponse
time depends on the type and data of order.
Unit [ms]
64
RS485 retry times of
communication
○
0~9
9
Set the retry times of RS485 communication.
0 - 8
: Number of retrials,
9
: No retrial
65
RS485 protocol
Timeout
○
1~255
2
Protocol timeout is the time allowed from reception of a character code to
reception of the next one in communication. If normal character code is not
received within this time, communication is timed out, and received data is
discarded. If timeout should continue to occur, and the number of detections
exceed the retry times, the motor trips due to RS485 communication error.
Unit [seconds]
6A
Trip history clear
0(No),
1(Yes)
nO
When " (1)" is set, trip history (Pr6b - 6F) is
cleared. Trip history is also cleared when 1 is set on
"PANATERM for BL" (sold separately).
6b
Trip history 1
―
―
Display the latest trip.
6C
Trip history 2
―
―
Display the 2nd latest trip.
6d
Trip history 3
―
―
Display the 3rd latest trip.
6E
Trip history 4
―
―
Display the 4th latest trip.
6F
Trip history 5
―
―
Display the 5th latest trip.
70
I
5 function selection
○
0~15
0
You can assign functions to
I5
,
I
6.
0
: Forced trip,
1
: Instantaneous stop,
2
: Deceleration stop,
3
: Homing start
∗
4
: Forward jog
∗
,
5
: Reverse jog
∗
,
6
. Point designation 1
∗
,
7
: Point designation 2
∗
8
: Run start
∗
,
9
: Sequential run start
∗
,
10
: Trip reset,
11
: Home sensor,
12
: Limit in + direction,
13
: Limit in –
direction,
14
: Direction switching
∗
,
15
: Motor-free
∗
) When Pr3E is 1, this function is effective for I/O input for giving priority to
RS485.
71
I
6 function selection
○
0~15
0
72
I
5 Input logic selection
○
0,1
0
0
: Normal logic (Input is effective (ON) when connected to GND.)
1
: Reverse rotation logic (Input is effective (ON) when OPEN (open))
Set the reverse rotation logic to the input desired to be operated on wiring break
side such as forced trip (emergency stop input).
73
I
6 Input logic selection
○
0,1
0
77
Parameter copy
function
No/P.INIT
/P.LOAD/P
.PROG
nO
This function is only available with use of the digital keypad. See page 26.
7A
Monitor mode
switching
0~6
0
You can choose monitor screen to be displayed first when the digital keypad is
connected.
0
: Rotation speed (actual speed),
1
: Torque reference,
2
: Load factor,
3
: Command speed,
4
: Internal DC voltage,
5
: Present position (lower 5 digits),
6
: Present position (rotation number)
Torque reference : A value based on a rated torque of 100. By calculating the
load factor using this, it aims at the minimum motor burnout protection, and the
accuracy can not be guaranteed.
Load factor: Value obtained by applying first-order lag filter to torque reference.
7b
Numerator of
command pulse ratio
○
1~20000
1
You can set the division multiplier ratio of travel
distance. Change of this parameter
does not affect operation speed of motor.
You can set numerator : denominator = 100:1 - 1:100.
7C
Denominator of
command pulse ratio
○
1~20000
1
7F
For manufacturer use
―
―
It cannot be changed.
<Information>
・
Pr6b, 6C, 6d, 6E, 6F, and 7F are read-only parameters. They cannot be changed.
・
Parameters marked with
○
in the column of “effective after power resetting” become
effective when power is turned off once and turned on again after about 10 seconds. They
are not made effective just by changing.