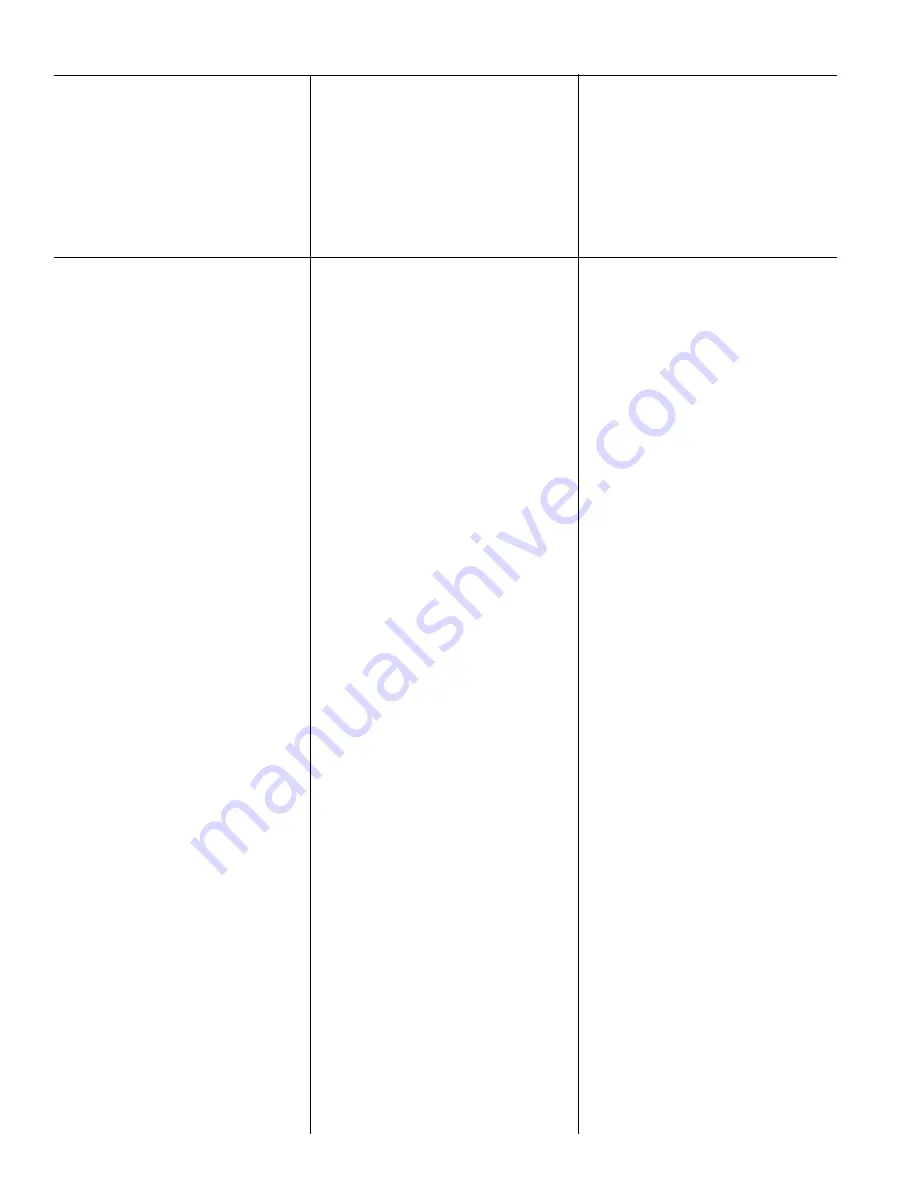
16
TROUBLE
REMEDY
PROBABLE CAUSE
The same as B2.
Same as A2.
1.
Excessive system back pres-
sure acting on the brake release
port.
2.
Friction brake will not hold due
to worn or damaged brake
discs.
The brake will not hold a load with
the control lever in neutral.
C
Reinforce mounting surface.
If necessary, use shim stock to
level winch. Refer to “Winch
Installation”.
First loosen, then evenly retight-
en all winch mounting bolts to
recommended torque.
Check relief pressure as fol-
lows:
A. Install an accurate 0-4000 psi
gauge into the inlet port of the
brake valve.
1.
The winch may be mounted on
an uneven or flexible surface
which causes distortion of the
winch base and binding of the
gear train. Binding in the gear
train will absorb horsepower
needed to pull the rated load
and cause heat.
2.
System relief valve may be set
too low. Relief valve needs
adjustment or repair.
The winch will not pull the rated load
D
B.
Apply a stall pull load on the
winch while monitoring pres-
sure.
C. Compare gauge reading to
winch specifications. Adjust
relief valve as required.
NOTE: If pressure does not increase
in proportion to adjustment,
relief valve or pump may be
contaminated or worn out. In
either case, the relief valve may
require disassembly or replace-
ment.
Same as remedies for Trouble
D1 & D2.
Same as remedies for Trouble
E2.
Refer to winch performance
charts for additional information.
Perform rigging service as rec-
ommended by vehicle manufac-
turer.
3.
Be certain hydraulic system
temperature is not more than
180oF (82oC). Excessive
hydraulic oil temperatures
increase motor internal leakage
and reduce motor performance.
4.
Winch line pull rating is based
on 1st layer of wire rope.
5.
Rigging and sheaves not oper-
ating efficiently.
Summary of Contents for Braden BP200
Page 46: ......