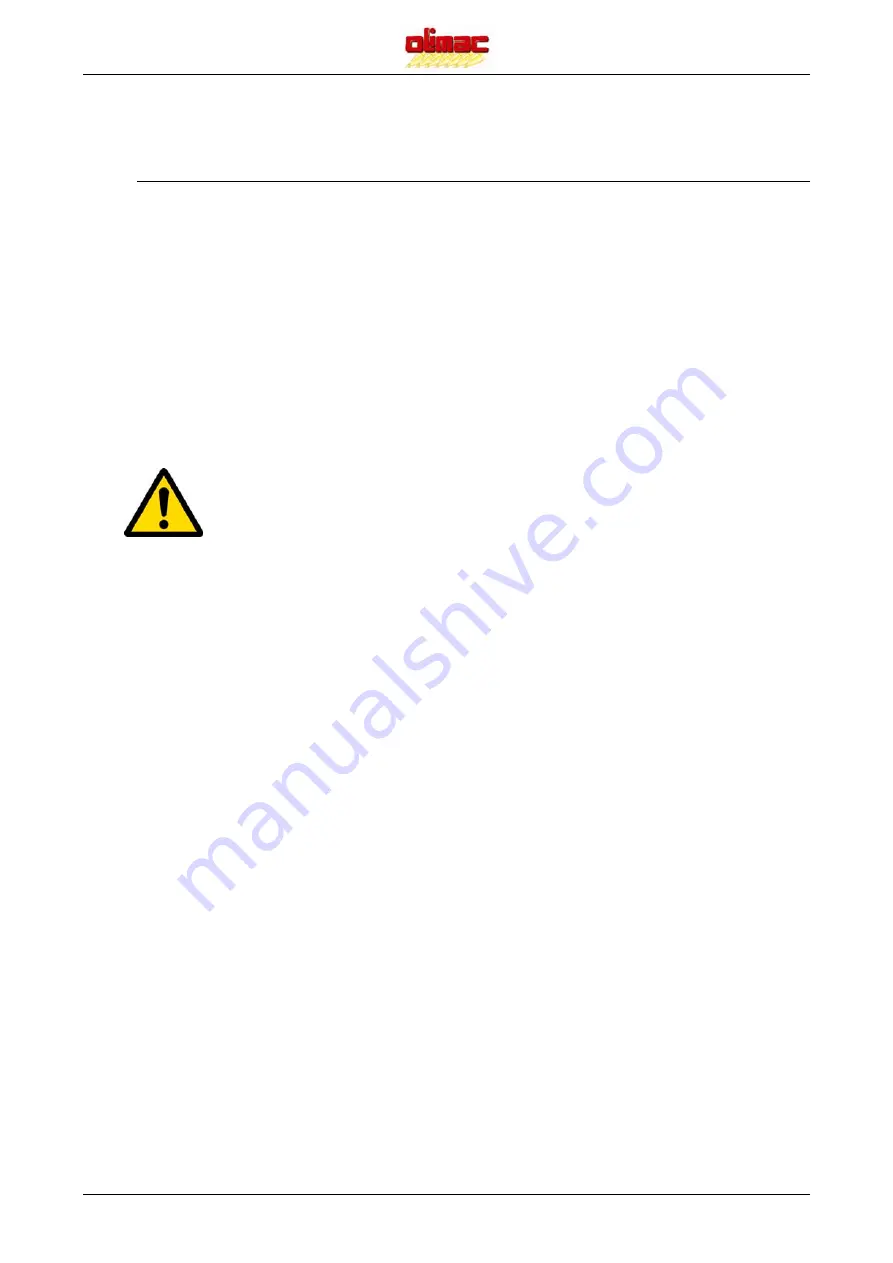
User
and
maintenance
manual
DRAGO
Rev.
01
Original
instructions
Page
8
/
53
3.
IMPROPER
USE
The
machine
must
never
be
used:
‐
for
purposes
other
than
those
outlined
in
chapter
2;
‐
in
potentially
explosive
and
aggressive
environments,
or
where
concentrations
of
dust
or
oily
substances
suspended
in
the
air
are
high;
‐
by
untrained
and
uninformed
personnel;
‐
when
safety
devices
are
unavailable,
have
been
removed
or
tampered
with;
‐
with
any
electrical
jumper
and/or
other
means
that
exclude
utilities/parts
of
the
machine;
‐
for
operations
other
than
those
specified
in
this
manual.
Failure
to
comply
with
the
instructions
provided
in
this
manual
could
result
in
damage
to
property
and/or
injury.