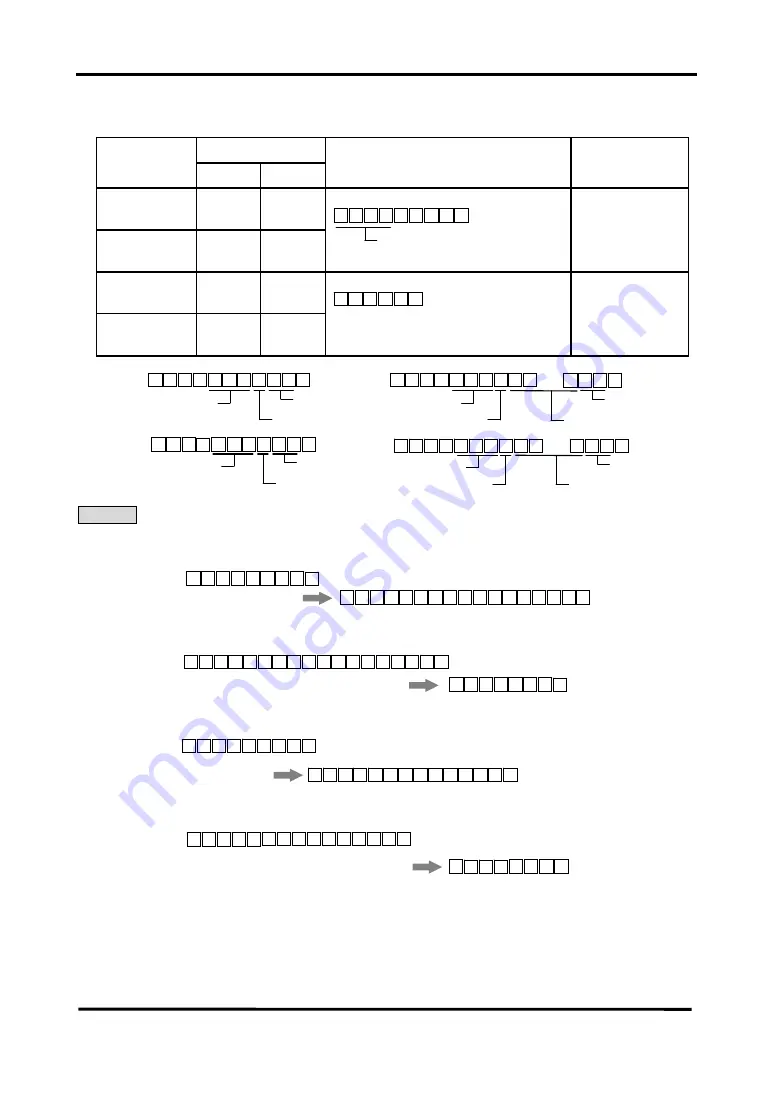
CHAPTER 6 RS-232C CONTROL
6-21
6-3-18 Upper and Lower Limits and Hysteresis
Command Code
Function
Read Set
Setting Code
Setting Value
Range
Upper Limit
Value
RHL WHL
Lower Limit
Value
RLL WLL
±999.9999mm
Upper Limit
Hysteresis
REH WEH
Lower Limit
Hysteresis
REL WEL
0.0000 to
2.0000mm
Example
(1) Read setting content (shown with BCC omitted).
If the add/subtract calculation upper limit is +123.4567mm.
(2) Change the setting (shown with BCC omitted).
Set sensor head 2 lower limit value to -98.7654mm.
(3) Read the setting (shown with BCC omitted).
For an upper limit hysteresis of sensor head 2 of 0.0050mm.
(4) Change the setting (shown with BCC omitted).
Change the lower limit hysteresis of add/subtract calculation to 1.1000mm.
% E E # R H L 1
R
C
% E E $ R H
1 2 3 . 4 5 6 7
L +
R
C
Send
Respond
% E E $ W L L
R
C
% E E # W L
SP
- 9 8 . 7 6
L 2
R
C
5
4
Code + Number (Zero Suppress)
.
.
R
E #
E
%
R
C
E H 2
%
E $
E
R E H
R
C
0
0
.
0 5 0
%
E $
E
W
E L
R
C
#
W
%
E
E
E L
R
C
1
1
.
0 0 0
1
BCC
Select Head
Command Code
E # R
L
% E
CR
Setting Code
Command Code
# W
L
E E
BCC
CR
%
Select Head
…
%
E #
E
R E
R
C
BCC
Select Head
Command Code
%
E #
E
W
E
R
C
…
BCC
Setting Code
Command Code
Select Head
Summary of Contents for HL-C1 Series
Page 7: ...3 Warning Label Laser Emission Indicator Measurement Range Indicator ...
Page 18: ...CHAPTER 1 NAMES AND FUNCTIONS OF PARTS ...
Page 25: ...CHAPTER 1 NAMES AND FUNCTIONS OF PARTS 1 7 MEMO ...
Page 26: ...CHAPTER 2 INSTALLATION ...
Page 32: ...CHAPTER 2 INSTALLATION 2 6 z Measurement of specular reflection 50mm type 85mm type ...
Page 39: ...CHAPTER 2 INSTALLATION 2 13 MEMO ...
Page 40: ...CHAPTER 3 INPUT AND OUTPUT TERMINAL BLOCKS ...
Page 49: ...CHAPTER 3 INPUT AND OUTPUT TERMINAL BLOCKS 3 9 MEMO ...
Page 50: ...CHAPTER 4 MEASUREMENT ...
Page 54: ...CHAPTER 4 MEASUREMENT 4 4 1 2 4 6 3 5 ...
Page 60: ...CHAPTER 5 FUNCTION ITEMS ...
Page 109: ...CHAPTER 5 FUNCTION ITEMS 5 49 MEMO ...
Page 110: ...CHAPTER 6 RS 232C CONTROL ...
Page 149: ...CHAPTER 6 RS 232C CONTROL 6 39 MEMO ...
Page 150: ...CHAPTER 7 INSPECTION AND MAINTENANCE ...
Page 152: ...CHAPTER 8 TROUBLESHOOTING ...
Page 156: ...CHAPTER 9 SPECIFICATIONS ...
Page 162: ...CHAPTER 10 DIMENSIONS ...
Page 164: ...CHAPTER 10 DIMENSIONS 10 2 z 85mm diffused reflection z 85mm specular reflection ...
Page 166: ...CHAPTER 10 DIMENSIONS 10 4 z 85mm diffused reflection z 85mm specular reflection ...
Page 168: ...CHAPTER 10 DIMENSIONS 10 6 10 2 Controller Unit mm 5 5 8 1 4 M3 55 104 120 74 40 Dpth 1 5 ...