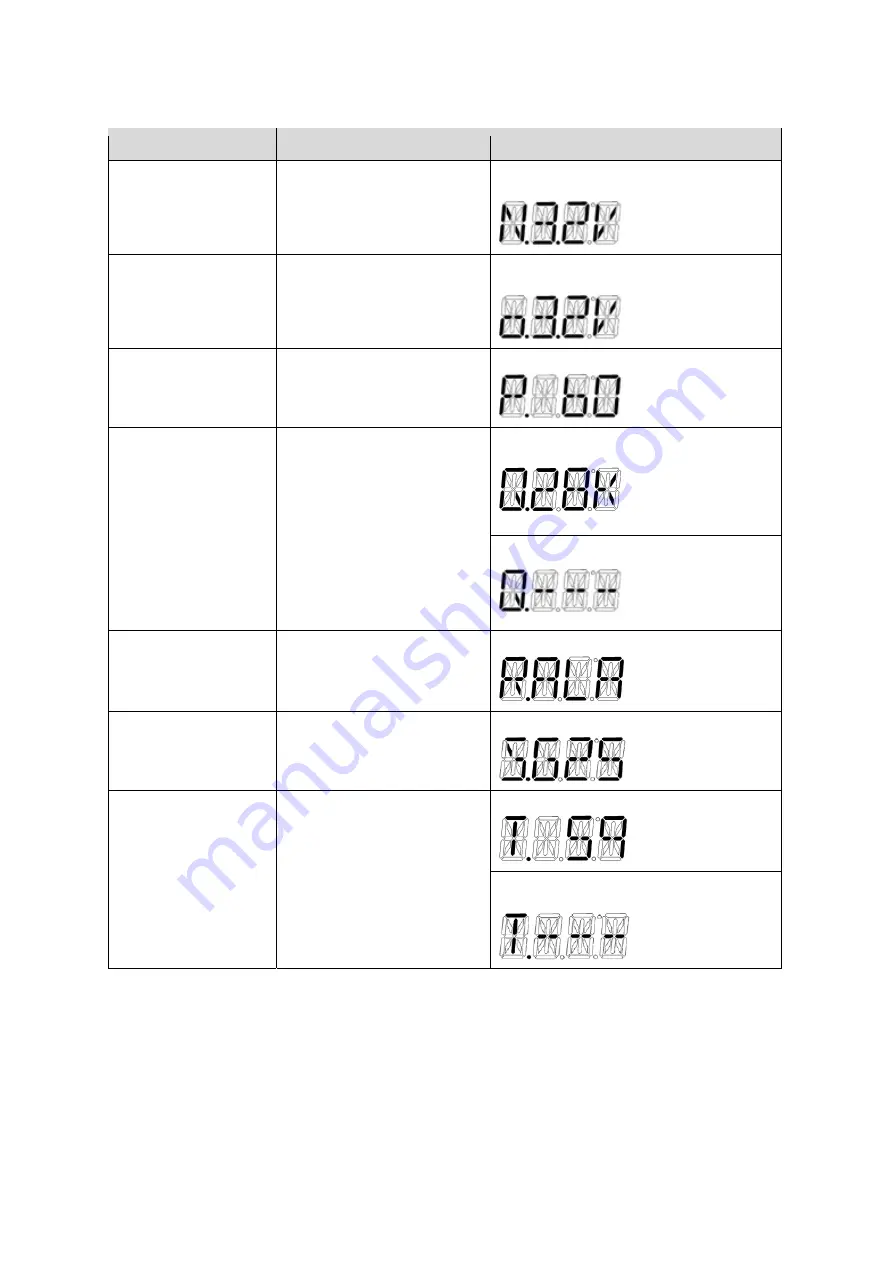
42 NCB Service Manual
Version 1.0
Item
Description
Display
(N) Target APS
The target APS voltage (V) is
displayed.
Displays the APS voltage value to one decimal place.
Eg.) 3.2 V
(O) Current APS
The current APS voltage (V) is
displayed.
Displays the APS voltage value to one decimal place.
Eg.) 3.2 V
(P) Exhaust Gas Temperature
The current exhaust gas temperature
(°C) is displayed.
Eg.) 60
℃
(Q) Model and Capacity
The currently set model and capacity
is displayed.
Eg.) Capacity 28 K
Eg.) Model or capacity setting error.
(R) Burner Type
The currently set burner type is
displayed.
ALA: Alantum
BEK: Bekaert
Eg.) The setting for Alantum.
(S) Gas Type
The current gas type is displayed:
G20, G25/G27, G30, or G31.
Eg.) G25/G27 setting
(T) Last maintenance activity
The number of days since the last
maintenance activity is displayed.
To reset the day count:
- Press [Reset] for 5 seconds.
- Clear the day count.
Eg.) 59 days since the last maintenance activity.
Eg.) Maintenance activity count is disabled. Set to
“0”.
Summary of Contents for NCB-24LSWE
Page 16: ...14 NCB Service Manual Version 1 0 NCB 24 28 34LSWE...
Page 17: ...NCB Service Manual 15 Version 1 0 NCB 40LSWE...
Page 18: ...16 NCB Service Manual Version 1 0 NCB 40LSWE...
Page 60: ...58 NCB Service Manual Version 1 0 4 8 Electrical Diagnostic Contacts and Wiring Diagram...
Page 87: ...NCB Service Manual 85 Version 1 0 Scenario2...
Page 120: ...118 NCB Service Manual Version 1 0 5 2 24 782Error Error occurrence conditions and check items...
Page 140: ...138 NCB Service Manual Version 1 0 Memo...
Page 141: ...NCB Service Manual 139 Version 1 0 Memo...
Page 142: ...140 NCB Service Manual Version 1 0 Memo...