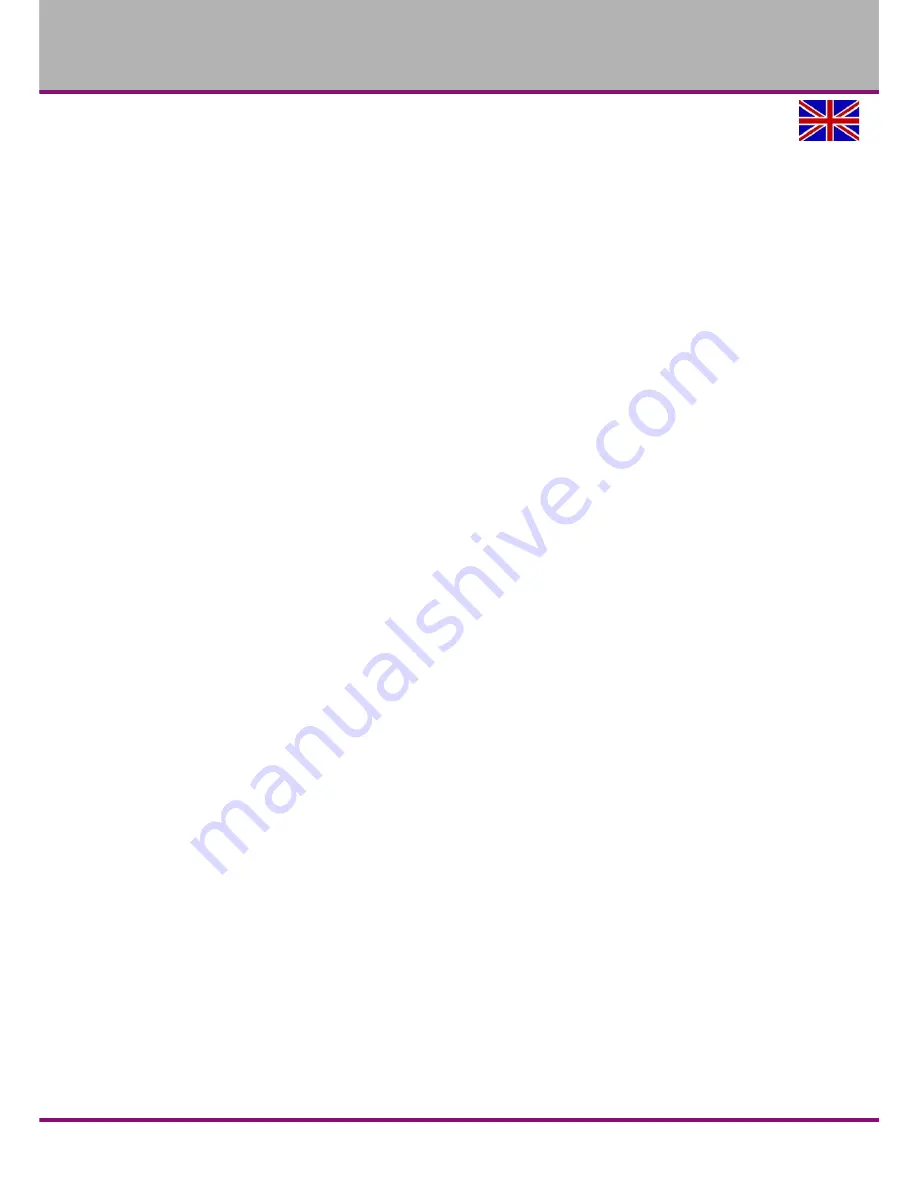
OPTIMUM
M A S C H I N E N - G E R M A N Y
Appendix
Version 1.0.1 dated 2015-05-27
Page 108
Original operating instructions
TU3008 | TU3008V
GB
8.3
Liability claims for defects / warranty
Beside the legal liability claims for defects of the customer towards the seller, the manufacturer
of the product, OPTIMUM GmbH, Robert-Pfleger-Straße 26, D-96103 Hallstadt, does not grant
any further warranties unless they are listed below or were promised in the framework of a sin-
gle contractual provision.
The processing of the liability claims or of the warranty is performed as chosen by
OPTIMUM GmbH either directly or through one of its dealers.
Any defective products or components of such products will either be repaired or
replaced by components which are free from defects. Ownership of replaced products
or components is transferred to OPTIMUM Maschinen Germany GmbH.
The automatically generated original proof of purchase which shows the date of purchase,
the type of machine and the serial number, if applicable, is the precondition in order to
assert liability or warranty claims. If the original proof of purchase is not presented, we are
not able to perform any services.
Defects resulting from the following circumstances are excluded from liability and warranty
claims:
- Using the product beyond the technical options and proper use, in particular due to over-
straining of the machine.
- Any defects arising by one's own fault due to faulty operations or if the operating manual
is disregarded.
- Inattentive or incorrect handling and use of improper equipment
- Unauthorized modifications and repairs
- Insufficient installation and safeguarding of the machine
- Disregarding the installation requirements and conditions of use
- atmospheric discharges, overvoltage and lightning strokes as well as chemical influences
The following items are also not subject to liability or warranty claims:
- Wearing parts and components which are subject to a standard wear as intended such
as e.g. V-belts, ball bearings, illuminants, filters, sealings, etc.
- Non reproducible software errors
Any services, which OPTIMUM GmbH or one of its agents performs in order to fulfil any
additional warranty are neither an acceptance of the defects nor an acceptance of its obli-
gation to compensate. Such services do neither delay nor interrupt the warranty period.
Place of jurisdiction for legal disputes between businessmen is Bamberg.
If one of the aforementioned agreements is totally or partially inoperative and/or invalid, a
provision closest to the intent of the warrantor is considered agreed upon, which remains
within the framework of the limits of liability and warranty which are specified by this con-
tract.