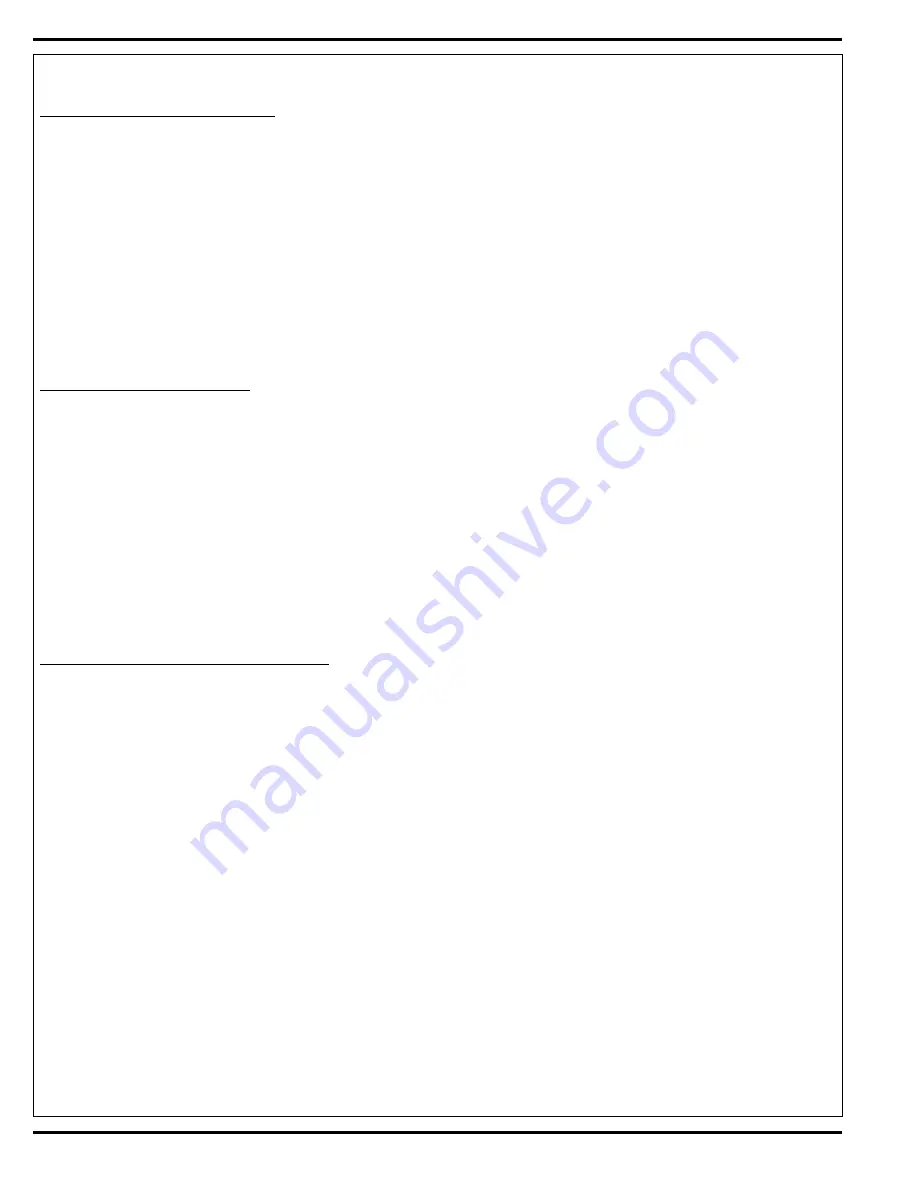
58
- FORM NO. 56043126 - CR 1100, CR 1200
PROGRAMMABLE CONTROL OPTIONS
Scrub Motor Turn-Off Delay Adjustment:
FACTORY DEFAULT: 1 (0.5 second)
RANGE: 1 - 9 (0.5 – 4.5 seconds)
The amount of time that the scrub brushes continue to run after the foot pedal returns to neutral is adjustable. To select the desired delay:
1
Turn
the
main power key switch
to the
off
position.
2
Press and hold the
scrub system off switch
.
3
While holding the scrub system off switch turn the
main power key switch
to the
on
position.
4
Continue to hold the scrub system off switch until all indicators except the scrub off indicator turn off (approximately two seconds).
5
Release the scrub off switch.
6
The status display will now show a number from 1 to 9. Pressing and releasing the
scrub off switch
will increase the displayed value until 9 is
reached. The next press will return to 1. Each increment represents 0.5 second with 1 equal to 0.5 second.
7
To save the new setting, turn the
main power key switch
to the
off
position.
8
The new setting will be saved and will remain in effect until it is changed again.
Vacuum Turn-Off Delay Adjustment:
FACTORY DEFAULT: 1 (12 seconds)
RANGE: 1 - 9 (12 – 20 seconds)
The amount of time that the vacuum continues to run after the foot pedal returns to neutral is adjustable. To select the desired delay:
1
Turn
the
main power key switch
to the
off
position.
2
Press and hold the
vacuum/squeegee switch
.
3
While holding the vacuum/squeegee switch turn the
main power key switch
to the
on
position.
4
Continue to hold the vacuum/squeegee switch until all indicators except the vacuum/squeegee indicator turn off (approximately two seconds).
5
Release the vacuum/squeegee switch.
6
The status display will now show a number from 1 to 9. Pressing and releasing the
vacuum/squeegee switch
will increase the displayed value
until 9 is reached. The next press will return to 1. Each increment represents one second with 1 equal to twelve seconds.
7
To save the new setting, turn the
main power key switch
to the
off
position.
8
The new setting will be saved and will remain in effect until it is changed again.
Main and Side Broom Turn-Off Delay Adjustment:
FACTORY DEFAULT: 3 (5 seconds)
RANGE: 1 - 9 (3 – 11 seconds)
The amount of time that the main broom and side brooms continue to run after the foot pedal returns to neutral is adjustable. To select the desired
delay:
1
Turn
the
main power key switch
to the
off
position.
2
Press and hold the
side broom up/off switch
.
3
While holding the side broom up/off switch turn the
main power key switch
to the
on
position.
4
Continue to hold the side broom up/off switch until all indicators except the side broom up/off indicator turn off (approximately two seconds).
5
Release the side broom up/off switch.
6
The status display will now show a number from 1 to 9. Pressing and releasing the
side broom up/off switch
will increase the displayed value
until 9 is reached. The next press will return to 1. Each increment represents one second with 1 equal to three seconds.
7
To save the new setting, turn the
main power key switch
to the
off
position.
8
The new setting will be saved and will remain in effect until it is changed again.
Summary of Contents for Cr 1100
Page 72: ......