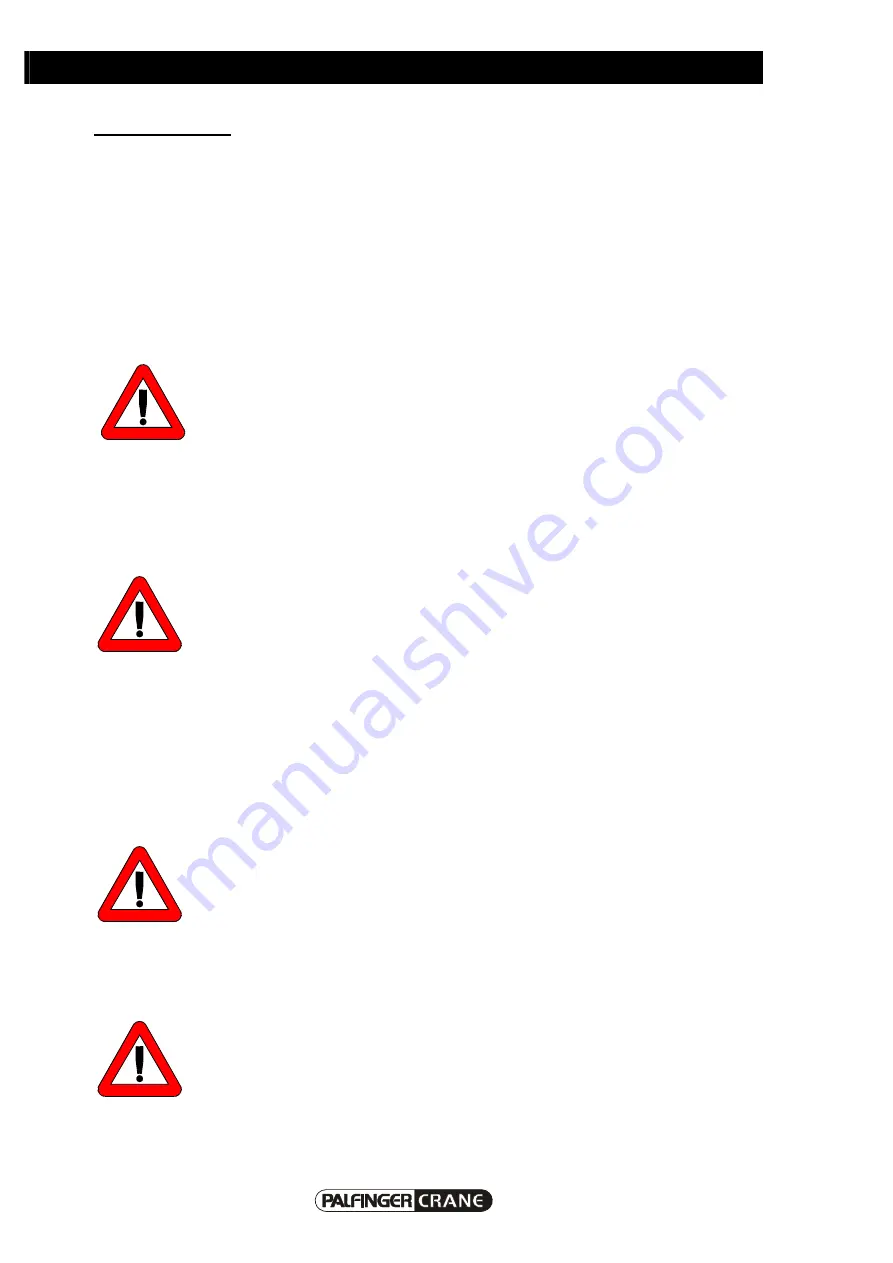
4.1-2
During crane operation
4.1-2 Loading
activity
Only use the crane for lifting loads and never for freeing, hitting, pulling (dragging) loads, pressing or
driving against solid obstacles or for towing vehicles. Any angled hoisting is prohibited.
Further, the country-specific regulations for truck loading crane operation are to be observed.
In a deviation from the set-up as a truck loading crane (e.g. stationary mounting) the load values
change (please consult your service workshop).
During the loading or unloading process the crane operator may not leave the crane operation stand or
put the remote control from the hand.
Only raise loads above the centre of gravity. Secure the load against slipping.
When using the grab always enclose the load completely with the grab.
Handle wet or icy loads with caution, there is danger of them slipping!
If there is so much ice or snow on the load which is to be lifted that
safe lifting cannot be guaranteed, the ice or snow must be removed
from the load before it is lifted.
When you activate a crane function grip the operating lever completely and press it until the crane
responds. You can then increase the speed of the crane function by further slow and even pressing of
the operating lever.
Likewise stop the crane movements slowly and evenly.
Operate the crane so that it performs gentle movements.
Abrupt crane movements, such as quick pressing through or momentary stopping
of a crane function can cause the load to swing and drop. There is danger of an
accident.
Move the raised load so that it does not hit against the crane or other obstacles.
During crane operation the crane operator must not be executing any other jobs.
When the crane operator himself removes the load he has to press the emergency-off switch first (on
the crane control panel, on the remote control).
The emergency-off switch may only be released when the crane operator is out off the danger zone.
Loads must only be attached and removed when the crane is completely at a standstill. Before moving
the load arm ensure that the person who has attached or removed the load is no longer in the danger
area of the crane.
If persons are in the area of the moving load arm (danger area) they
are in acute accident danger.
Do not move the crane at full working speed to the stop, this increases wear and shortens service life.
You can operate several functions at the same time, i.e. carry out several movements at the same
time.
If the crane is operated with several functions at the same time it must
be ensured that if one function is switched off the working speed of
the other functions can increase.
Summary of Contents for PK 23002
Page 1: ......
Page 2: ......
Page 4: ...Inhalt ...
Page 6: ...Inhalt ...
Page 8: ...1 1 1 Overview of dangers ...
Page 16: ...1 3 6 During crane operation ...
Page 18: ...2 1 1 Checks ...
Page 20: ...2 1 1 Checks ...
Page 22: ...3 1 1 An overview of the crane ...
Page 40: ...4 1 1 During crane operation ...
Page 68: ...4 3 6 Additional equipment ...
Page 70: ...5 1 1 Ending crane operation ...
Page 80: ...5 2 1 After crane operation ...
Page 82: ...6 1 1 Maintenance ...
Page 85: ...Maintenance 6 1 3 5 8 11 12 9 4 6 5 7 16 12 4 13 1 2 3 3 W 10 18 17 11 13 15 ...
Page 94: ......