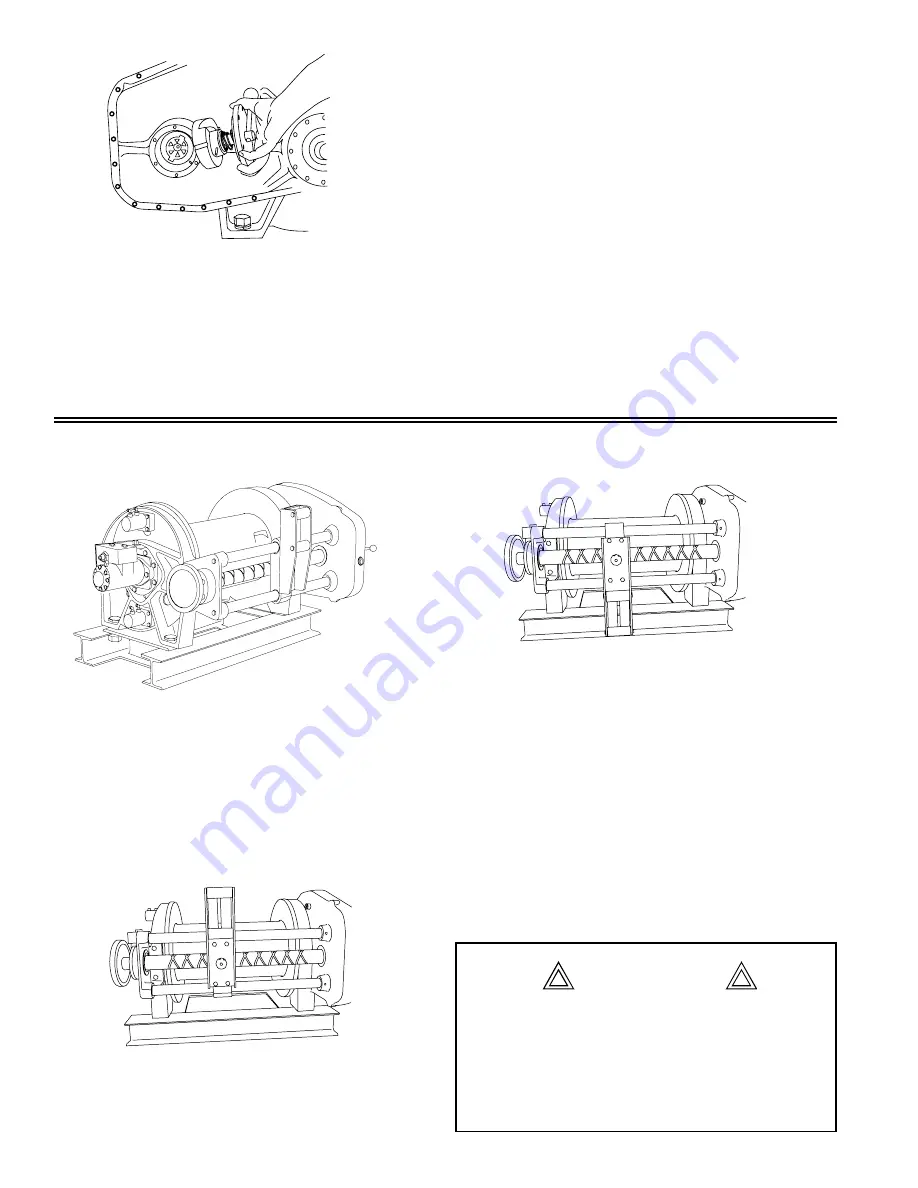
22
CHANGE FROM OVERWIND TO UNDERWIND
The normal method of spooling wire rope onth the winch
drum is “overwind” as shown above. Cable is drawn
through the level wind roller assembly and “over” the top
of the drum.
The following steps outline the procedure to convert the
winch to “underwind”, where the drum rotates in the
opposite direction, and cable is wound onto the drum
from the “under” side.
Remove the four capscrews and lockwashers holding
the roller bracket assembly to the sliding carriage.
Turn the roller assembly over, and re-attach it to the car-
riage with the same capscrews and lockwashers.
Follow the “Wire Rope Installation” instructions on page
6, except you will position the correct anchor pocket on
the bottom of the drum barrel.
Reverse the “A” and “B” hoses on the brake valve block
of the motor. This change will allow the winch controls
to be operated in the same manner as before (haul-in
and pay-out), but the winch drum will rotate in the oppo-
site direction.
Since the BP200 is built with a solid brake hub/coupling,
no other modifications to the winch are required.
If there are any labels, markings, indications, etc. at
the control station, or anywhere else on the vehicle,
which tell the operator what direction the cable drum
or extension shaft rotates in relation to control lever
movement, they may have to be modified according-
ly.
CAUTION
Install the diamond screw disconnect lever assembly
into the cover. Be sure to engage the slot on the out-
side of the cam with the pin in the bore of the cover.
Install the capscrews and lockwashers and torque to the
correct value. Install the freespool switch. The
freespool mechanism and switch can now be tested.
Attach an ohmeter between the terminal on the switch to
the chain case. The meter should read “0”, indicating
an open circuit. If your winch is air controlled, connect
an air source to the freespool pressure port next to the
switch. If your winch is hydraulically contrtolled, connect
a hydraulic hand pump with an accurate gauge to the
pressure port. Apply 90 - 150 psi (621 - 1,030 kPa) of
air, or 150 - 250 psi (1,030 - 1,720 kPa) of hydraulic
pressure. The ohmneter should indicate continuity and
you should be able to rotate the drum by hand.
Maintain pressure for several minutes to be sure piston
seals are not leaking. If there are any signs indicating
pressure is leaking past the seals, disassemble the pis-
ton and correct the cause of the leak before returning
the winch to service. Slowly rotate the drum while
releasing pressure to re-engage the gear train.
Install the drain plug and fill the chain case with oil to
the middle of the sight glass. Install the bushing and
vent plug.
Summary of Contents for Braden BP200
Page 46: ......