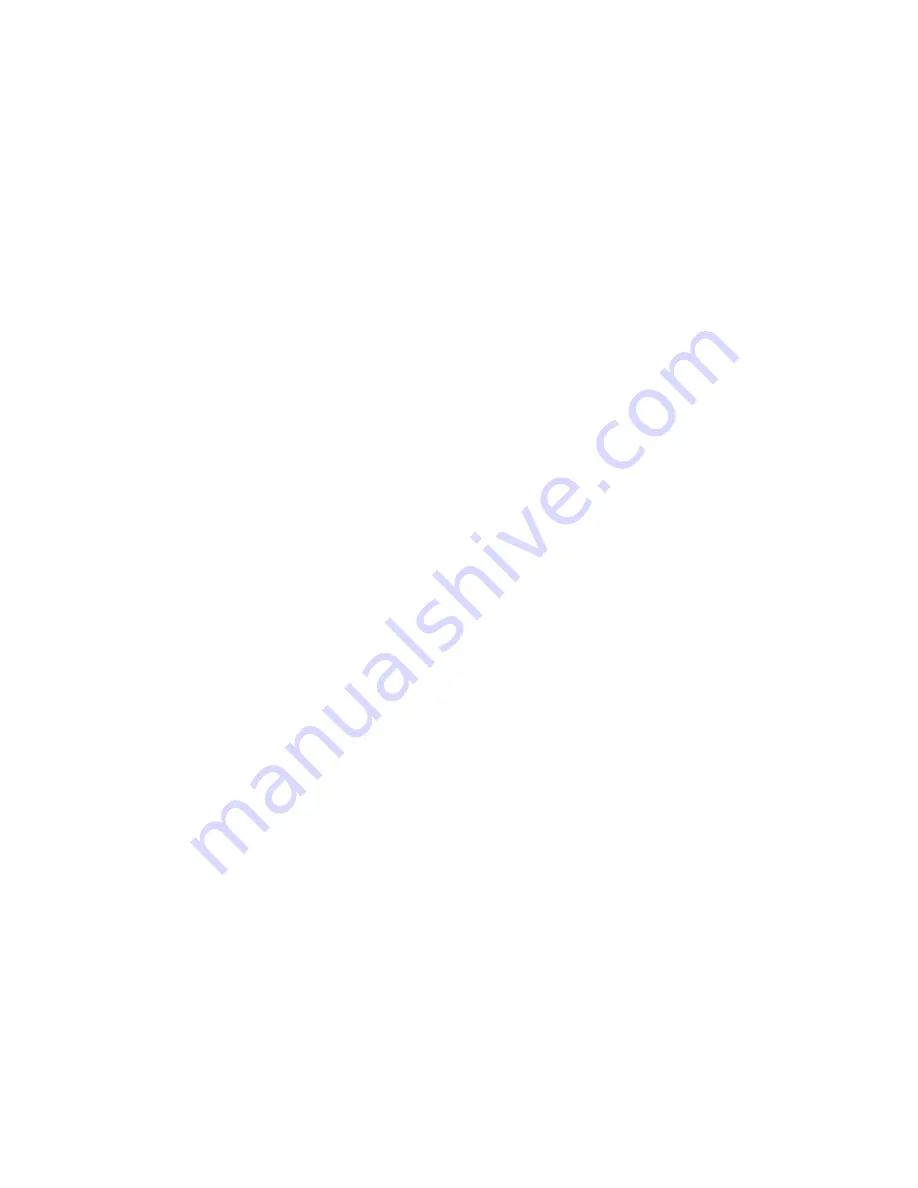
27
You should also note that the maximum reading observed on SUM will typically be lower on rough or non-
metallic surfaces than on smooth and metallic surfaces because less light is reflected and scattered into our
detectors on rough or non-metallic surfaces.
Verifying Alignment Procedures
Set Head Close Correct Position
Horizontal and vertical alignment should be close before performing any alignment with Measure/Headtest
or Lasercheck Windows software. If Lasercheck is badly misaligned, than the software cannot locate the
specular laser beam for vertical alignment and has little or no signal for horizontal alignment.
Align Horizontally
Horizontal alignment works best on a clean, rough surface (greater than 10 microinches) with a dominant
roughness direction, for example a ground surface. With an alignment aid, Measure/Headtest or
Measure/Align, set the horizontal alignment as close to optimal as possible. This is done by maximizing the
value of SUM displayed on Measure/Headtest software or by maximizing the horizontal alignment percent
within Measure/Align.
Align Vertically
Vertical alignment works best on a smooth surface. Move the head up or down over a smooth area (or a
rough area coated with a film of oil). Use Measure/Headtest to position the specular beam on # 6.
Verify Alignment
Check visually and with software that horizontal alignment has not changed during the process of
performing vertical alignment.
As surfaces get rougher (greater than 20 microinches), resolution of Lasercheck decreases and sensitivity to
misalignment increases. Mounting and alignment stability becomes more important to maintaining high
repeatability from Lasercheck. The important issue to appreciate is that on smoother surfaces, Lasercheck
has more tolerance to misalignment, shaking, vibrating, etc. On rougher surfaces, Lasercheck does not have
as much tolerance for misalignment, shaking, or vibrating.