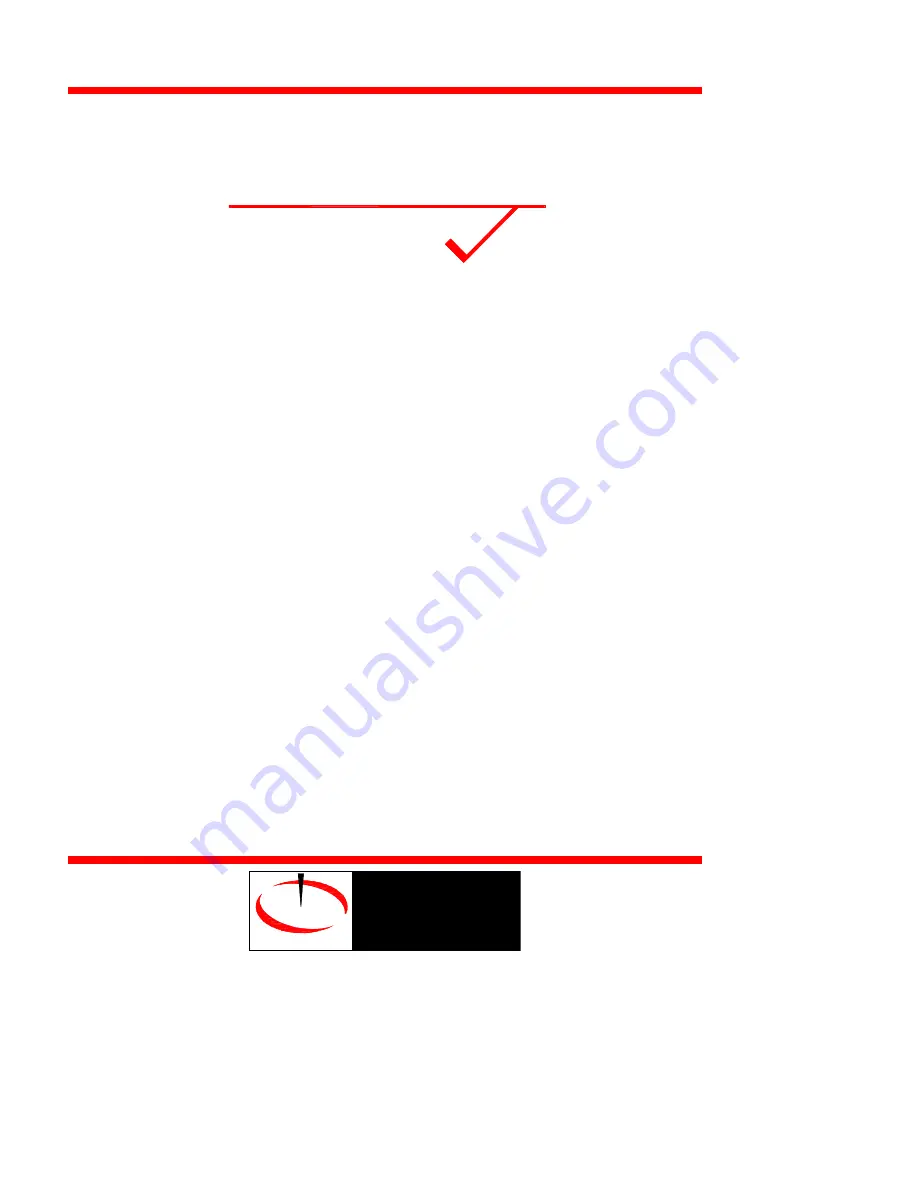
5872C Manual Version 5_4
LASER
CHECK
Surface Roughness
Measurement Gages
O P T I C A L D I M E N S I O N S
LLC
®
1 3 7 E a s t A l t o n , S u i t e B
S a n t a A n a , C A 9 2 7 0 7
P H O N E : 7 1 4 - 6 6 8 - 9 1 1 5
F A X : 7 1 4 - 6 6 8 - 9 1 1 9
i n f o @ o p t i c a l d i m e n s i o n s . c o m
w w w . o p t i c a l d i m e n s i o n s . c o m
®