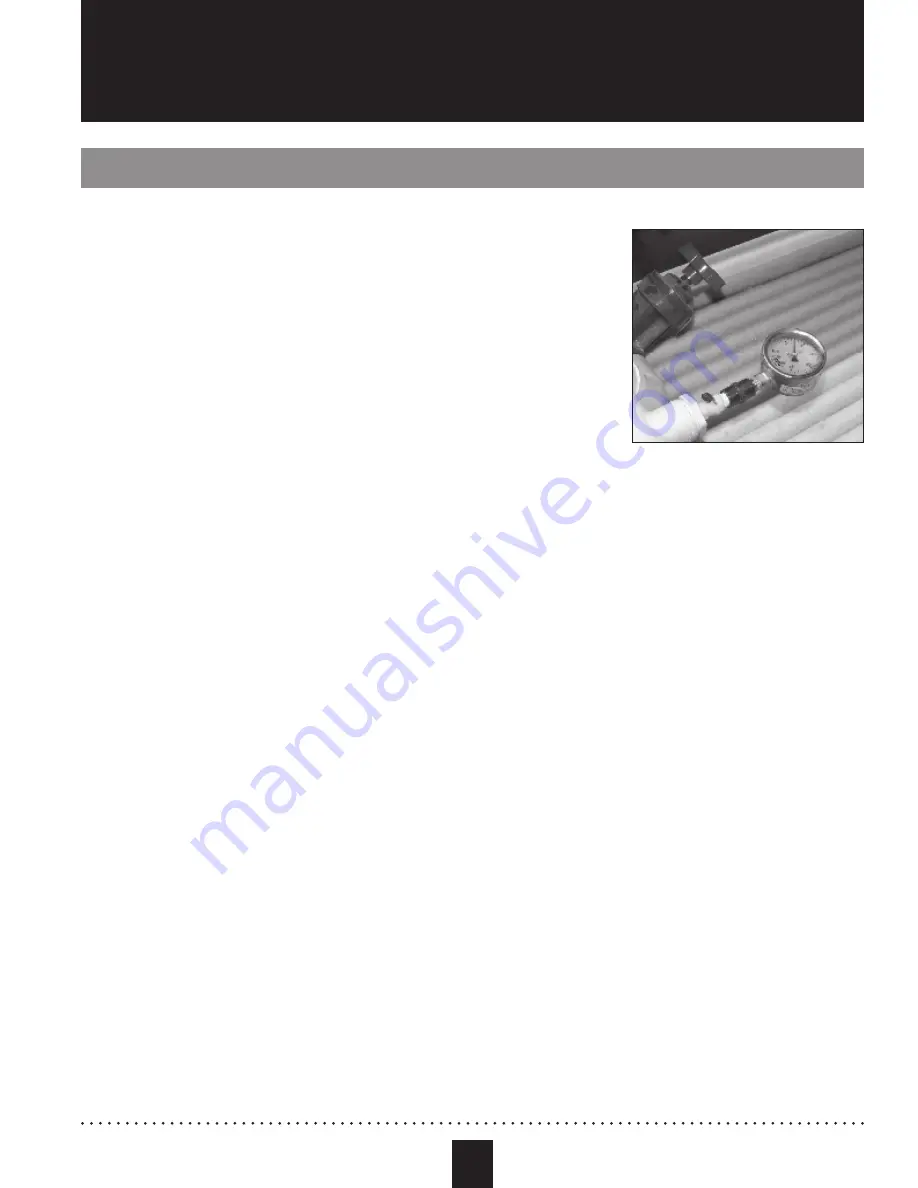
17
Copyright Orenco Systems
®
, Inc. Property of Orenco Systems
®
, Inc. Do not reproduce or distribute without written authorization from Orenco: 800-348-9843. •
AIM-OM-ATX-3, Rev. 2.1, 05/15
AdvanTex
®
O
&
M
MANUAL
C O M M E R C I A L T R E A T M E N T S Y S T E M S
Maintenance (continued)
Quarterly Maintenance
Testing for Biochemical Oxygen Demand (BOD
5
); Total Suspended Solids
(TSS); Fats, Oils, and Grease (FOG); Ammonia (NH
3
); Nitrate (NO
3
); and
pH should be done according to regulatory requirements. If testing is
not required by the regulatory jurisdiction, samples should be taken
quarterly for the first year to establish a baseline. Subsequent testing
after the first year may be reduced based on the establishment of this
baseline. Regular samples will provide valuable information for ongoing
maintenance and troubleshooting. Effluent testing procedures may be
found in the residential
AdvanTex
O&M Manual
in Appendix B. All results
obtained should be reported to the appropriate people, including Orenco’s
Engineered Systems Department.
For the first year only, check voltages and amperages of all pumps and
record them on the
Field Maintenance Report Form
provided in Appendix
B. Refer to the start-up voltages and amperages recorded in the “Start-
up & Operation” section of this document. If the voltage drop or the
amperage exceeds National Electric Code (NEC) requirements (see chart
provided in “Inspection Points —Pumps” section of this document), have
an electrician verify the service line and check the pump windings. If there
is no discernible difference in voltage or amperage, this procedure may be
performed annually.
Semi-Annual Maintenance
Inspect the spray of the
nozzles in the AdvanTex
pods. Look for reduced
or uneven spray patterns
as well as clogged spray
nozzles or biological
growth on the spray
nozzles. Observe and
measure the residual
pressure. Refer back to
the Start-up & Operation
section for initial
measurements of residual pressure. If the observed residual pressure
exceeds the initial residual pressure (3 psi) more than 15-20%, it can be
assumed that some of the nozzles are plugged and the laterals require
flushing. To flush the laterals, open the ball valves at the end of one lateral.
At the control panel, toggle the “AUTO-OFF-MAN” switch to “MAN” and let
the pump run to flush any material from the lateral. Repeat for each lateral
until all of the laterals have been flushed. Recheck the residual pressure
to ensure the laterals have been sufficiently cleared.
If there is still a significant difference in initial and current residual
pressure, use an Orenco AX lateral cleaning brush or a high-pressure
washer to clean the laterals.
To clean out the spray nozzles, turning the laterals so the spray nozzle
turbines are pointed up and then hosing each turbine off. For excessive
buildup in the spray nozzles, remove the nozzles and replace them with
clean nozzles. Soak the plugged nozzle in TSP or any other approved
cleaning agent for 30 minutes. When a spray nozzle is clear, you can
see the spray nozzle turbine spin freely and the spray distribute evenly
across the textile media. If the nozzles are substantially plugged after six
months, then it may be prudent to inspect the residual pressure every
three months and adjust scheduled testing and flushing of the laterals
accordingly.
Visually inspect the recirculating valve and verify that the liquid level in
the tank is within the normal range. Consult the design plans for proper
operating level. If the liquid level is low, the ball mechanism could be
jammed in the seated position. Remove, disassemble, and inspect. If the
liquid level is high, the valve may require cleaning because it is not making
a tight seal when seated. Remove, disassemble, and inspect.