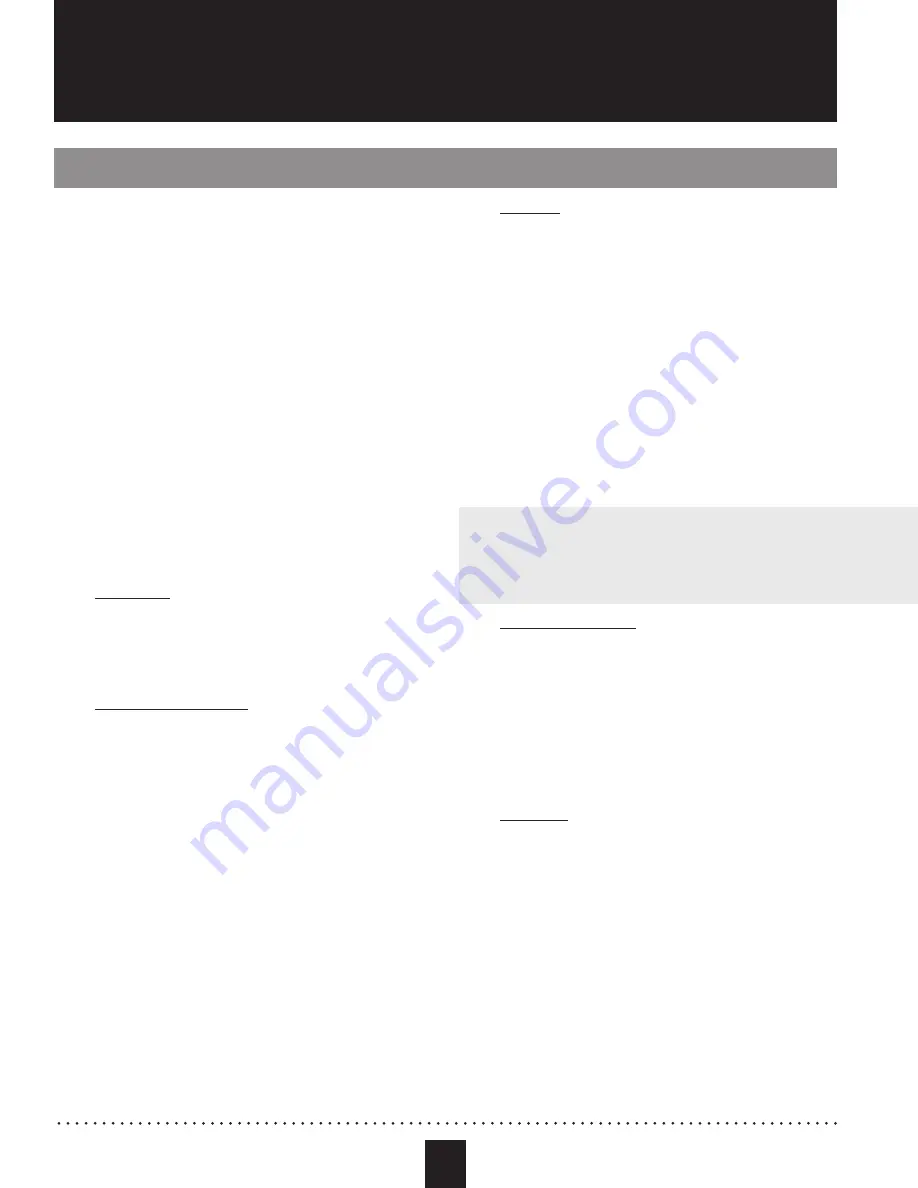
20
AIM-OM-ATX-3, Rev. 2.1, 05/15
• Copyright Orenco Systems
®
, Inc. Property of Orenco Systems
®
, Inc. Do not reproduce or distribute without written authorization from Orenco: 800-348-9843.
AdvanTex
®
O
&
M
MANUAL
C O M M E R C I A L T R E A T M E N T S Y S T E M S
Maintenance (continued)
Corrective Maintenance
An alarm is triggered when the liquid in the tank reaches a level that
is either higher or lower than it should be, under normal operating
conditions.
When responding to an alarm, first discern the type of alarm being
activated. If it is due to pump failure, test each pump manually and locate
the failed pump. To replace the pump, see the “Removing & Replacing
Inoperative Pumps” section of this document. Remove the access riser lid
and visually inspect the liquid level. If a high liquid level or low liquid level
has caused the alarm, follow the appropriate procedures below.
High Liquid Level Alarm
1. Determine if the high water alarm is from higher than expected
usage (i.e., special event, etc.). If there is a long-term increase in
flows, then timer settings need to be adjusted accordingly.
2. When a high liquid level condition exists, the source of the problem is
likely to be one of the following:
a. Poor valve seal – Consult the design plans for proper operating
level and visually inspect the recirculating valve to verify the liquid
level in the tank is within the normal range. If the liquid level is
high, the valve may require cleaning because it is not making a
tight seal when seated. Remove, disassemble, and inspect.
b. Control panel breakers tripped – Check the circuit breakers,
switches, and fuses in the system control panel. If separate
breakers in the main panel were used for the pumps and controls,
also check these breakers. If a breaker is found to be tripped,
reset the breaker. If the breaker trips immediately, check the
wiring for a short or bad breaker. If the breaker or breakers don’t
trip again, then the problem has probably been found or has
corrected itself. Test the automatic function of the system as
shown in the “Start-up & Operation” section of this manual to
verify proper operation.
c. Faulty floats – If, after checking the circuit breakers, fuses, and
switches, the pump still does not operate, toggle the “AUTO-
OFF-MAN” switch to “MAN.” If the pump engages, the problem
is likely to be in the float system. (If the motor contactor engages
but the pump doesn’t run, go to step g, “Water in splice box or
loose wires.”) Pump the tank down to a level below the “Override
Timer On/Off” float. Cycle the pump to simulate the timer on
and off periods so the effluent is dosed to different zones of
the AdvanTex
®
system. Toggle the “AUTO-OFF-MAN” switch to
“AUTO.” Do not leave a pump in the “MAN” position unattended. If
you do, the pump can continue to operate without liquid, possibly
drawing solids into the filter and causing potential failures. Isolate
the float switches and check to ensure all floats are operating
properly. If a float is found to be faulty, refer to the “Removing &
Replacing Inoperative Floats” section in this document.
IMPORTANT!
Before doing any work on either the wiring to
the level control floats and pump or inside the pump control
panel, switch off the power to the system at the service
entrance panel and set the circuit breakers in the panel to
their “OFF” positions.
d. Pump clogged or not clean – Check the pump for discharge
flow. Close the ball valve, disconnect the union in the discharge
plumbing assembly and turn the union so it is facing down.
Engage the pump and visually inspect the approximate flow
rate being discharged. If you are unsure of the discharge rate,
measure the time it takes to fill a five-gallon bucket with the
discharge. Check this value against the appropriate pump curve.
If the flow rate is insufficient, the pump may need to be cleaned.
Refer to the
Pump Repair Manual
provided in Appendix D.
e. Valves closed – If the pump operates in the proper flow range,
check all downstream valves to ensure that they are in the open
position. If the valves are all open, test the discharge pressure of
the pump. For proper pump testing methods, refer to the
Pump
Repair Manual
provided in Appendix D.