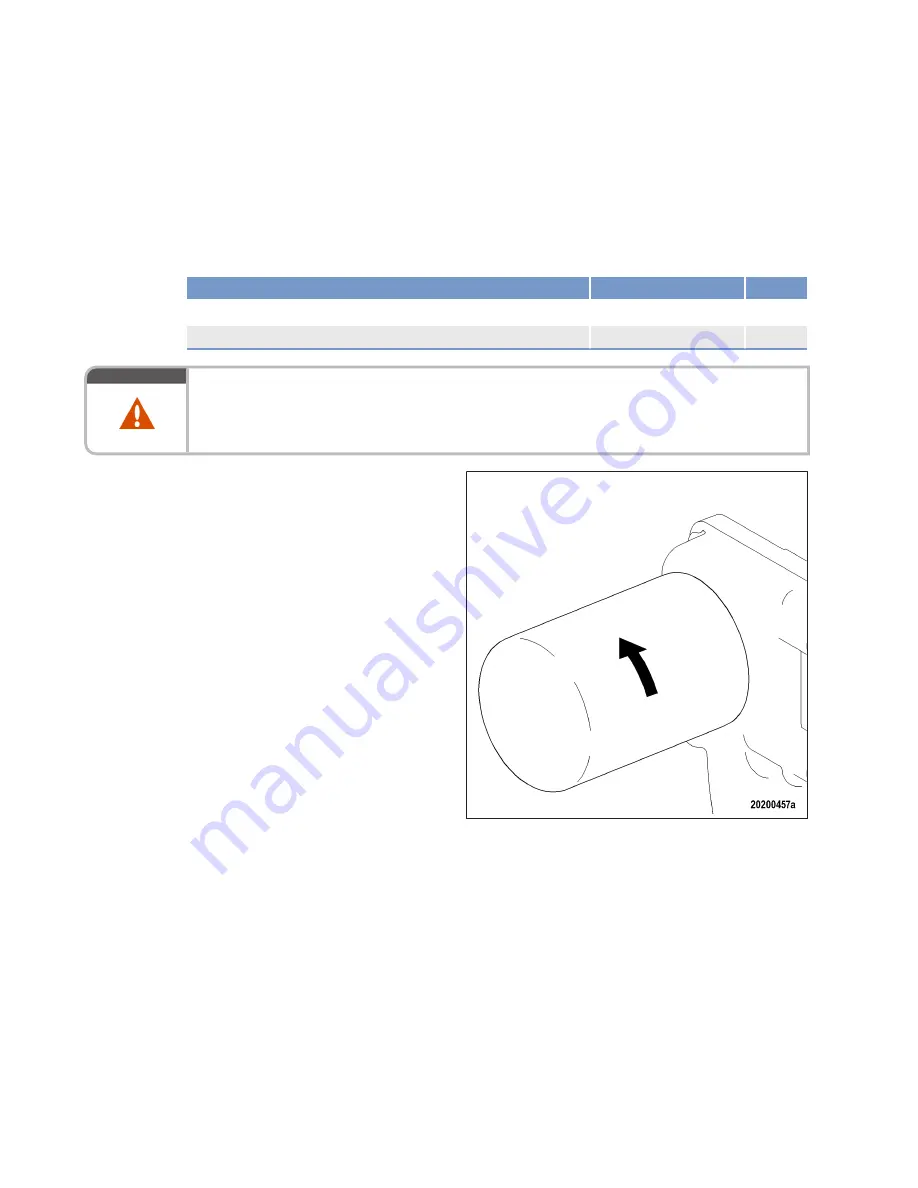
7.15.8 Coolant filter – Replacement
Preconditions
☑ Engine is stopped and starting disabled.
Special tools, Material, Spare parts
Designation / Use
Part No.
Qty.
Oil filter wrench
F30379104
1
Coolant filter
(→ Spare Parts Catalog)
WARNING
Coolant is hot and under pressure.
Risk of injury and scalding!
• Let the engine cool down.
• Wear protective clothing, gloves, and goggles / safety mask.
Coolant filter – Replacement
1.
Turn breather valve of coolant expansion
tank counterclockwise (→ Page 23) to the
first stop and allow pressure to escape.
2.
Continue to turn breather valve counter‐
clockwise and remove.
3.
Remove coolant filter using the oil filter
wrench.
4.
Clean the sealing face on the adapter.
5.
Coat sealing ring of the new coolant filter
with engine oil.
6.
Install and tighten coolant filter by hand.
7.
Close breather valve.
8.
Check coolant level (→ Page 106).
112 | Task Description | M015700/06E 2012-06
TIM-ID: 0000006921 - 004