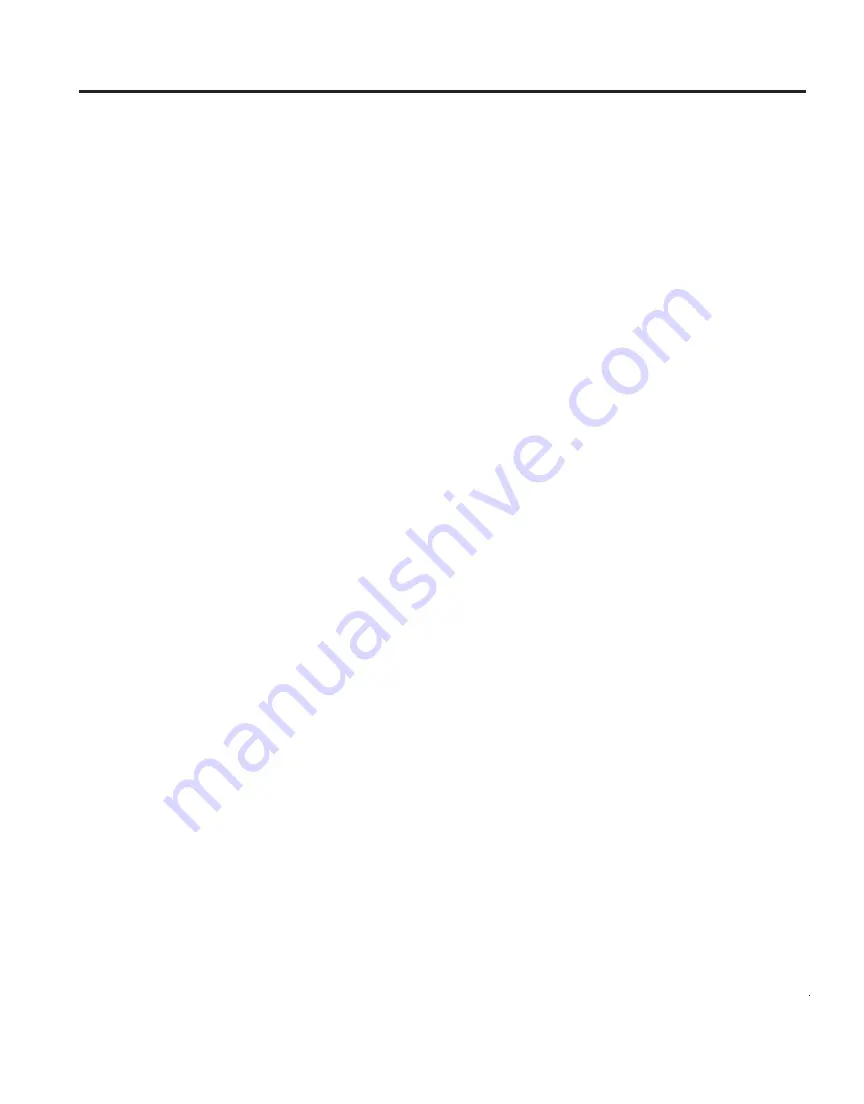
55
APPENDIX A
Autotuning
By autotuning, the controller selects what it calculates to be the optimal
PID control parameters for a particular process and then stores them in
EEPROM memory for future use. The PID parameters are stored so that
when the controller is powered up after being shut down, the controller
does not need to be autotuned again. The same autotuned PID parame-
ters are used until the Autotune function is again initiated. The Autotune
parameters are only good for the process the Autotune function was
used on. If the setpoint is significantly changed, the input sensor is
changed, the load or output device is changed or relocated, or any
other disturbances occur which might change the dynamics of the sys-
tem, the Autotune function should be performed again. The autotuned
control parameters are not always perfect for every application but
almost always give the operator a good starting point from which fur-
ther refinement of the control parameters can be performed manually.
The controller’s autotuning algorithm is particularly suited for tempera-
ture control applications and may not always autotune effectively for
other processes. Here are cases where the Autotune function does not
perform well or does not perform at all:
1. The system is affected by process disturbances external to the con-
trol loop. Adjacent heater zones, changing material levels, exother-
mic reactions are examples of process disturbances which are
external to the control loop. The controller would never be able to
autotune such an unstable process.
2. The system is very dynamic. The process variable changes very
quickly. Certain pressure and flow applications would be character-