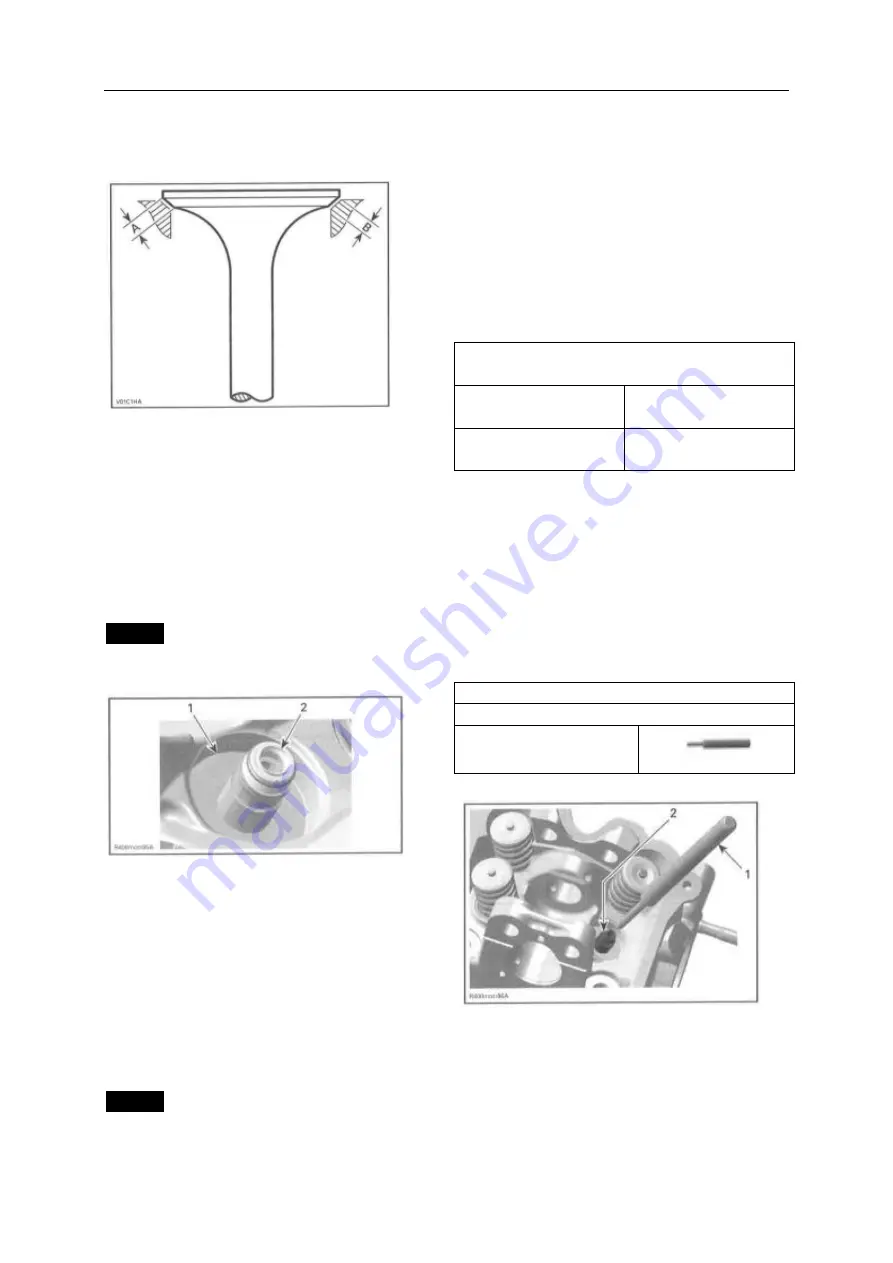
3. ENGINE
3-
56
If valve seat contact width is too wide or has dark
spots, replace the cylinder head.
A. Valve face contact width
B. Valve seat contact width
Valve Installation
For installation, reverse the removal procedure.
Pay attention to the following details.
Install a NEW valve stem seal. Make sure thrust
washer is installed before installing seal.
Apply engine oil on valve stem and insta1l it.
NOTICE Be careful when valve stem is passed
through sealing lips of valve stem
sea1.
1. Thrust washer
2. Sealing lips of valve stem seal
To ease installation of cotters, apply oil or grease
on them so that they remain in place while
releasing the spring.
After spring is installed, ensure it is properly
locked by tapping on valve stem end with a soft
hammer so that valve opens and c1oses a few
times.
NOTICE An improperly locked valve spring wi1l
cause engine damage.
VALVE GUIDES
Valve Guide Inspection
Always replace valve stem seals whenever valve
guides are removed.
Measure valve guide in three places using a small
bore gauge.
NOTE: Clean valve guide to remove carbon
deposits before measuring.
Replace valve guide if it is out of specification or
has other damages such as wear or friction surface.
VALVE GUIDE DIAMETER
(INTAKE AND EXHAUST VALVES
NEW
4.998mm to5.018mm
(.1968in to.1976in)
SERVICE LIMIT
SERVICE LIMIT
5.050 mm(.1988 in)
Valve Guide Removal
Refer to following procedures in this subsection to
remove:
- Cylinder head
- Valves.
NOTE: Clean valve guide area from contamination
before removal.
Drive the valve guide out of cylinder head.
REQUIED TOOL
Hammer
VALVE GUIDE
REMOVER 5 MM
1. Valve guide remover
2. Valve guide
Valve Guide Installation
For installation, reverse the removal procedure.
Pay attention to the following details.
Summary of Contents for UTV Desertcross 1000cc-3
Page 30: ......
Page 40: ...3 ENGINE 3 10 COOLING SYSTEM RADIATOR 1000R Engine...
Page 41: ...3 ENGINE 3 11 WATER PUMP 1000R Engine...
Page 58: ...3 ENGINE 3 28 MAGNETO SYSTEM...
Page 66: ...3 ENGINE 3 36 INTAKE MANIFOLD...
Page 69: ...3 ENGINE 3 39 TOP END CYLINDER HEAD NO 1...
Page 70: ...3 ENGINE 3 40 CYLINDER HEAD NO 2...
Page 71: ...3 ENGINE 3 41 CYLINDER AND PISTONS...
Page 95: ...3 ENGINE 3 65 TIMING CHAIN...
Page 105: ...3 ENGINE 3 75 BOTTOM END ENGINE DRIVE SHAFT...
Page 106: ...3 ENGINE 3 76 CRANKCASE AND PTO COVER...
Page 107: ...3 ENGINE 3 77 CRANKSHAFT...
Page 132: ...3 ENGINE 3 102 GEARBOX AND4X4 COUPLING UNIT GEARBOX COMPONENTS AND 4 4 COUPING MECHANISISM...
Page 133: ......
Page 152: ......
Page 158: ...4 COOLING SYSTEM 4 6...
Page 168: ......
Page 182: ......
Page 183: ...7 STEERING SYSTEM 7 1 7 STEERING SYSTEM ADJUSTMENT 7 2 TROUBLESHOOTING 7 3...
Page 186: ......
Page 188: ......
Page 200: ......
Page 216: ......