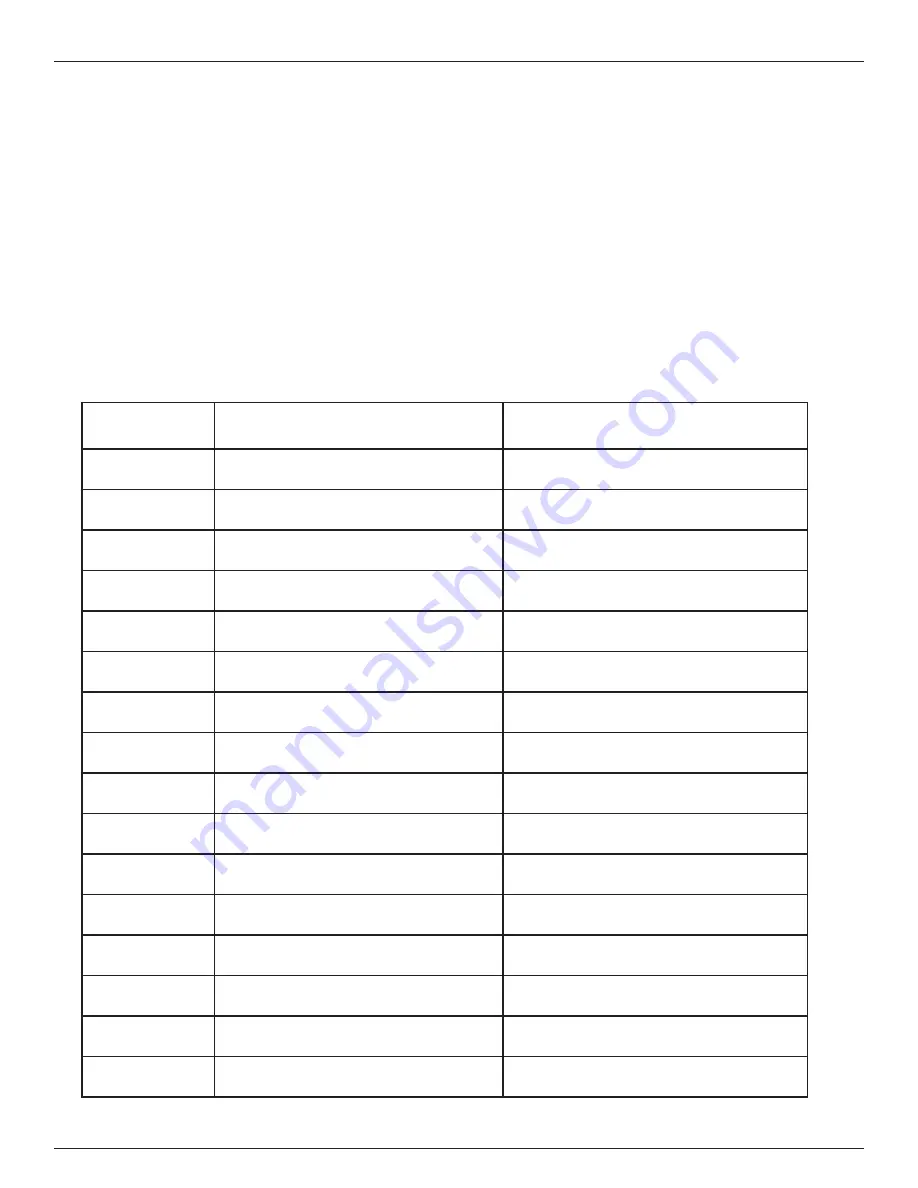
8 - FORMS AND DECLARATIONS
8-1
8 - FORMS AND DECLARATIONS
Norwood Sales Inc. follows the general Safety Standards specified by the American Society of Agricultural and Biological
Engineers (ASABE
®
), and the Occupational Safety and Health Administration (OSHA
®
). Anyone who will be operating and/
or maintaining the equipment must read and clearly understand all Safety, Operating and Maintenance information presented
in this manual.
Do not operate, or allow anyone else to operate, this equipment until this document has been read. Review this information
annually, before the season start-up.
Make periodic reviews of SAFETY and OPERATION a standard practice for all of your equipment.
The following Sign-Off Form is provided for your record keeping. Use it to show that all personnel who will be working with
the equipment have read and understand the provided information. Also, they have been instructed in the operation of the
equipment. Copy this page to continue the record.
SIGN - OFF FORM
DATE
EMPLOYEES SIGNATURE EMPLOYERS SIGNATURE
Summary of Contents for The Grain Handler 10
Page 12: ...1 6 1 GENERAL INFORMATION This Page Is Intentionally Left Blank...
Page 40: ...2 SAFETY INFORMATION 2 28 This Page Is Intentionally Left Blank...
Page 90: ...4 WORKING OPERATIONS 4 12 This Page Is Intentionally Left Blank...
Page 108: ...5 MAINTENANCE 5 18 This Page Is Intentionally Left Blank...
Page 112: ...6 TROUBLESHOOTING 6 4 This Page Is Intentionally Left Blank...
Page 120: ...8 FORMS AND DECLARATIONS 8 2 This Page Is Intentionally Left Blank...
Page 128: ...i 6 www norwoodsales com 1 800 446 0316...
Page 129: ......